High pressure shafts are indispensable components in various industrial and mechanical applications, playing a critical role by ensuring efficient transmission of power and motion. Their importance cannot be overstated in fields ranging from aerospace to automotive engineering. This article delves into the intricacies of high-pressure shafts, shedding light on their construction, applications, and maintenance, thus equipping professionals and enthusiasts with a comprehensive understanding vital for making informed decisions.
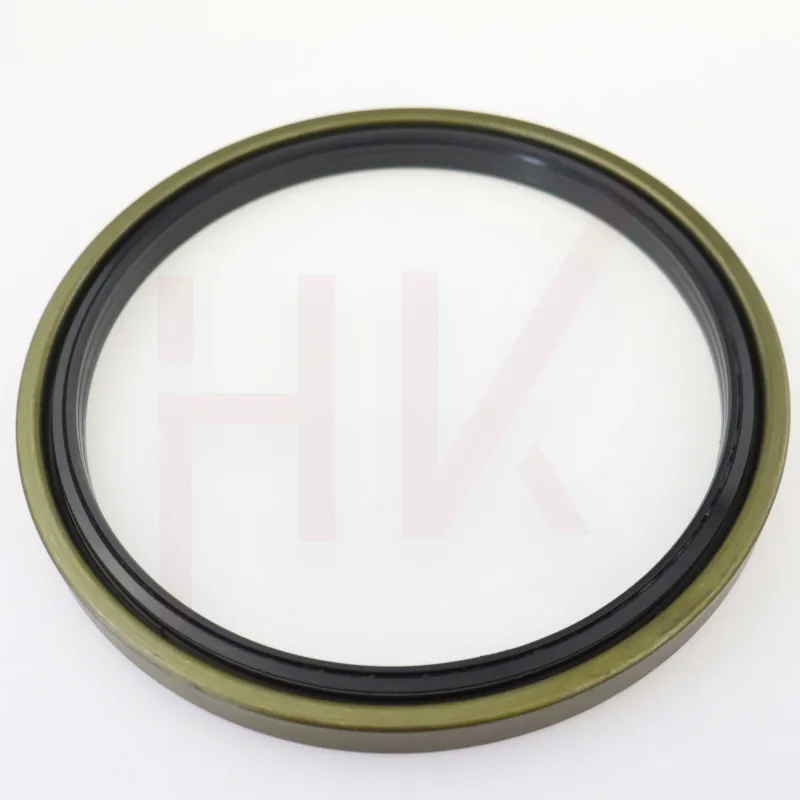
At the heart of many mechanical systems, high-pressure shafts are revered for their ability to withstand substantial stress and provide reliable performance. These shafts are engineered to handle significant rotational forces while maintaining structural integrity, a necessity for high-performance machinery. The robust nature of high-pressure shafts stems from meticulous material selection and advanced engineering techniques, designed to optimize performance under demanding conditions.
One of the foremost considerations in the design of high-pressure shafts is the choice of material. Common materials include alloy steels, titanium, and composites, each selected for their specific strength, weight, and resistance to environmental factors. Alloy steels, for instance, are frequently used due to their excellent fatigue strength and machinability, making them ideal for custom configurations. Titanium offers a high strength-to-weight ratio, essential in aerospace applications where weight savings are critical without compromising durability. Composites provide a lightweight alternative with customizable stiffness and strength properties, beneficial in specialized applications that demand precision.
