When it comes to hydraulic systems, seals play a pivotal role in ensuring efficiency and longevity. Hydraulic oil seal types are varied, each serving a specific purpose and providing unique benefits. Understanding the intricacies of these seals is crucial for anyone looking to maintain or improve their hydraulic system’s performance.
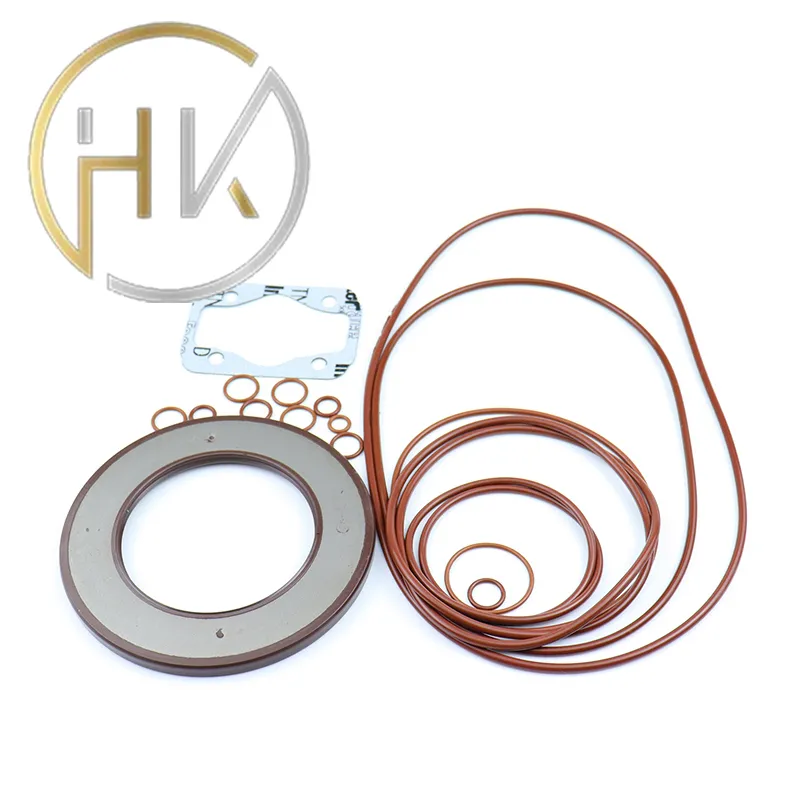
Oil Seal Basics in Hydraulic Systems
Hydraulic systems operate under pressure, often in harsh environments susceptible to contamination. The primary role of any oil seal in these systems is to prevent fluid leakage and protect the machinery from dust, dirt, and other contaminants. This helps in maintaining pressure, ensuring smooth operation, and consequently, extending the life of the equipment.
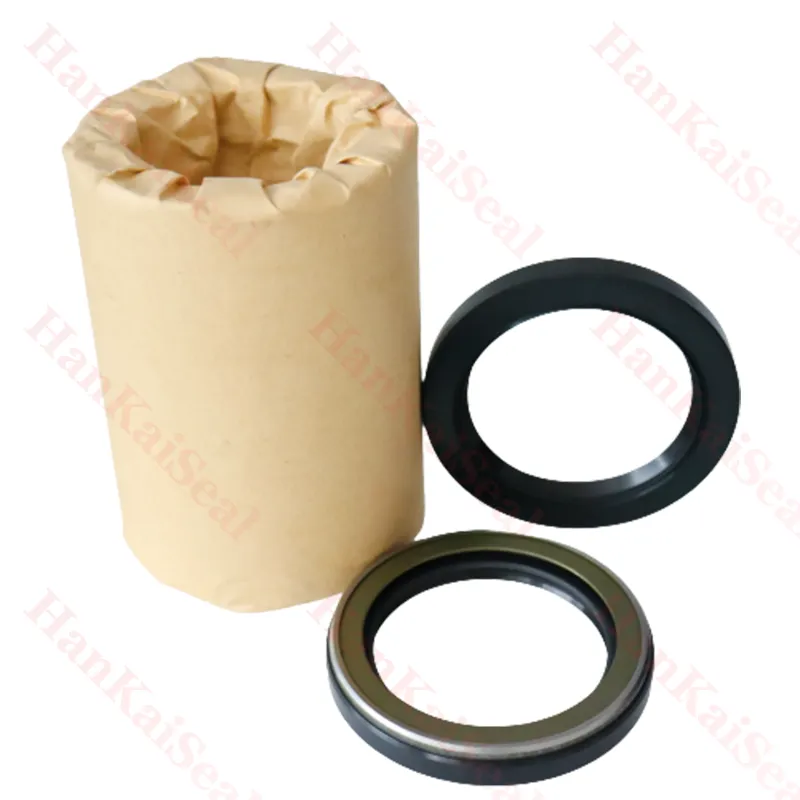
Types of Hydraulic Oil Seals
1. Piston Seals
Piston seals are used to seal between the piston and the cylinder bore, ensuring that pressurized hydraulic fluid does not leak across the piston, enhancing operational efficiency. These seals come in single-acting or double-acting variants, tailored to specific applications. High-quality piston seals improve machine performance by minimizing friction and wear while providing high sealing efficiency.
2. Rod Seals
Rod seals are critical for preventing hydraulic fluid leakage from the cylinder and avoiding the ingress of contaminants. Positioned around the cylinder rod, they are the primary barrier against external factors. These seals must withstand high pressure and temperatures while reducing friction, within the cylinder housing.
3. Wiper Seals
Wiper seals, also known as scraper seals, protect against dirt and moisture by wiping the rod clean as the hydraulic system operates. This helps in reducing the contamination of hydraulic fluid and extends the life of both the seals and the cylinder's components.
4. Rotary Seals
Rotary seals are utilized in hydraulic systems where components rotate relative to each other, managing the seal of a rotating shaft. These seals are designed to balance the requirements of sealing efficiency, heat dissipation, and low friction, enhancing the reliability of rotating machinery parts.
Choosing the Right Hydraulic Oil Seal
hydraulic oil seal types
Selecting the appropriate hydraulic oil seal involves considerations like the operating pressure, temperature range, fluid type, and the specific application environment. Each type of seal has its optimal conditions; therefore, precision in selection affects overall performance and system reliability.
Material Considerations
Material plays a crucial role in the performance of hydraulic oil seals. Common materials include Nitrile Rubber (NBR), Fluorocarbon (FKM), and Polyurethane (PU). Each material offers specific benefits
- Nitrile Rubber (NBR) Excellent for general hydraulic applications, providing good abrasion resistance and compatibility with most hydraulic fluids.
- Fluorocarbon (FKM) Ideal for high-temperature and chemically aggressive environments, offering superior heat resistance.
- Polyurethane (PU) Known for its resilience and high tear resistance, suitable for high-pressure applications.
Ensuring Seal Efficiency
Regular maintenance and inspection of hydraulic systems ensure oil seals function effectively. Monitoring for wear, tear, or damage, and replacing seals as necessary, prevent costly downtimes. Moreover, using seals from reputable manufacturers guarantees quality and reliability, contributing to their trustworthiness.
Conclusion
An expert understanding of hydraulic oil seal types empowers decision-makers to optimize system performance and longevity. With precise selection, careful material consideration, and regular maintenance, these components secure their crucial role in the successful operation of hydraulic systems. Trust in product quality and installation precision remains imperative for achieving long-term benefits from hydraulic seals.