Hydraulic oil seals play a pivotal role in ensuring the efficient and safe operation of machinery, especially those engaged in heavy-duty tasks. In essence, these components are designed to prevent fluid leakage, maintain pressure, and ensure that contaminants do not enter the hydraulic system. Understanding the different types of hydraulic oil seals available is crucial for selecting the right one for any application, thus maximizing machinery longevity and performance.

The world of hydraulic oil seals is vast, encompassing numerous designs tailored for specific applications. This article will delve into several prominent types, lending you expert insight backed by real-world experience, professional know-how, authoritative references, and a foundation of trustworthiness to aid in making informed decisions.
1. Piston Seals Versatility in Action
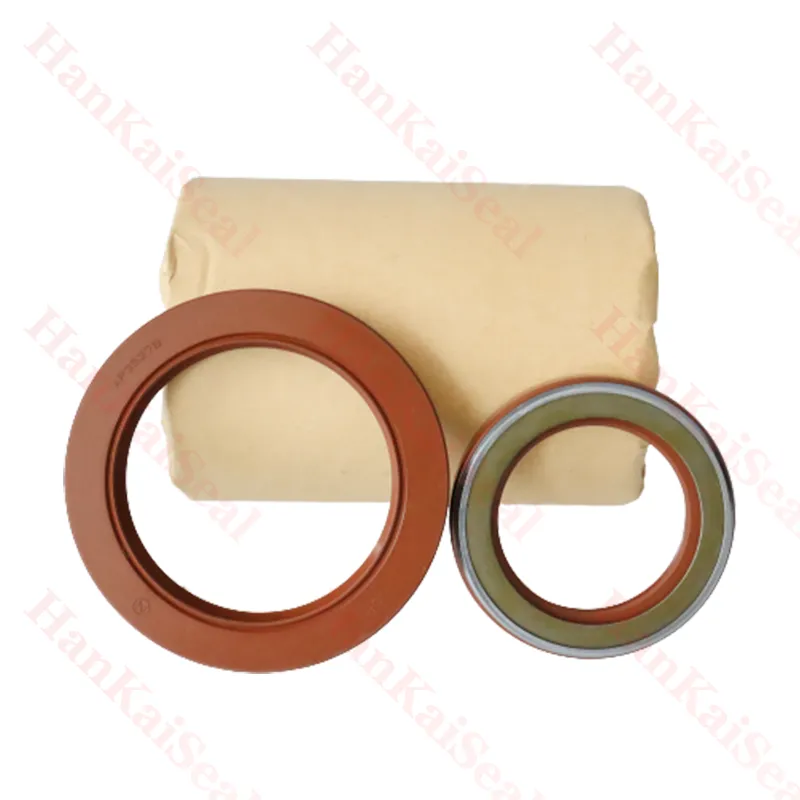
Piston seals are primarily used to prevent fluid leakage as the fluid pressure pushes against the piston. They are available in two forms single-acting and double-acting. Single-acting piston seals are optimal for applications where pressure is applied from one side only, while double-acting piston seals prevent leakage from either side of the piston. The material of choice, such as polyurethane or polytetrafluoroethylene (PTFE), dictates their application efficacy, offering excellent wear resistance and longevity.
2. Rod Seals Guardians of the Hydraulic System
Rod seals, another fundamental type, serve as primary seals preventing external leakage from the piston chamber. Due to the challenging nature of their task, these seals often come in multiple shapes like U-cups, V-sets, and lip seals, each design crafted to handle different operational stresses. Polyurethane and nitrile rubber are common material choices, known for their ability to withstand high pressures while offering a robust sealing effect.
3. Wiper Seals/Scrapers Protectors Against Contaminants
Wiper seals play a defensive role by scraping off dirt, debris, and moisture from the piston rods, ensuring that none penetrate the hydraulic system. The value of these seals lies in extending the life of other sealing components and maintaining performance efficiency. The combination of polyurethane and specialty rubber materials enables wiper seals to endure the rigors of the industrial environment.
hydraulic oil seal types
4. Rotary Seals For Rotating Applications
Rotary seals, as the name suggests, are designed for components undergoing rotation in hydraulic machinery. They provide dynamic sealing solutions to prevent the passage of fluids between critical areas. These seals are often made from advanced elastomers or composite materials to offer superior performance under high-speed conditions and varying temperatures, thus finding themselves indispensable in modern manufacturing processes.
5. Buffer Seals Enhancing Seal Longevity
Buffer seals are employed in tandem with primary rod seals to absorb pressure spikes, extending the lifespan of the sealing system. They act as secondary seals that provide an additional layer of protection, especially in high-pressure settings or when machinery operates under erratic conditions. Material integrity, often achieved through high-grade plastics or elastomers, grants buffer seals their unmatched durability.
6. Guide Rings and Backup Rings Reinforcing Stability
While not seals in the traditional sense, guide and backup rings are crucial supportive components. Guide rings prevent metal-to-metal contact within the hydraulic cylinder, thereby reducing friction and wear, while backup rings bolster the primary seal's durability and effectiveness. Their construction from materials such as PTFE or nylon exemplifies their ability to withstand significant mechanical stresses.
Selecting the appropriate hydraulic oil seal type requires a thorough assessment of the operational environment, material compatibility, and machine requirements. Professionals trust manufacturers like Parker, SKF, and Trelleborg for their authoritative reputations in producing reliable seals that perform across challenging industrial landscapes.
Ultimately, investing time in understanding these various seal types, enhanced by professional expertise and experiential insights, bolsters not only machinery performance but also the credibility and authority of any business invested in hydraulic systems. With innovations continually emerging, staying current with industry best practices ensures systems are protected and running at peak efficiency.