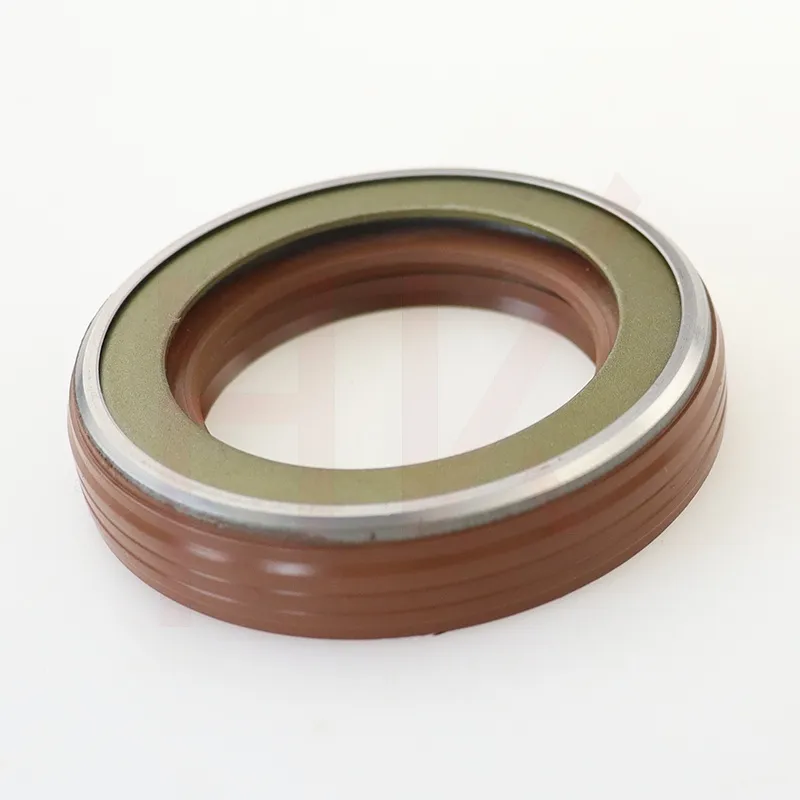
Precision engineering is paramount in the manufacturing of high-pressure shafts. Advanced techniques such as computer-aided design (CAD) and finite element analysis (FEA) are employed to simulate stress distribution and optimize geometry, ensuring that the shafts can endure the operational stresses encountered in high-pressure environments. The manufacturing process also involves precision machining and heat treatment, both crucial in enhancing the mechanical properties and lifespan of the shafts.
High-pressure shafts find applications across a broad spectrum of industries. In the aerospace sector, they are integral to jet engines, transferring power from the turbines to the compressors. The automotive industry utilizes them in high-performance vehicles, where they serve as drive shafts transmitting torque between components. Even in power generation, high-pressure shafts play a pivotal role in turbines, aiding in the efficient conversion of mechanical energy.
high pressure shaft
A critical aspect of working with high-pressure shafts is establishing a reliable maintenance routine. Regular inspections are crucial for identifying wear and tear, which can manifest as vibrations, noise, or reductions in performance. Non-destructive testing methods, such as ultrasonic and magnetic particle testing, are routinely employed to detect subsurface flaws that could lead to catastrophic failures if left unaddressed. Lubrication is another fundamental maintenance consideration, as it minimizes friction and wear, extending the operational life of the shafts.
Moreover, balancing and alignment are key maintenance practices that sustain high-pressure shaft performance. Imbalances can lead to vibrations that cause premature wear and damage the shaft and associated components. Alignment ensures that the shaft remains properly oriented with the system it powers, safeguarding against misalignment-related stresses.
The strategic importance of high-pressure shafts necessitates a commitment to quality and reliability, underscoring the need for collaboration with reputable manufacturers and suppliers. Trust is built through transparency in the manufacturing process, adherence to stringent industry standards, and the provision of comprehensive documentation outlining material specifications, performance metrics, and quality assurance protocols.
In conclusion, high-pressure shafts are critical components engineered to excel under duress, demanding precise material selection and cutting-edge manufacturing processes. Their application across industries highlights their versatility and significance in enhancing mechanical systems' efficiency and reliability. Proper understanding, coupled with diligent maintenance, ensures these shafts continue to perform at their peak, safeguarding the operational integrity of the machinery they empower. As technology progresses, the evolution of high-pressure shaft design will continue to align with innovations, promising advancements in performance and application diversity.