Replacing seals in a hydraulic cylinder is an essential task for maintaining the efficiency and longevity of hydraulic systems used across various industries, including construction, manufacturing, and agriculture. Understanding the intricacies of hydraulic seal replacement ensures that systems operate smoothly, reducing downtime and enhancing productivity.

Hydraulic cylinders depend on a series of seals to maintain pressure, control leaks, and exclude contaminants. Over time, seals can wear out due to factors like excessive pressure, contamination, heat, and age. When this happens, it's crucial to address the issue promptly to prevent more severe damage to the hydraulic system.
Here's a detailed guide on how to effectively replace seals in a hydraulic cylinder, emphasizing precision and care
1. Preparation and Safety Before beginning any repair work, ensure that the hydraulic system is completely depressurized. This involves disconnecting the power source and relieving any stored pressure in the system to prevent accidents or injury. Proper safety gear, such as gloves and goggles, should be worn to protect against hydraulic fluid contact.
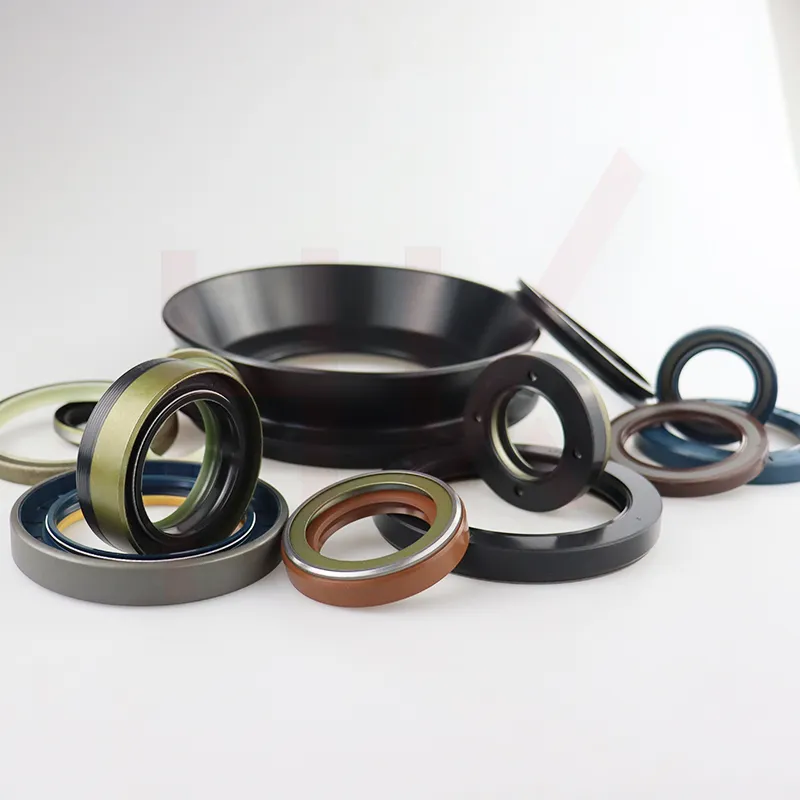
2. Disassembly Carefully remove the hydraulic cylinder from the machinery following the manufacturer's guidelines. It's crucial to document the disassembly process, taking notes or photos to ensure an accurate reassembly. This attention to detail is vital for locating the seals and understanding how they fit within the cylinder assembly.
3. Inspection of Components Once disassembled, inspect all internal components of the cylinder for wear and damage. This includes the piston, rod, barrel, and any bushings. Look for scratches, dents, or abnormalities that could affect the cylinder's operation. Identifying these issues helps ensure that a simple seal replacement will suffice rather than needing a more extensive overhaul.
replacing seals in a hydraulic cylinder
4. Seal Selection and Compatibility Choosing the right seals is critical. They must be compatible with the specific hydraulic fluid used, the operating temperatures, and pressure ranges of the system. High-quality seals made from robust materials like polyurethane or nitrile rubber are recommended for their durability and resistance to wear.
5. Seal Replacement Remove the old seals using appropriate tools that do not damage the surrounding components. Installing new seals requires cleanliness and precision to prevent contamination and ensure a snug fit. It's imperative to follow the correct orientation and alignment of the seals as per the manufacturer's specifications.
6. Reassembly Reassemble the hydraulic cylinder carefully, reversing the disassembly steps. Maintain a clean work environment to avoid introducing dirt or debris into the cylinder. Accurate alignment and correct torque settings for bolts and fasteners are crucial to prevent leaks and ensure efficient operation.
7. Testing and Troubleshooting After reassembly, test the hydraulic system for correct operation at low pressure before gradually increasing to full capacity. Monitor the system for any signs of leakage or irregular function. If issues persist, additional troubleshooting might be necessary, which could involve rechecking seal placement or considering other potential problems within the system.
Replacing hydraulic cylinder seals is a task that demands attention to detail, precision, and a methodical approach. By following these guidelines, technicians can ensure that the hydraulic system remains in peak operational condition, extending the life of machinery and reducing the risk of costly breakdowns. This proactive maintenance approach confirms expertise in handling complex hydraulic systems, thereby establishing trustworthiness and reliability in operations management.