Replacing seals in a hydraulic cylinder is a crucial maintenance task that ensures the efficient operation and longevity of hydraulic systems. In the realm of heavy machinery and fluid mechanics, the seamless functioning of hydraulic cylinders directly impacts performance and reliability. One of the primary components sustaining this functionality is the set of seals within the cylinder. These seals prevent fluid leakage, maintain pressure, and protect the system from contaminants.
Here's a comprehensive guide to understanding the process and importance of replacing seals in hydraulic cylinders.
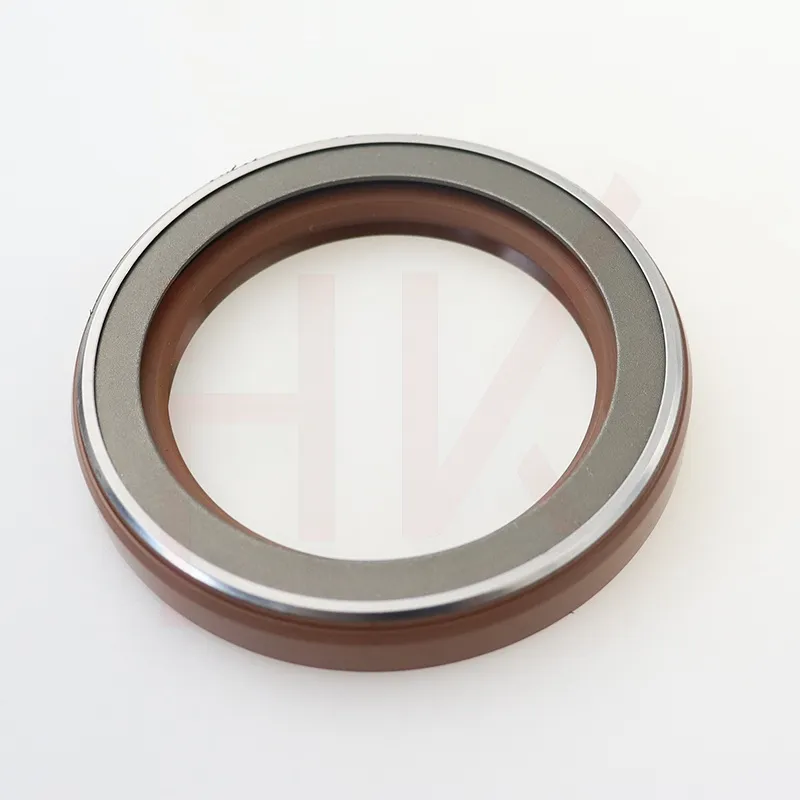
Hydraulic cylinders operate under intense pressure, often in challenging environments. Over time, the seals inside these cylinders deteriorate due to friction, heat, and exposure to various industrial elements. As an expert in hydraulic systems, the first step in addressing seal replacement is correctly diagnosing the issue. Common signs that seals need replacement include visible fluid leaks, decreased system efficiency, and unusual noise during cylinder operation.
The process of replacing seals begins with obtaining the correct seal kit specific to your hydraulic cylinder model. It is critical to consult the manufacturer's documentation or an experienced supplier to ensure compatibility. Using incorrect seals may lead to premature failure and system damage, compromising the safety and effectiveness of the equipment.
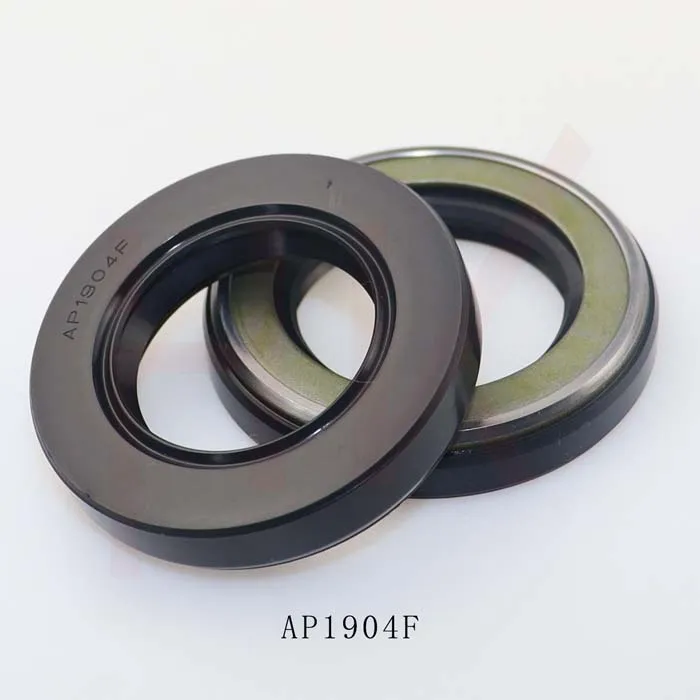
Once the appropriate seal kit is at hand, the cylinder must be safely removed and disassembled. This step requires a clean, spacious working environment equipped with the necessary tools such as wrenches, seal picks, and grease. Expertise is essential here, as hydraulic cylinders consist of a series of precisely engineered components. Any mishandling during disassembly can lead to irreparable damage, highlighting the importance of technical proficiency.
In disassembling the cylinder, it is crucial to document each step meticulously. This records the arrangement and orientation of components, facilitating effortless reassembly. The integrity of the piston, rod, and cylinder barrel should be inspected for wear and damage. If any additional issues are identified, they should be addressed before proceeding with seal replacement.
replacing seals hydraulic cylinder
Installation of new seals requires attention to detail and adherence to installation instructions. The seals must be correctly oriented to function effectively. Using the correct lubricants is vital for ensuring proper alignment and preventing premature wear. This step embodies professional expertise, as improper seal installation is a common cause of failure in hydraulic systems.
After seal installation, reassembly of the cylinder should follow, replicating the disassembly steps in reverse order. Reassembled cylinders must be tested for system integrity and performance. This testing phase confirms the success of the seal replacement and identifies any persistent or new issues before the cylinder is reinstalled into the machinery.
Trustworthiness and reliability in hydraulic systems are significantly enhanced by regular maintenance practices such as timely seal replacements. This preventative measure not only extends the life of the cylinder but also enhances safety and efficiency in operation. By prioritizing high-quality seal replacements, businesses can significantly reduce downtime, ensuring continuous productivity and operational excellence.
In conclusion, replacing hydraulic cylinder seals is a detailed process that necessitates a high level of expertise and careful attention. For those who lack the technical skills, consulting a professional is recommended. This ensures that the work is done correctly, achieving the desired improvements in hydraulic system performance while safeguarding against potential mechanical hazards. With the right approach, hydraulic systems can offer sustained, reliable service, underscoring the importance of skilled maintenance practices in industrial settings.