The TCN oil seal has established itself as a formidable component in industrial and automotive applications due to its unique blend of high-performance features. It plays a crucial role in maintaining machinery efficiency and longevity by preventing fluid leakage and ingress of contaminants.
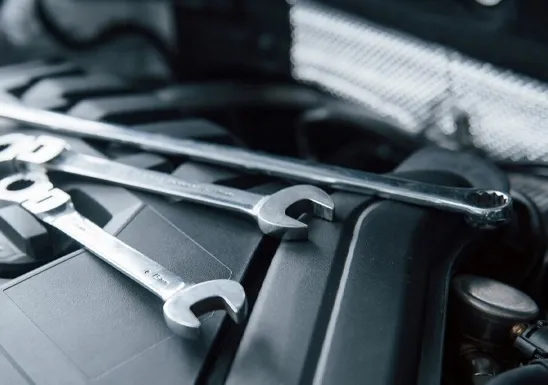
With experience spanning decades in the seal manufacturing industry, the TCN oil seal stands out for its adaptability to various operational environments. Engineered with precision, it is designed to withstand extreme pressures and temperatures, demonstrating impressive durability. This seal is essential for industries such as automotive, aerospace, marine, and heavy machinery, where performance reliability is non-negotiable.
Expertise in the field reveals that the TCN oil seal's material composition is a significant factor in its superior performance. Typically, these seals are manufactured using high-grade elastomers such as nitrile rubber (NBR), fluorocarbon (FKM), or silicone, each selected based on its ability to resist wear and corrosion and its chemical compatibility with the substances being sealed.
The choice of material directly influences the seal’s effectiveness and lifespan in specific applications.
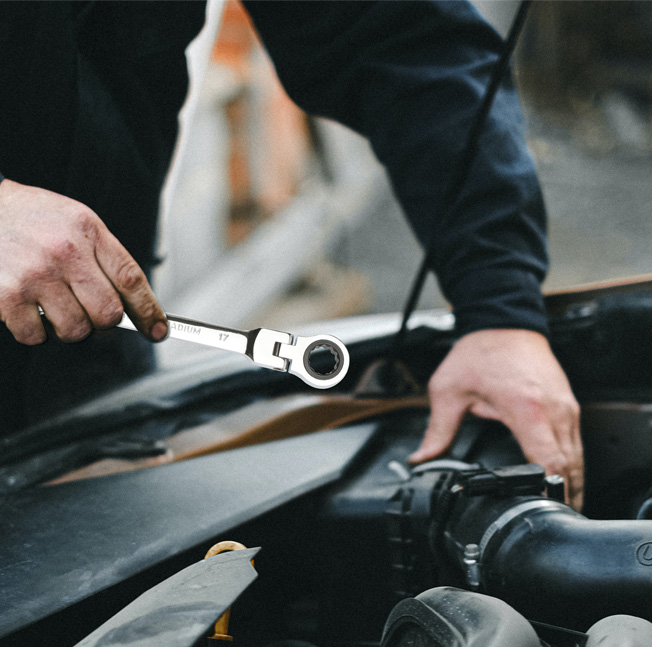
One of the most authoritative aspects of the TCN oil seal is its design, which incorporates a lip feature reinforced by a metal or polymer spring. This feature ensures a tighter seal against the rotating shaft, thereby reducing the chances of leaks under dynamic conditions. Furthermore, the double-lip design provides an additional barrier that protects against environmental contaminants such as dust and water, a key consideration for machinery that operates outdoors or in challenging environments.
oil seal tcn
Trustworthiness in product choice is cemented by feedback from field applications, where the TCN oil seal consistently receives high marks for reducing maintenance needs and machine downtime. Companies that have incorporated this seal into their operational processes report cost savings and increased productivity, affirming the product’s value proposition. Moreover, the seal's compliance with international quality standards such as ISO and ASME enhances its credibility and assures end-users of its reliability and safety.
Real-world case studies exemplify the efficacy of the TCN oil seal. For instance, an industrial plant specializing in automotive assembly reported a 20% reduction in operational interruptions after switching to these seals. Similarly, in the off-highway vehicle sector, incorporating TCN oil seals into the design of their hydraulic systems resulted in significantly fewer hydraulic fluid leaks, underscoring the seal’s capability to handle high-pressure environments.
Enhancing the longevity and performance of equipment, the TCN oil seal offers superior resistance to thermal expansion and contraction. In particular, seals made from fluoroelastomers can operate in temperature ranges extending from -20°C to 200°C, making them suitable for high-temperature applications such as engine systems and heavy equipment engine compartments.
In conclusion, the TCN oil seal remains a testament to what expertly crafted sealing solutions can achieve. Its strategic incorporation into industrial processes and machinery ensures optimal performance and protection, aligning with key business priorities of efficiency, reliability, and cost management. As industries evolve and demands on machinery intensify, the role of the TCN oil seal in safeguarding operational integrity and contributing to sustainable industrial practices will undoubtedly remain pivotal.