Replacing seals in a hydraulic cylinder stands as a critical maintenance task that ensures the long-term reliability and efficiency of hydraulic systems. This task is synonymous with preserving the lifeblood of various mechanical operations, where hydraulic systems are paramount. Through years of handling hydraulic systems both in the field and at workshops, I've gathered in-depth experience, which I’ll share to guide those seeking the best practices and insights into successfully replacing hydraulic seals.
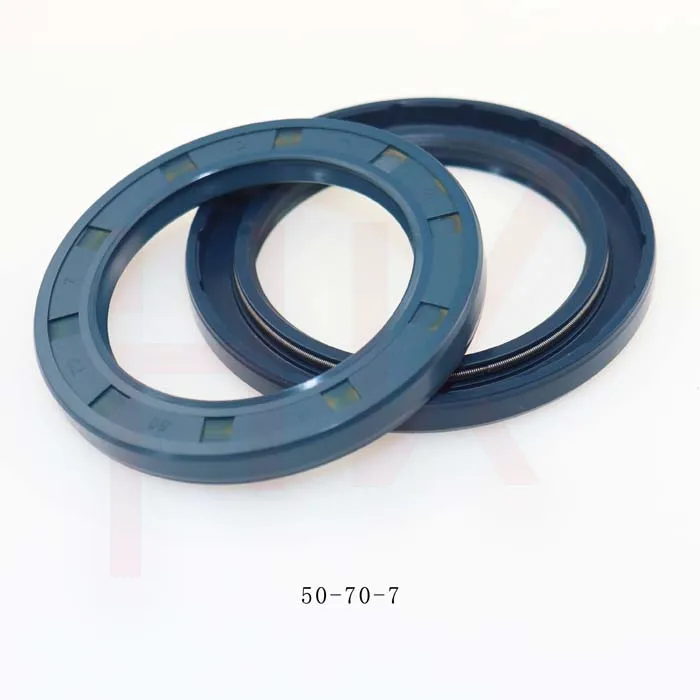
Hydraulic cylinders are essential components in heavy machinery, agriculture, and construction equipment. The seals within these cylinders are vital for maintaining pressure, preventing leaks, and ensuring the smooth operation of the machinery. When a seal fails, the performance of the entire system is compromised. This makes understanding the replacement process and recognizing signs of wear imperative for ongoing machinery efficiency.
Identifying the need for seal replacement often begins with observing common symptoms of seal failure. These include visible oil leaks around the cylinder, decreased hydraulic pressure, sluggish operation, and unusual noises during cylinder movement. By staying vigilant to these signs, equipment operators can prevent more severe damage and costly repairs.
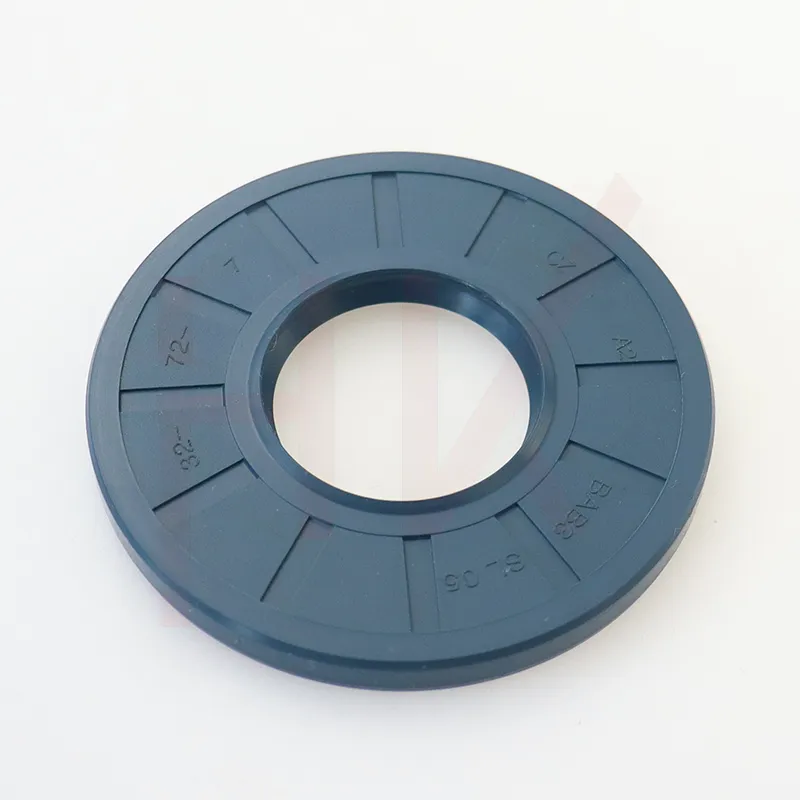
The process of replacing seals in a hydraulic cylinder involves several meticulous steps. Firstly, one must ensure the hydraulic system is safely depressurized to prevent any accidents. Safety is paramount, and using the appropriate personal protective equipment (PPE) cannot be overstated.
Disassembling the cylinder requires a delicate touch and familiarity with the cylinder’s design, as they vary across different models and manufacturers. Keeping the components organized during disassembly can significantly ease reassembly. It's advisable to consult the manufacturer's manual for specific instructions tailored to the particular cylinder model.
Upon removal of the old seals, a thorough inspection of the cylinder's interior is crucial. Look for any signs of scoring or damage that may have contributed to seal failure. If damage is found, it might necessitate further repairs or component replacements.
replacing seals in a hydraulic cylinder
When selecting new seals, it is essential to procure seals that match the specifications of the original manufacturer. Using inferior or mismatched seals could result in premature failure, compromising the integrity of the hydraulic system. Quality seals typically come with precise manufacturing standards, ensuring durability and fitment.
Installation demands precision and cleanliness. Any contaminants introduced during this process could potentially damage the new seals or degrade their lifespan. Applying a light coating of hydraulic oil can facilitate the installation, and using specialized tools for fitting seals can prevent damage during placement.
After completing the replacement,
reassemble the cylinder with care. Each part should be securely refastened in the correct order. Following reassembly, gradually reintroduce pressure and perform a series of function tests to confirm the integrity of the new seals and the operation of the cylinder. Monitoring for leaks and operational efficiency is crucial in the first few hours following replacement.
Throughout my career, clients and fellow professionals have consistently found that routine maintenance and proactive inspections play pivotal roles in extending the lifespan of hydraulic seals. By planning regular maintenance checks, one can often preempt potential failures and optimize machinery uptime.
For those keen on mastering hydraulic cylinder maintenance or expanding their expertise, comprehensive training programs and workshops are highly recommended. Understanding the nuances of hydraulic systems can position professionals as authorities in the field, enhancing trust and reliability in their skills and services.
In summary, replacing seals in a hydraulic cylinder is a procedure that demands attention to detail and a commitment to best practices. By approaching this task methodically, professionals can ensure their hydraulic systems continue to operate smoothly, reflecting their expertise and dedication to excellence in mechanical maintenance.