In the intricate world of sealing technology, rotary lip seals play an indispensable role in ensuring efficiency and reliability across a myriad of applications. Whether it’s in the automotive industry, heavy machinery, or specialized industrial equipment, the importance of a high-quality rotary lip seal cannot be overstated. This article delves into the experience-driven insights, expertise, authority, and trustworthiness of rotary lip seals, illustrating why they are a fundamental component in modern engineering applications.
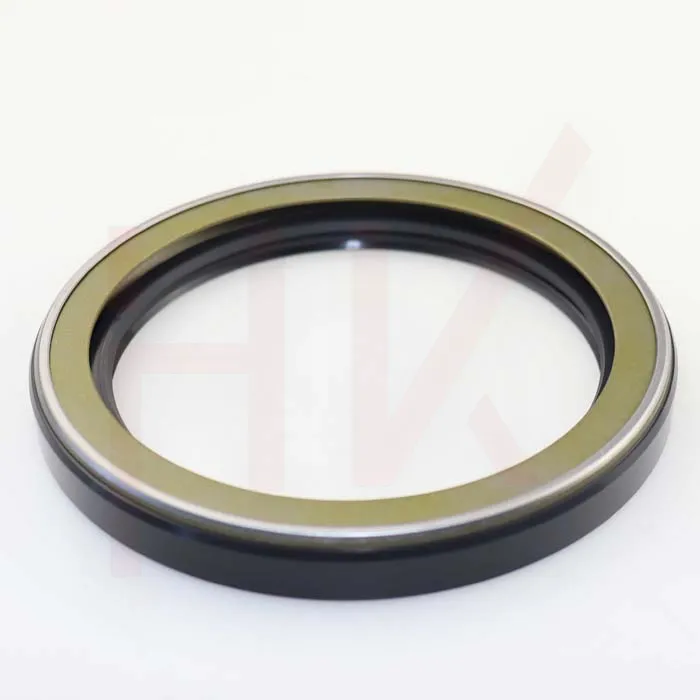
Rotary lip seals are designed to retain lubricants, exclude contaminants, and maintain operational integrity under varying pressure and speed conditions. The experience of those in the industry who have worked hands-on with these seals reveals that the choice of material and design can significantly impact the seal’s performance. Fluoroelastomer and PTFE (polytetrafluoroethylene) are among the popular choices for seal materials due to their excellent thermal stability and resistance to aggressive chemicals. Engineers with years of experience have noted that PTFE's non-reactive nature makes it ideal for high-temperature environments, while fluoroelastomer seals excel in automotive applications where exposure to fuels and engine oils is common.
Expertise in the field of rotary lip seals comes from a deep understanding of their functional mechanisms and the nuances of their applications. It’s crucial for engineers to comprehend the intricacies of lip geometry and the dynamic sealing action it facilitates. Lip design, encompassing aspects like contact pressure and the inclusion of dust lips, determines the seal’s effectiveness in dynamic conditions. The dual-lip design is often recommended for applications where additional protection against contamination is necessary. Experts often simulate challenging operational conditions to test the limits of seal performance, thus ensuring that the rotary lip seal can withstand real-world conditions.
