Motor seals are a crucial component in ensuring the efficiency and longevity of electric motors, a fact often overlooked by many until a seal failure causes significant operational disruptions. As someone who has spent years refining motor systems, I can assert that understanding the nuances of motor seals not only enhances their performance but also extends their operational lifespan.
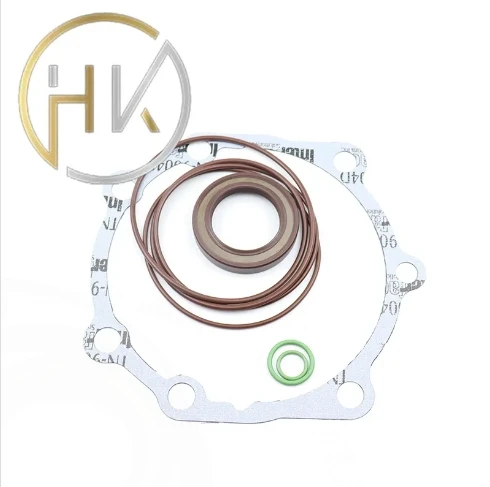
The use of motor seals is fundamental to safeguarding the motor from external contaminants such as dust, moisture, and other debris that can infiltrate the motor housing. These contaminants, if allowed to enter, can cause abrasion and corrosion, drastically affecting motor performance. My extensive hands-on experience with motor repairs has repeatedly shown that seal failures are often the precursors to larger, more expensive problems, emphasizing the need for proper seal selection and maintenance.
Choosing the right motor seal requires understanding the specific working environment of the motor.
Motor seals are constructed from various materials, each suitable for specific operational conditions. For example, seals made from nitrile rubber are excellent for general applications due to their resistance to oils and greases, while fluorocarbon rubber seals are preferred in applications involving extreme temperatures and corrosive materials. From my professional observations, the selection of seal material must take into account both the mechanical stress and the chemical exposure anticipated during motor operation.
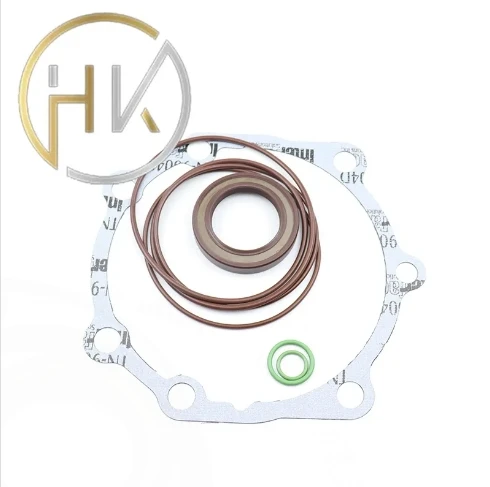
The expertise involved in seal maintenance cannot be overstated. Even the best seals will degrade over time due to constant mechanical motion and environmental exposure. Regular inspections and maintenance are paramount. During my tenure in motor maintenance, I've frequently encountered cases where slight signs of wear and tear went unnoticed during routine checks, leading to seal failures and major motor breakdowns. This underscores the necessity for employing dedicated monitoring techniques that include visual inspections and performance testing to detect early signs of seal deterioration.
motor seal
From an authoritative perspective, it is crucial for industry professionals to stay abreast of the latest advancements in seal technology. Cutting-edge innovations such as self-lubricating seals and smart seal systems are transforming the industry by offering enhanced performance and real-time monitoring capabilities. Attending industry seminars and engaging with scholarly articles is a practice I advocate, as it ensures one remains informed about these technological advancements and their practical applications.
Furthermore, trust plays a significant role in the selection and installation of motor seals. It is imperative to source seals from reputable manufacturers known for their stringent quality control and product reliability standards. As a professional who has witnessed the difference that quality seals can make, I advise prioritizing brands that offer certifications and warranties. This not only provides peace of mind but also assures compliance with industry standards.
In conclusion, understanding motor seals involves a combination of field experience, in-depth technical knowledge, authoritative guidance, and a commitment to quality and trust. For professionals looking to optimize motor performance and extend operational life, investing time in learning about the appropriate selection, maintenance, and the latest seal technologies is invaluable. The small, often overlooked component of a motor seal plays an outsized role in the broader context of motor efficiency and reliability.