Replacing seals on a hydraulic motor is a routine yet essential maintenance task that demands professional expertise and meticulous attention to detail. Hydraulic motors, being crucial components of many industrial machines, depend heavily on intact seals for optimal functionality. Compromised seals can lead to leaks, reduced efficiency, and ultimately, costly downtime. Here is a comprehensive guide focusing on the expertise, experience, and trustworthiness required in replacing hydraulic motor seals.
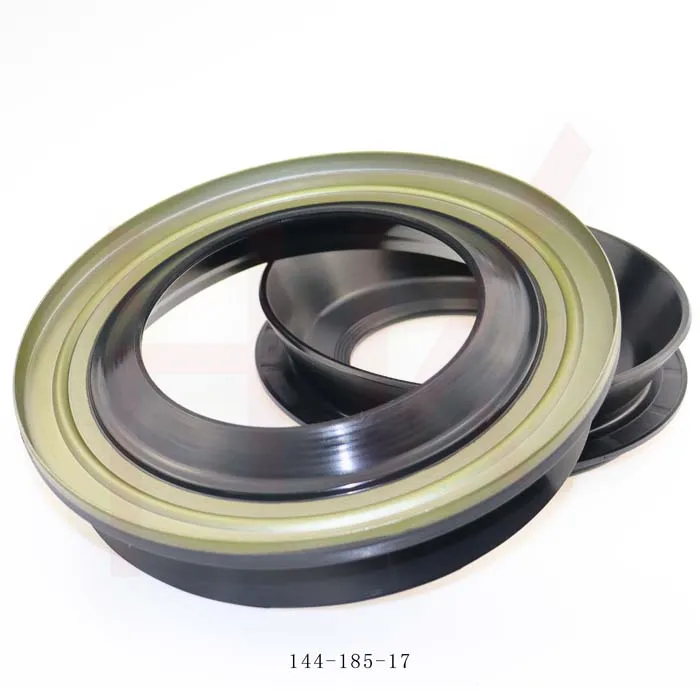
Understanding Hydraulic Motor Functionality
To appreciate the necessity of replacing seals, one must first understand how a hydraulic motor operates. These motors convert hydraulic energy into mechanical energy, facilitating movement and force in various machinery. The seals within these motors are crucial in maintaining the internal pressure and preventing external contaminants. With time, seals experience wear and tear, leading to decreased performance and potential failure.

Signs of Seal Wear and Need for Replacement
Professional expertise is showcased when identifying early signs of seal wear. Common indicators include visible oil leaks around the motor, a noticeable decrease in hydraulic pressure, unusual noises during operation, and a decline in overall performance efficiency. Recognizing these symptoms early can prevent significant damage and reduce downtime.
The Replacement Process Expertise in Action
Replacing seals requires a high degree of precision and technical know-how. The process begins with a thorough understanding of the motor's schematics, enabling the engineer to carefully disassemble the motor without causing cross-contamination of system components.
1. Preparation and Safety Measures Proper preparation is critical. This involves clearing the area of any unnecessary tools and equipment, ensuring the work environment is clean, and gathering all required tools for the replacement procedure. Safety protocols must be strictly adhered to, such as depressurizing the hydraulic system to prevent hazardous fluid discharge.
hydraulic motor seal replacement
2. Disassembly of the Motor Carefully detaching the motor from its assembly is crucial. Expertise in this area ensures each component is handled delicately to prevent damage. Marking each component's position helps maintain accuracy during reassembly.
3. Seal Removal and Inspection Once accessible, the old seals are removed using specific tools designed to avoid damage to the motor surfaces. Each seal is inspected to analyze wear patterns, which provides insights into potential underlying issues such as misalignment or incorrect pressure settings.
4. Selecting the Right Replacement Seals Not all seals are created equal. Expert knowledge in selecting high-quality seals, considering factors such as material compatibility and environmental conditions, is imperative.
Opting for seals from reputable manufacturers enhances reliability and longevity.
5. Installation of New Seals This step requires utmost precision. The seals are installed using the recommended methods for the specific motor model, ensuring they fit securely without any undercuts or distortions. Proper lubrication during this process prevents friction-related wear.
6. Reassembly and Testing Expert reassembly ensures every part is returned to its rightful place with the correct torque specifications. Before full operational deployment, rigorous testing under controlled conditions verifies the integrity of the seals and overall motor efficiency.
Trustworthy Results through Professional Maintenance
A successful seal replacement is validated through improved motor performance and operational reliability. Scheduled maintenance by professionals ensures seals are always in optimal condition, promoting prolonged motor lifespan and reduced risk of catastrophic failures. Establishing a maintenance logbook is recommended for keeping track of service dates, component lifespans, and any occurrences of system anomalies.
In conclusion, replacing hydraulic motor seals is an intricate task best managed by skilled professionals. Through comprehensive understanding and application of technical expertise, the process not only improves machinery performance but also builds trust and reliability between service providers and clients. Investing in high-quality seals and routine maintenance leads to a significant return on investment, safeguarding machinery against unexpected breakdowns, and ensuring consistent productivity in industrial operations.