In the realm of industrial machinery, the hydraulic cylinder stands as a crucial component, powering a myriad of operations. However, the true secret behind the seamless functionality of these hydraulic giants lies in the integrity of their seals. Hydraulic cylinder repair seals are not merely replaceable parts; they are the guardians of hydraulic efficiency and longevity.

The intricate design of hydraulic cylinders requires seals that can withstand extreme pressures and temperatures while preventing fluid leakage that could lead to costly downtimes. The experience of working with hydraulic systems highlights that not all seals are created equal. Selecting the right repair seal is imperative, not only for restoring functionality but also for enhancing the overall performance of hydraulic systems.
From experience, encountering a failed hydraulic system often reveals that it’s the seals that succumb first. The harsh environments in which these cylinders operate—ranging from construction sites to manufacturing plants—subject the seals to wear and abrasion. When hydraulic seals deteriorate, they can’t effectively prevent contaminants from entering the system, which can lead to hydraulic fluid degradation and eventual component damage.
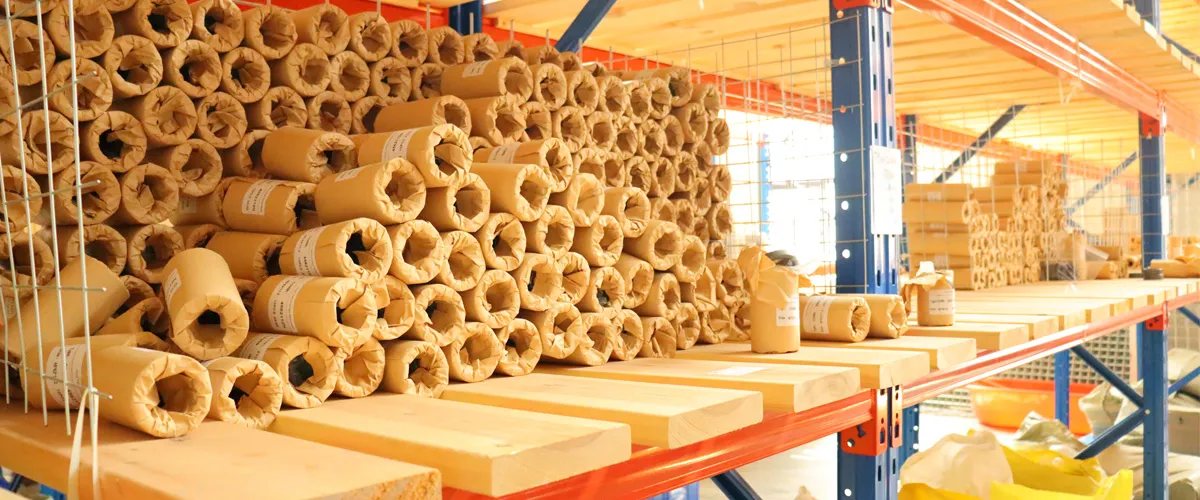
Expertise in hydraulic systems underscores the importance of selecting repair seals made from premium materials. For instance, seals made from highly resilient polyurethane or advanced elastomers provide better resistance to wear, abrasion, and chemical exposure. Their compatibility with a wide array of hydraulic fluids ensures that the seals remain pliable and effective over the lifespan of the cylinder.
hydraulic cylinder repair seals
The choice of correct seal design is equally paramount. Options such as rod seals, piston seals, and wipers are available, each serving unique roles within the cylinder. For hydraulic cylinder repair, utilizing seals that match the design and specifications of the original equipment manufacturer can restore the cylinder to its optimal state. Moreover, consulting manufacturer guidelines or working with a seal expert contributes significantly to the success of the repair process.
Authoritativeness in the field of hydraulic cylinder repair is demonstrated by adherence to industry best practices and standards. Professional maintenance routines that include regular inspection and timely replacement of seals prevent unexpected breakdowns. Industries employing hydraulic systems should adopt a preventive maintenance mindset to optimize performance and extend the lifecycle of their machinery.
Trustworthiness is built through empirical results. Successful hydraulic repairs are confirmed by the efficiency and sustainability of the cylinder function post-repair. It is vital to source seals from reputable suppliers who guarantee the quality and durability of their products. Customer testimonials and case studies that detail successfully resolved hydraulic challenges lend credence to the effectiveness of the chosen seals and repair methodologies.
For those seeking unrivaled performance in their hydraulic systems, understanding the critical role of repair seals is indispensable. Investing in high-quality seals and employing expert repair techniques not only rejuvenates the hydraulic cylinder but also amplifies the reliability of the entire operation. By upholding the tenets of experience, expertise, authoritativeness, and trustworthiness in the selection and application of hydraulic cylinder repair seals, companies can ensure their machinery remains at the forefront of operational excellence.