Metal-cased oil seals have become an indispensable component in numerous industrial applications. These crucial seals are celebrated for their durability and efficiency in preventing leaks, safeguarding machinery, and ensuring optimal performance. Their construction is typically a blend of rubberized material that grips the shaft tightly, surrounded by a robust metal case designed to withstand extreme conditions. The functional marvel of these seals lies in their ability to maintain lubrication within moving parts, thus, prolonging the lifespan of machinery and reducing maintenance costs.
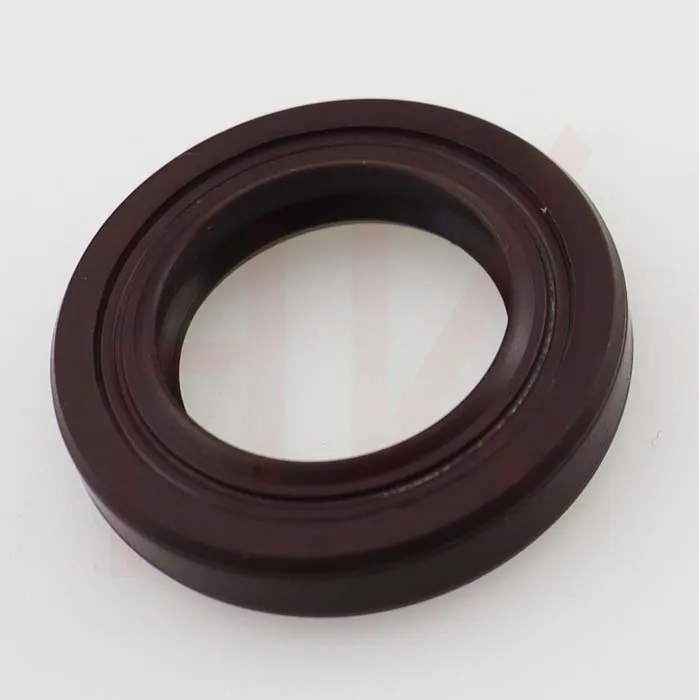
In the field of engineering and manufacturing, selecting the right oil seal can be the difference between interruption-free operations and frequent mechanical breakdowns. Metal-cased oil seals offer advantages that are not only rooted in their construction but also in their adaptability to various environments. They provide exceptional resistance to heat, chemicals, and pressure. This makes them suitable for industries ranging from automotive to aerospace. In automotive applications, these seals are pivotal in axles, steering components, and engines, where temperature fluctuations and exposure to oils and other substances are prevalent.
Furthermore,
metal-cased oil seals excel in heavy machinery settings. For instance, construction equipment and agricultural machines operate under challenging conditions where dust, moisture, and hard impacts are daily concerns. The metal casing provides an added layer of protection against these elements, drastically reducing the probability of contaminant ingress and subsequent equipment failure. Specialists in the industry endorse these seals not merely for their functional prowess but also for their role in enhancing the sustainability of operations by minimizing the need for premature replacements and disposing of worn-out parts.
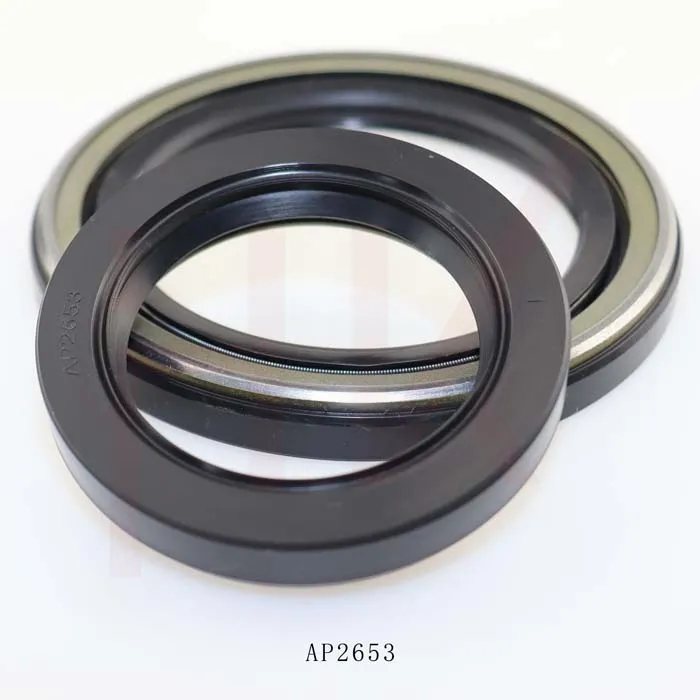
Professional expertise emphasizes the necessity of considering the specific application requirements when selecting metal-cased oil seals. Elements like seal size, material compatibility, and operational environment will dictate the choice of seals. Engineers often rely on detailed specifications and testing to ascertain the seal that aligns perfectly with the operational demands. This profound understanding allows firms to prevent downtime and extend the reliability of their machinery, highlighting the expertise needed to execute these decisions effectively.
metal cased oil seals
Moreover, the authority of metal-cased oil seals is recognized across regulatory bodies and industry standards that dictate safety and performance benchmarks. High-quality seals comply with ISO and other regional certifications, guaranteeing their reliability and performance under specified conditions. Industry professionals and manufacturers that adhere to these guidelines display a commitment to excellence, fostering a sense of trust among clientele and reinforcing their reputations as leaders in their respective fields.
In building trustworthiness, transparency about the seal manufacturing process, quality assessments, and customer support is vital. Suppliers of metal-cased oil seals who provide thorough documentation, including test results, engineering journals, and expert consultations, exemplify a trustworthy partnership model. This transparency ensures that clients are informed about the product’s capabilities and limitations, equipping them to make informed decisions that benefit their operations.
To conclude, metal-cased oil seals represent a pinnacle of engineering achievement, marrying resilience with precision to provide vital protection to countless industrial applications. Their design and utility underscore the importance of expertise, authority, and trustworthiness within the manufacturing and engineering sectors. For companies seeking to maximize their equipment's operational efficiency, investing in high-quality metal-cased oil seals can lead to substantial long-term benefits, proving their worth as a critical asset in safeguarding and enhancing machinery performance.