Oil seals, often referred to as rotary shaft seals, are essential components in a wide range of mechanical systems. Their primary purpose is to prevent the leakage of oil and other fluids while protecting the equipment from dirt, dust, and other contaminants. Understanding the nuances of oil seals can be critical for optimal performance across various industries, including automotive, aerospace, manufacturing, and more.
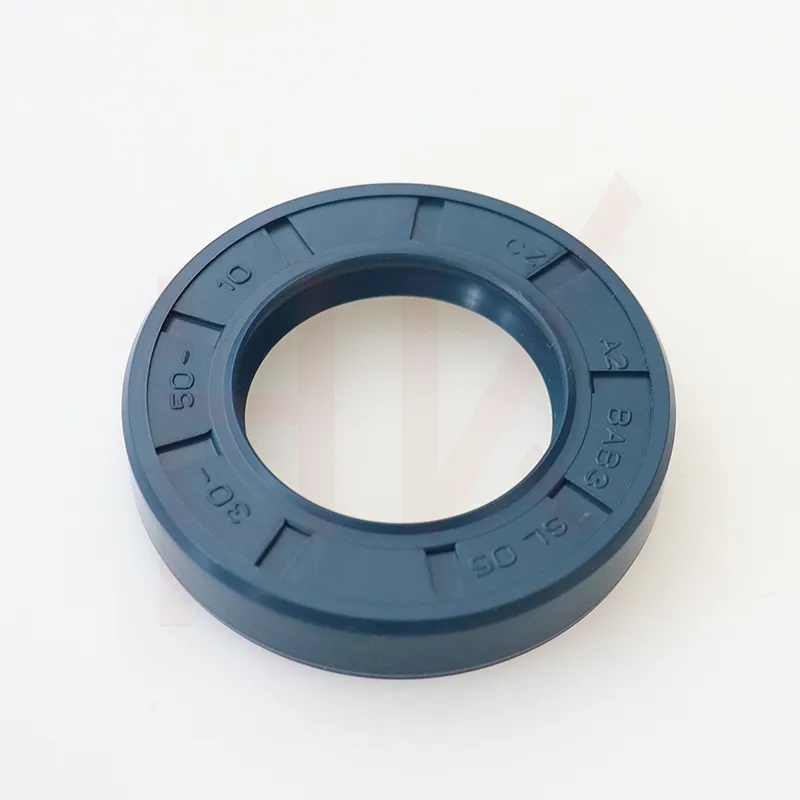
Oil seals are manufactured using different materials, each suited to specific conditions. For example, nitrile rubber is commonly used due to its affordability and resistance to oil and fuel. However, when operating under high temperatures or in contact with aggressive chemicals, fluorocarbon (Viton) offers superior performance. Selecting the appropriate material for oil seals can dramatically increase the lifespan of machinery by minimizing wear and tear, thus ensuring reliability and reducing maintenance costs.
The design of oil seals varies significantly, depending on the application. The most common types include single lip, double lip,
and specialized designs such as labyrinth seals. Single lip seals are most effective in low-pressure environments where contamination control is critical. In contrast, double lip seals provide additional security, incorporating a secondary lip to protect against contaminants. These seals are particularly beneficial in environments where debris and dust are prevalent.
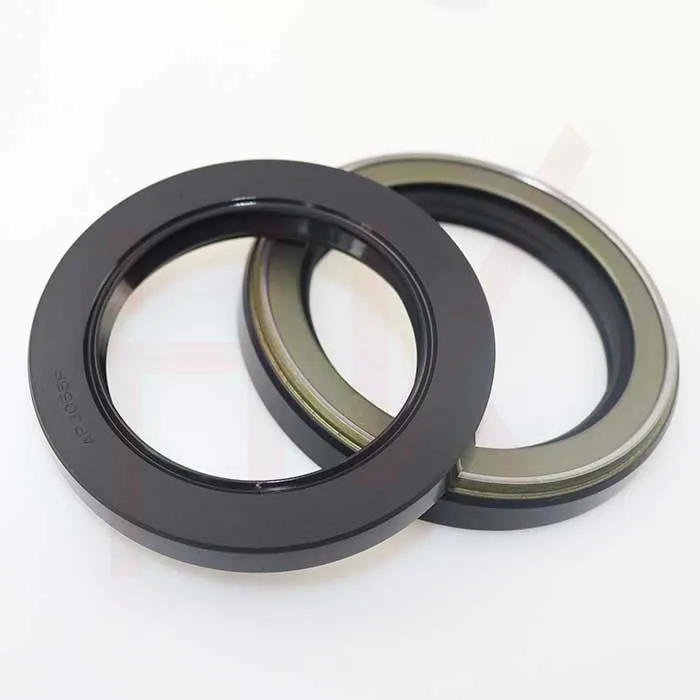
Precision installation of oil seals is a critical factor in achieving maximum operational efficiency. Incorrect installation can lead to premature failure, resulting in leakage and equipment damage. It is crucial that the sealing lip face is perpendicular to the shaft and that there is adequate lubrication to prevent drying and overheating. Furthermore, using proper installation tools can help ensure a perfect fit and avoid seal deformation, which is a common cause of leakage.
The role of oil seals becomes even more apparent when examining industry-specific applications. For instance, in the automotive sector, oil seals play a vital role in the function of engines and gearboxes. They maintain essential lubrication within motor components, significantly impacting a vehicle's performance and longevity. In industrial machinery, oil seals are tasked with preserving the integrity of the lubricant, protecting bearings and shafts from contaminants that could lead to system failure.
oil seals
Innovations in oil seal technology have introduced enhanced materials and designs that push the boundaries of performance and durability. Advances such as PTFE materials offer reduced friction and wear resistance, ultimately leading to longer seal life and reduced energy consumption. As industries move toward more sustainable practices, these innovations are not only cost-effective but also environmentally friendly.
Technical advancements further extend into the production of oil seals, where computer-aided design and automated manufacturing ensure high precision and consistency. These technologies enable the mass production of complex seal designs that once required extensive manual labor. The result is a product that consistently meets rigorous standards, providing end-users with reliable seal performance across diverse applications.
Maintaining oil seals is a matter of following best practices in machinery maintenance. Regular inspection and timely replacement at the first signs of wear can prevent catastrophic failures. Investing in high-quality seals and understanding their role in system performance are what establish best practices in asset management.
Oil seals may be small, but their significance in the world of machinery cannot be overstated. They offer an indispensable line of defense against fluid leakage and contamination, directly impacting the efficiency and dependability of various systems. In light of technological advancements and a greater understanding of materials and applications, oil seals continue to evolve, promising greater efficiencies and ensuring that industries worldwide keep moving forward reliably and sustainably. Their pivotal role underscores the importance of selecting the correct seal for the specific application, a decision that hinges on expertise, experience, and an understanding of industry trends.