Single lip oil seals, often overlooked but undeniably crucial components in mechanical systems, play a vital role in maintaining the integrity and efficiency of various machinery. These seals are designed to retain lubricants and prevent the intrusion of contaminants, thereby extending the lifespan and performance of equipment. Their significance cannot be understated, especially in industries where precision and reliability are paramount.
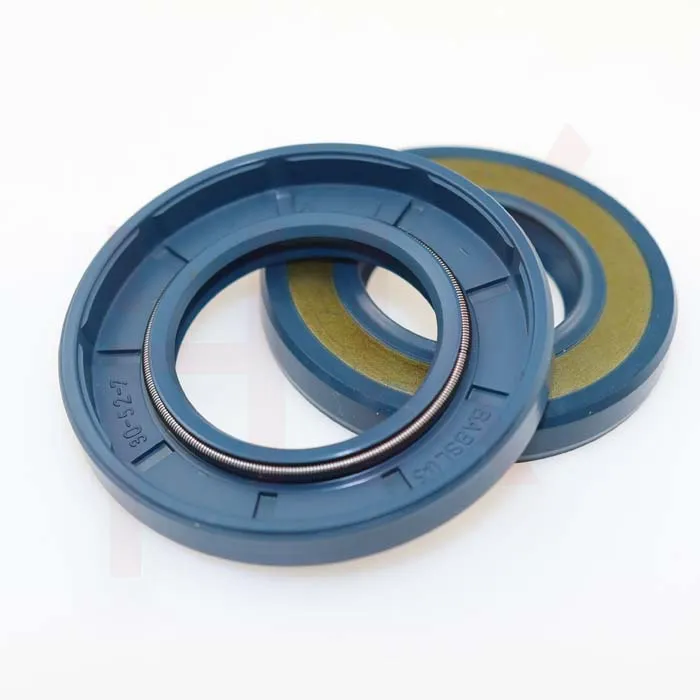
Understanding the intricate workings of single lip oil seals begins with appreciating their structure and function. Comprising a flexible lip secured within a metal or composite casing, these seals create a barrier between the internal and external environment of machinery. The single lip refers to the single point of contact against the rotating shaft, which is sufficient for numerous applications, particularly where moderate sealing is required, and shaft eccentricity is minimal.
Drawing from practical experience, the selection of a single lip oil seal must consider the operational environment. Factors such as temperature extremes, pressure variations, and chemical exposure can significantly impact seal performance. It is crucial to choose materials compatible with the specific conditions. For example, nitrile rubber is an excellent choice for standard applications due to its cost-effectiveness and adequate resistance to oils and wear. However, for higher temperature environments, fluorocarbon is a preferable option, thanks to its superior thermal stability.
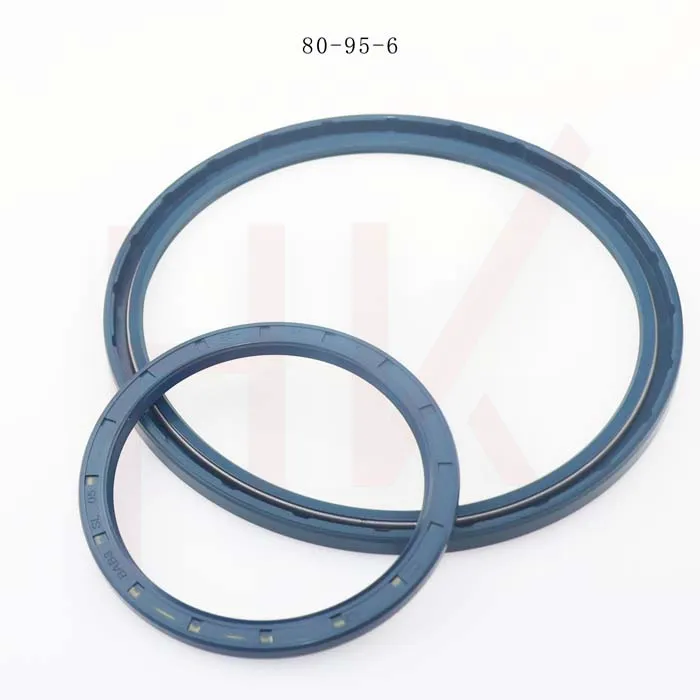
Expertise in the deployment of single lip oil seals involves an understanding of shaft surface finish and hardness. A smooth, hardened surface reduces friction and wear, thus prolonging seal life. Installation expertise is another critical factor; improper installation can lead to premature failure, resulting in increased maintenance costs and potential downtime.
It is advisable to lubricate the lip during installation to minimize startup friction and ensure a snug fit.
single lip oil seal
The authority of single lip oil seals is touted not just through anecdotal success stories but also through empirical evidence and industry benchmarks. Independent studies comparing sealing solutions consistently highlight the efficacy of single lip designs in applications where dual lip seals might offer redundant protection. The simplicity of single lip seals often translates to lower manufacturing costs and simplified maintenance protocols, which are compelling advantages in cost-sensitive operations.
Trustworthiness in these products derives from adherence to international standards and quality assurance practices. Leading manufacturers subject their seals to rigorous testing to ensure reliability under specified conditions. Users are encouraged to seek suppliers who provide clear documentation of compliance with ISO and other relevant certifications, offering peace of mind regarding the integrity of their purchase.
In conclusion, single lip oil seals, though simplistic in design, embody a complex amalgamation of material science, engineering precision, and application-specific knowledge. Their successful integration into machinery is predicated on careful selection, expert installation, and regular maintenance. By ensuring these seals are matched to their intended environment and application, businesses can leverage their reliability to enhance machinery performance, reduce unscheduled repairs, and ultimately, safeguard their operational investments.