Hydraulic seals play an indispensable role in the operation of hydraulic equipment, facilitating the conversion of fluid power into mechanical force and motion. At the heart of this process, seals prevent leaks and maintain pressure, ensuring the efficiency and safety of the entire hydraulic system. However, even the most robust seals can succumb to wear and tear over time, leading to the necessity for hydraulic seal repair. Understanding this repair process is crucial for minimizing downtime, reducing costs, and maximizing equipment longevity.
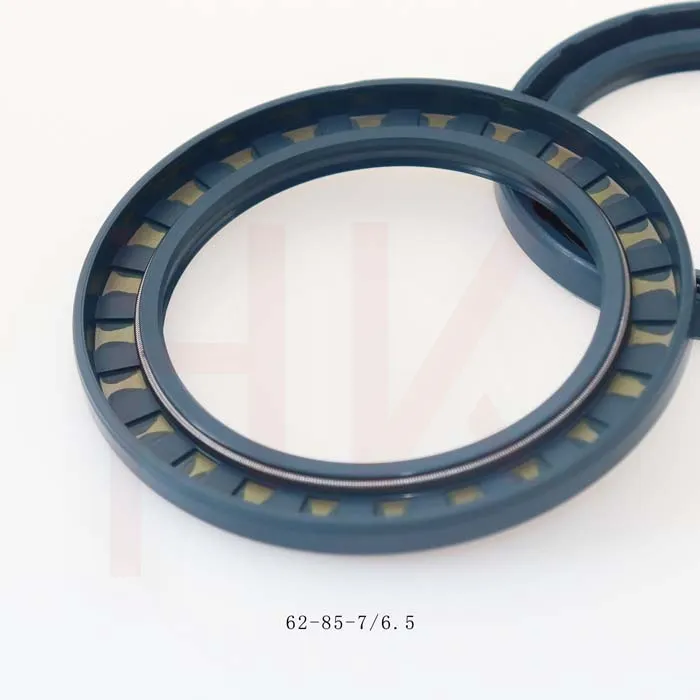
From a wealth of hands-on experience in hydraulic system maintenance, one can attest to the fact that the repair of hydraulic seals requires precision and a comprehensive understanding of system dynamics. A typical hydraulic seal may fail due to a variety of reasons, including contamination, improper installation, excessive pressure, or material degradation. Identifying the root cause of seal failure is the first step in crafting an effective repair strategy.
Expertise in hydraulic seal repair extends beyond the mere replacement of worn-out components. It demands a thorough inspection of the entire hydraulic system.
This step is not merely diagnostic but is preventative as well. During inspection, it's vital to check for irregularities such as scratches or pits on the rod and cylinder surfaces, as these imperfections can lead to premature seal wear even after replacement.
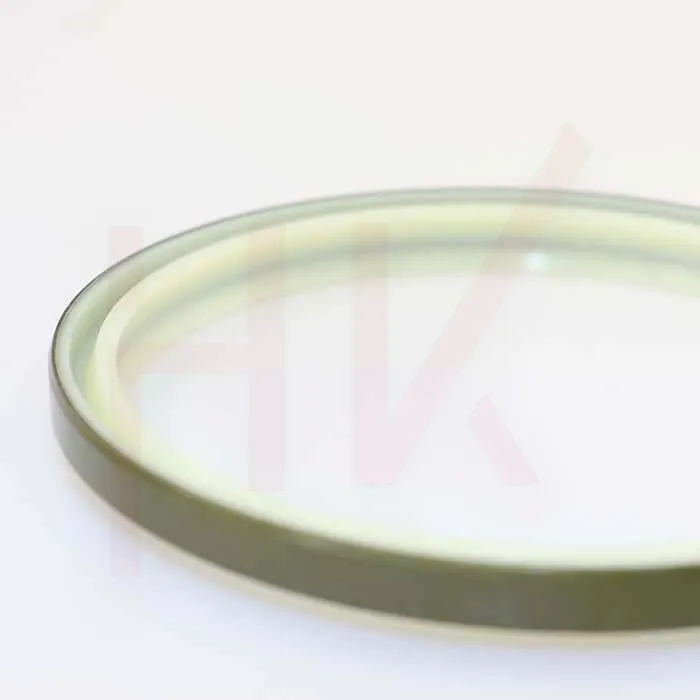
Precision machining tools come into play in the repair process, where surface finishing might be required to restore the components to their ideal condition. Choosing the correct seal material is another critical factor, heavily dependent on operational conditions such as temperature, pressure, and fluid type. Over the years, fluorocarbon elastomers and nitrile butadiene rubber have proven their efficacy in demanding hydraulic applications due to their resilience and compatibility with a variety of hydraulic fluids.
hydraulic seal repair
The expertise component of seal repair also involves designing a maintenance schedule that aligns with the operational cycle of the machinery. Routine checks and proactive replacements, rather than reactive fixing, are key strategies employed by industry experts to prevent unscheduled downtimes. This not only saves cost but extends the lifespan of the machinery.
Authoritativeness in hydraulic seal repair entails a profound commitment to quality assurance practices. Utilizing seals from reputable manufacturers and adhering to industry standards such as ASME and ISO ensures the repairs will stand the test of time. Professionals also utilize advanced diagnostic tools, including thermal imaging and ultrasonic leak detectors, to verify the integrity of hydraulic systems post-repair.
Lastly, trustworthiness is built through transparency and customer education. Providing clients with comprehensive reports detailing the repair process, as well as guidance on operational best practices, empowers them to make informed decisions about their equipment. For many businesses, machinery is an investment that must yield returns, and trustworthy service providers become partners in ensuring this objective is met.
In summation, hydraulic seal repair is not a simplistic task of component replacement; it is a multidisciplinary endeavor requiring experience, precision, and a holistic view of the hydraulic system. Through commitment to quality, continuous learning, and innovation, experts in the field assure the operational longevity and reliability of hydraulic systems, cementing their roles as essential partners in industrial success.