High pressure hydraulic shaft seals play an indispensable role in a broad spectrum of industrial applications. They are designed to prevent leakage, contamination, and maintain the necessary pressure levels within hydraulic systems. These seals ensure operational efficiency, safety, and longevity of machinery, proving essential in industries like automotive, aerospace, and manufacturing.
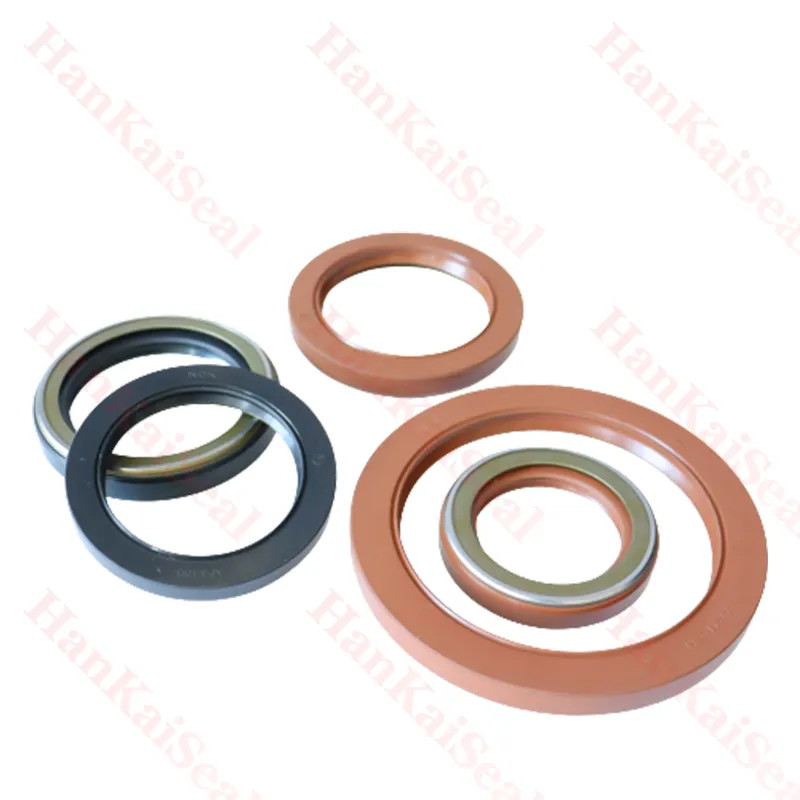
When selecting the right seal, several critical factors must be considered to ensure optimal performance and durability. The foremost consideration should be the pressure range anticipated within the system. High pressure environments demand seals that can withstand substantial stress without deforming or sustaining damage. Materials such as urethane, PTFE composites, and advanced rubber compounds are frequently used due to their resilience and ability to maintain integrity under pressure.
Another essential factor is the dynamic nature of the shaft’s movement. Axial and radial loads must be factored in, as these affect the seal's performance. High-speed operations can generate significant friction, necessitating seals with low friction coefficients to reduce wear and prolong lifespan. While traditional lip seals provide basic sealing functions, advances such as labyrinth or multi-lip seals offer enhanced protection by minimizing leakage paths and providing a pressured barrier against contaminants.
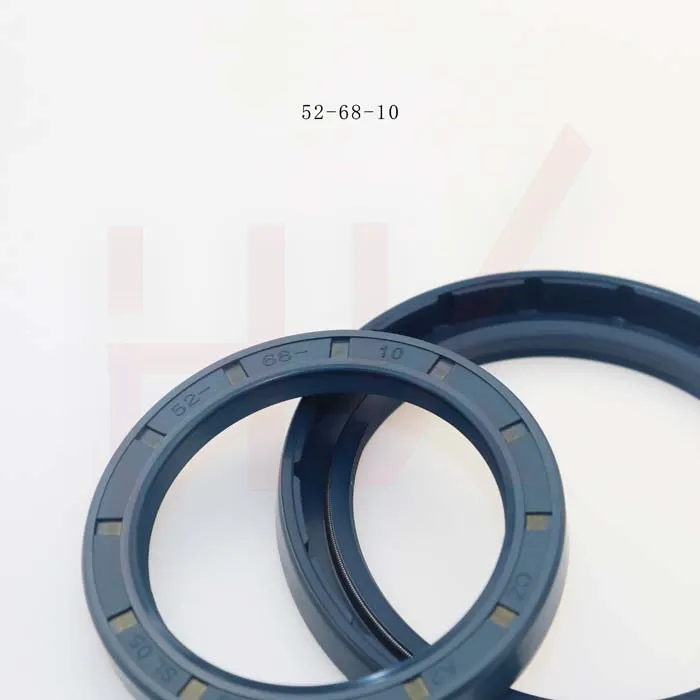
The environmental conditions also play a decisive role in seal selection. High temperatures, corrosive agents, and particulate matter can impose additional strain on seals. Hence, materials with high temperature tolerance or chemical resistance should be prioritized in such environments. High-grade PTFE and viton are examples that mitigate these issues effectively.
Installation nuances also cannot be overlooked. Incorrect installation is a leading cause of seal failure. Therefore, adherence to precise installation protocols, possibly even employing specialized tools or consultation with experts, is recommended. A robust seal will only perform as expected if installed and maintained correctly.
high pressure hydraulic shaft seals
One underappreciated aspect is maintenance, where regular inspections and timely replacements can stave off potential failures. Advanced monitoring systems can now predict seal life expectancy based on operational data, preventing unexpected downtimes.
Innovations in high pressure hydraulic shaft seals have led to the development of seals capable of interactive communication, employing sensor technology to monitor real-time conditions. This innovation underscores the importance of integrating technology with traditional industrial components to drive efficiency.
Furthermore, sourcing these seals from reputable manufacturers cannot be overemphasized. Accredited suppliers often invest significantly in research and development, ensuring their products meet stringent industry standards. Certification to standards like ISO 6194 for rotary shaft seals provides assurance of quality and adherence to specifications.
In the global context, as industries pivot towards more sustainable operations, the focus on resource efficiency is sharper than ever. High efficiency seals contribute to reducing energy wastage by enhancing the sealing efficiency which, in turn, reduces system losses, positively impacting the environmental footprint.
In conclusion, high pressure hydraulic shaft seals are more than mere components they are pivotal to the operational success and efficiency of hydraulic systems. With an increasing focus on performance and sustainability, choosing the right seal—bearing in mind material selection, operational conditions, and maintenance considerations—can mean the difference between operational excellence and costly downtimes. As industries evolve, so too must the technology and strategy behind selecting and maintaining these critical components, underscoring their undeniable importance in today's industrial environment.