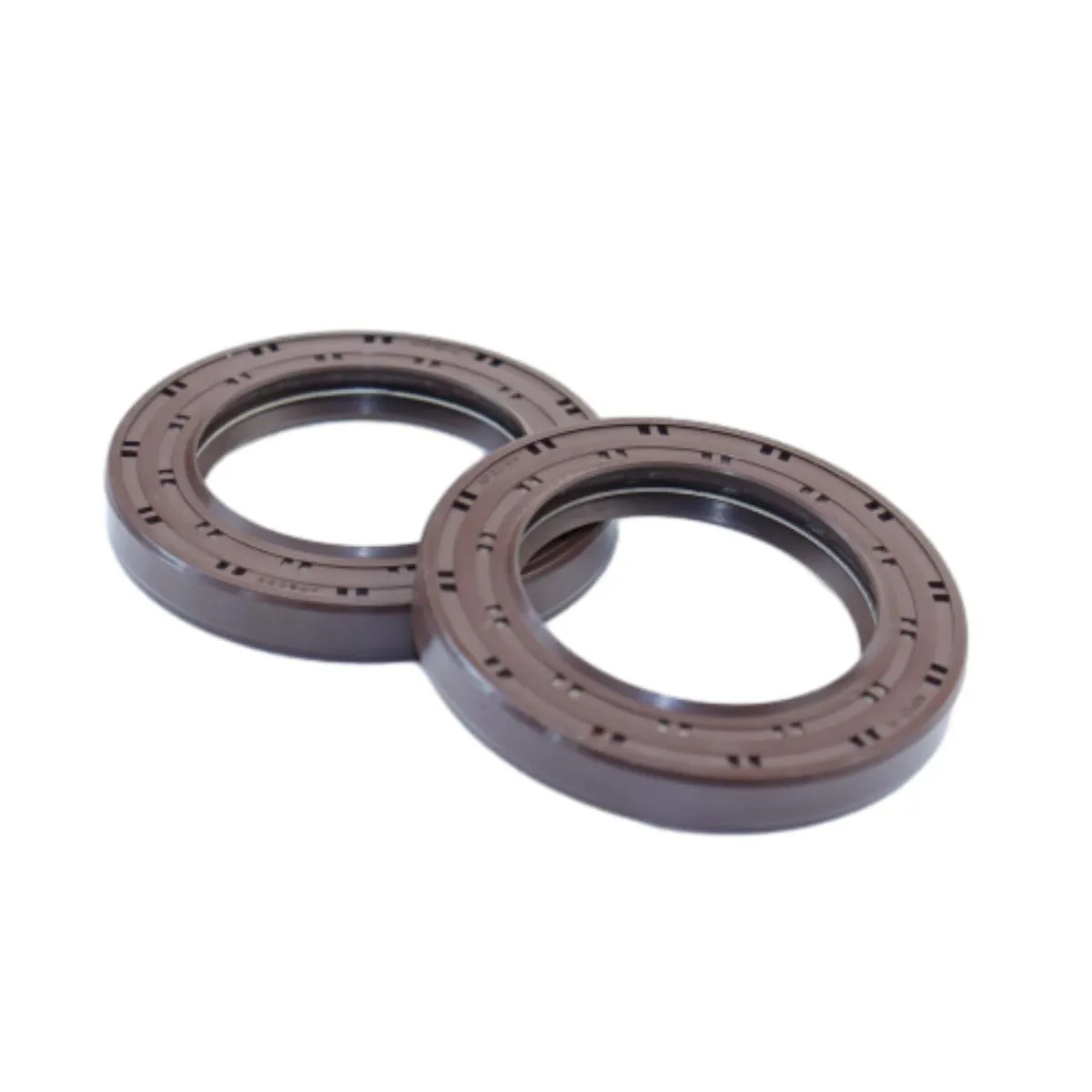
Rotary lip seals are an authoritative choice in industries that demand reliability and efficiency. Their application in the automotive sector, for instance, underscores their reputation for reducing friction and wear, which in turn extends the life of the engine and other mechanical systems. This authority is further consolidated by the fact that rotary lip seals are a preferred choice in aerospace and marine applications, where failure is not an option. A precise understanding of pressure differentials and rotational speeds characterizes the authority of manufacturers who set industry standards.
rotary lip seal
Trustworthiness in rotary lip seal applications is built through rigorous testing and validation processes. Manufacturers who are at the forefront of this industry invest substantially in research and development to ensure their products meet stringent international quality standards. This trust is exemplified by certifications such as ISO 9001, which affirm the manufacturer’s commitment to quality, safety, and consistency. End-users, relying on these seals for critical applications, can depend on their proven track record of performance and durability.
Testimonials from industry professionals and long-term users further reinforce the trust in rotary lip seals. Case studies highlight instances where seals have operated without fail for thousands of hours, thereby saving substantial costs in maintenance and downtime. The predictive maintenance benefits offered by using advanced rotary lip seals are substantial, as they can alert to potential failures before they occur, using data-driven insights.
In conclusion, the experience, expertise, authority, and trustworthiness of rotary lip seals make them an essential component in high-stakes industrial environments. Their ability to perform under diverse conditions, maintain system efficacy, and guarantee safety allows engineers and industries to push the boundaries of what they can achieve. As technology advances, rotary lip seals will continue to evolve, offering even more reliable solutions to sealing challenges across various sectors, thereby cementing their place as a cornerstone in engineering and production processes.