Rotary oil seals, vital in the world of machinery and engineering, play an indispensable role in maintaining operational efficiency and longevity of equipment. This comprehensive guide delves into the nuances of rotary oil seals, sharing valuable insights backed by years of experience and expertise in the field.
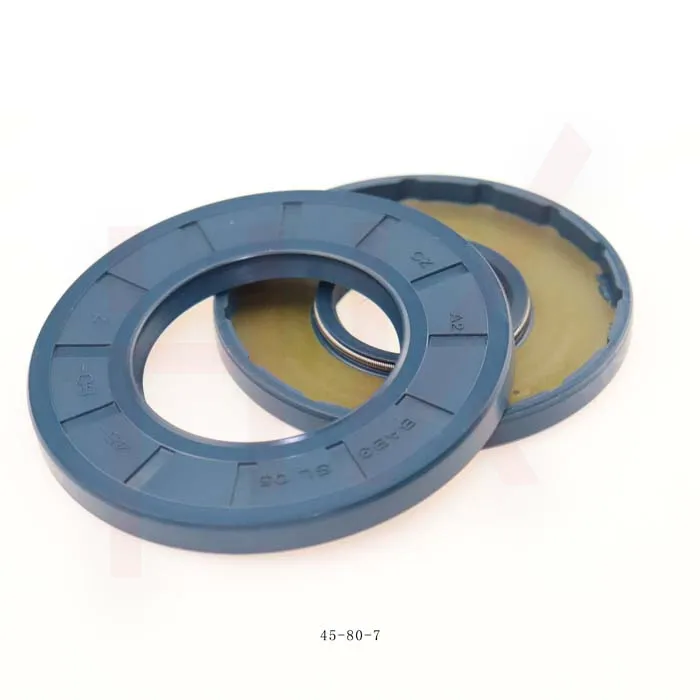
Understanding the Different Types of Rotary Oil Seals
Rotary oil seals are designed to prevent the leakage of lubricants and contaminants, thereby ensuring optimal performance of rotary applications. Various types are available in the market, each engineered for specific applications and operating conditions. Standard rotary shaft seals, for instance, are commonly used in pumps and mixers, serving the primary function of sealing the rotating parts from the stationary ones. Advanced versions, like double-lip seals, come with an added layer of protection, providing enhanced sealing efficiency against environmental contaminants.
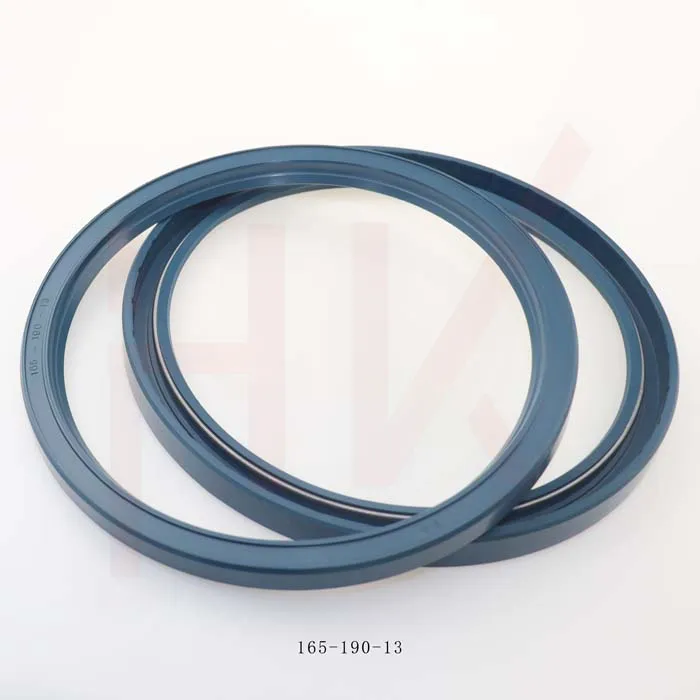
Factors Influencing the Selection of Rotary Oil Seals
Selecting the right rotary oil seal requires meticulous consideration of several critical factors including the operational environment, temperature range, speed of rotation, and the type of lubricant in use. In my extensive experience, failure to choose the appropriate seal often results in premature wear, leading to costly downtime. High-temperature applications necessitate seals made from materials like Viton, known for their excellent thermal resistance properties. For high-speed applications, PTFE seals are often recommended due to their superior low friction characteristics.
Installation Practices for Optimal Performance
Proper installation is paramount to the performance and lifespan of rotary oil seals. A common mistake many make is neglecting the condition of the shaft. Ensuring the shaft surface is smooth and free of blemishes is crucial, as imperfections can lead to seal damage, causing leakage. It's essential to lubricate the seal lip before installation to reduce initial wear and friction. Moreover, using appropriate tools to press the seal into its housing prevents warping and ensures a perfect fit.
Challenges and Troubleshooting in Rotary Oil Seals
rotary oil seals
Despite their robustness, rotary oil seals can encounter issues such as lip wear, spring failure, and chemical degradation.
Identifying the root cause of these problems is critical. Lip wear is often due to excessive heat or contamination, which can be mitigated by regular maintenance and ensuring proper lubricant levels. Spring failure often results from material fatigue, typically resolved by opting for seals with reinforced springs made from durable stainless steel. Chemical degradation can be tackled by selecting seals compatible with the fluids they will encounter.
Innovations in Rotary Oil Seal Technology
Recent advancements have led to the development of seals with smart materials and designs. Self-lubricating seals, for instance, are gaining popularity in applications where continuous lubrication is a challenge. These seals contain embedded reservoirs of lubricant, automatically releasing lubrication as needed, significantly extending service intervals. The integration of IoT technology into seal designs is an emerging trend, facilitating real-time monitoring of seal wear and performance, enabling predictive maintenance and reducing downtime.
Building Trust Through Reliability and Expertise
Relying on reputable manufacturers and suppliers of rotary oil seals is crucial to ensuring quality and reliability. Companies that invest in research and development tend to produce seals that not only meet but exceed industry standards. Engaging with suppliers who offer personalized consultation services can dramatically enhance your seal selection process, ensuring that you choose the correct seal type tailored to your specific application needs.
The Future of Rotary Oil Seals
Looking forward, the evolution of rotary oil seals will undoubtedly be shaped by advances in material science and engineering. The growing emphasis on eco-friendly materials is likely to spawn a new generation of bio-degradable seals, reducing environmental impact. Additionally, the push towards automation and smart manufacturing will see greater integration of sensors within seal systems, offering unprecedented levels of control and assurance in industrial operations.
Rotary oil seals remain a pivotal component in the machinery sector, and making informed decisions regarding their selection and maintenance can lead to significant improvements in equipment efficiency and lifespan. By combining theoretical knowledge with hands-on experience, and maintaining an openness to new developments and technologies, businesses can maximize the potential of these essential components.