High-pressure oil seals play a critical role in industrial machinery, offering an essential barrier that ensures lubricants remain in place while preventing contaminants from infiltrating the systems. This delicate balance facilitates efficient machinery operation, extending the lifespan of components and optimizing overall performance. Understanding the intricacies of high-pressure oil seals not only requires technical knowledge but also a wealth of experience, as these components operate under demanding conditions that challenge their design and material properties.

With years of expertise in mechanical engineering and industrial applications, it's clear that selecting the right oil seal hinges on specific parameters, such as pressure levels, temperature fluctuations, and the type of lubricant involved. High-pressure environments, often found in hydraulic systems and heavy machinery, necessitate seals capable of withstanding immense force without succumbing to leaks or fatigue.
Material selection is paramount in ensuring an oil seal's success under high pressure. Elastomers like fluorocarbon (Viton) and nitrile rubber often find common use due to their superior resilience to heat and chemical degradation. In applications exposed to extreme temperatures or aggressive chemicals, polytetrafluoroethylene (PTFE) seals are preferred for their unparalleled resistance and durability. These materials furnish the necessary balance between rigidity and flexibility, crucial for maintaining a tight seal in dynamic environments.
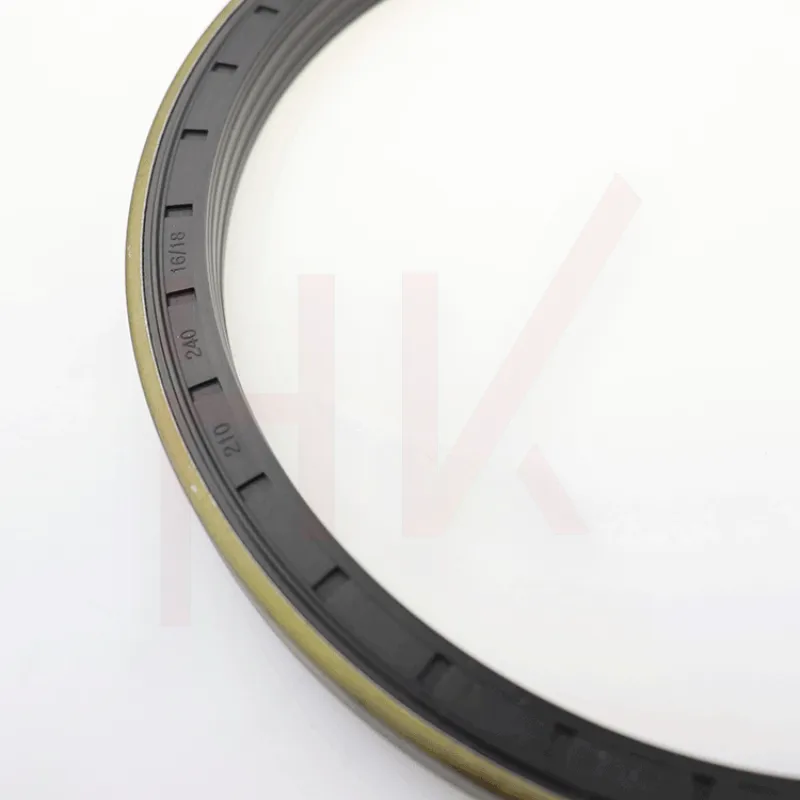
Precision engineering also dictates high-pressure seal design, which must accommodate axial play and minor misalignments. The incorporation of spiral wound springs or garter springs enhances the seal's ability to adapt to varying pressures and speeds, thereby ensuring a consistent and reliable barrier. Additionally, multi-lip configurations offer redundancy, mitigating the risk of seal failure and reinforcing their reliability in high-pressure applications.
high pressure oil seals
Installation expertise cannot be overstated. Even the most robust oil seal is rendered ineffective if not installed correctly. It's imperative that surfaces are meticulously cleaned and inspected for irregularities that could compromise the seal's integrity. Lubrication during installation aids in preventing damage to the seal's lip, ensuring a smooth interface with the shaft and housing. Once installed, regular monitoring and maintenance are vital, as they allow for the early detection of wear or potential failure.
Moreover, the authoritativeness and trustworthiness of an oil seal provider are essential considerations. Established manufacturers offer a track record of quality and innovation, backed by rigorous testing and compliance with international standards. Engaging with a reputable supplier often provides access to technical support and detailed documentation, aiding in the appropriate selection for your specific needs.
High-pressure oil seals are indispensable in maintaining the efficacy of countless industrial systems. Their correct application not only demands an understanding of the technical specifications but also a holistic view of the system in which they operate. By leveraging both expertise and experience, industries can ensure their machinery remains operational, minimizing downtime and maximizing efficiency.
In conclusion, high-pressure oil seals embody the intersection of engineering proficiency and practical application. The choice of material, design, installation practices, and supplier all contribute to the seal's overall effectiveness, ultimately safeguarding machinery against the relentless forces of pressure and contamination. Whether you're a facility manager or an engineer, appreciating the nuances of oil seal performance is crucial in fostering a productive and sustainable operation.