Replacing seals on a hydraulic cylinder is a critical maintenance task that requires precision, expertise, and attention to detail. The hydraulic cylinder is an indispensable component in numerous industrial applications, including construction equipment, manufacturing machinery, and agricultural implements. Proper seal maintenance not only ensures optimal performance but also extends the life of the hydraulic system. Here, we delve into the meticulous process of seal replacement, highlighting key considerations and the technical expertise required.
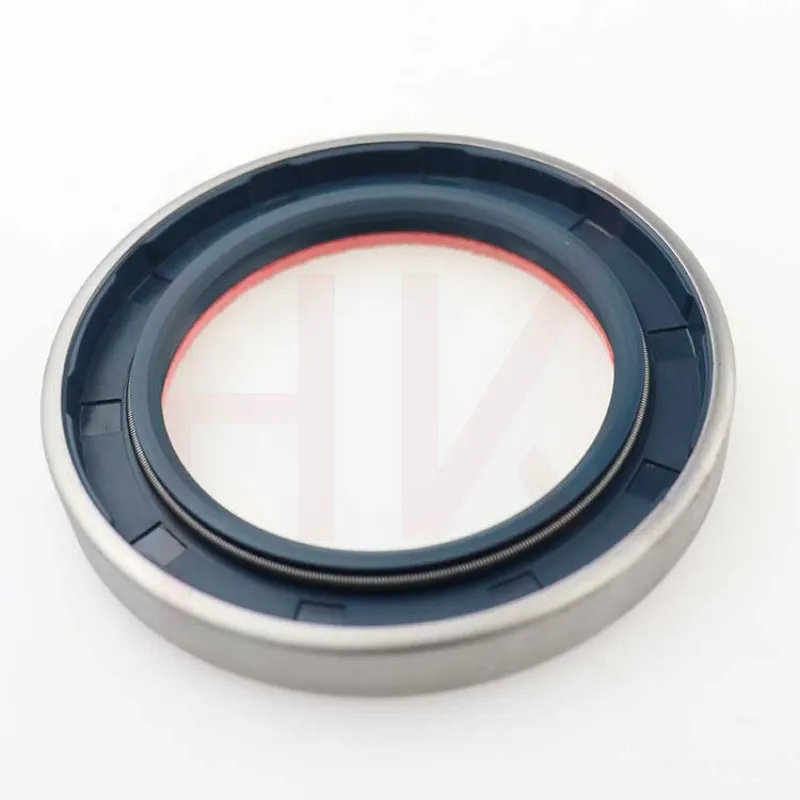
Identifying the Need for Seal Replacement
The first step in seal replacement involves recognizing symptoms of seal failure. Common indicators include fluid leaks, decreased performance, and abnormal sounds or movements from the hydraulic cylinder. These symptoms can result from factors such as wear and tear, contamination, or environmental conditions. Regular inspections and preventative maintenance can preemptively identify these issues, minimizing downtime and preventing costly repairs.

Selection of Appropriate Seals
The selection of appropriate seals is crucial for the hydraulic cylinder's performance. Seals are made from various materials, such as polyurethane, rubber, or PTFE, each suited to specific applications and environments. The choice of material depends on several factors including operating pressure, temperature, and the type of hydraulic fluid used. Consulting the cylinder manufacturer's specifications or a hydraulic systems expert can provide authoritative guidance in selecting the proper seal.
Disassembly of the Hydraulic Cylinder
Once the need for seal replacement is confirmed, the hydraulic cylinder must be carefully disassembled. This involves releasing pressure and fluid from the system, followed by the removal of the cylinder from the machinery. It is essential to perform this task methodically to avoid damaging components or causing harm. Expertise in handling hydraulic equipment is imperative to ensure safety and efficiency during disassembly.
Removal of Old Seals
replacing seals on a hydraulic cylinder
After disassembly, the next step is to remove old seals from the cylinder. This requires specialized tools designed to extract seals without damaging the piston or cylinder bore. It is a process that demands precision and experience, as any damage can compromise the cylinder's integrity. Ensuring cleanliness and avoiding contamination is vital during this phase to maintain the hydraulic system’s reliability.
Installation of New Seals
Installing the new seals requires a meticulous approach. Each seal must be properly oriented and seated in its designated groove. Professionals often use assembly lubricants to facilitate this process, ensuring a snug fit without causing the seal to twist or tear. Expertise in the correct installation method for each seal type contributes greatly to the system's longevity and performance.
Reassembly and Testing
Once new seals are in place,
the hydraulic cylinder is reassembled with care. It is crucial to follow a sequential approach as advised by the manufacturer or technical manuals. After assembly, testing the cylinder is necessary to confirm successful seal placement. This involves checking for leaks, ensuring smooth operation, and validating that the system holds pressure. Professionals rely on both visual inspections and pressure tests to guarantee the hydraulic cylinder meets operational standards.
Authoritative Maintenance Practices
Trustworthy hydraulic seal maintenance involves not only the initial replacement but ongoing monitoring and care. Implementing a routine maintenance program ensures early detection of potential issues. Utilizing high-quality seals from reputable manufacturers enhances system performance and reliability. Partnering with knowledgeable service providers or in-house technicians who are trained and certified in hydraulic systems boosts trustworthiness and effectiveness.
By understanding the intricacies of replacing seals on a hydraulic cylinder, businesses can maintain the efficiency and effectiveness of their equipment. The expertise required for this process underlines the importance of professional involvement and adherence to best practices. Investing in reliable seal maintenance prolongs the life of machinery, reduces costs associated with repairs and downtime, and optimizes operational productivity.