In industries where equipment reliability and safety are paramount, high pressure seals play a crucial role. Their importance cannot be overstated, as they are essential in preventing leaks and maintaining system integrity across various applications. These seals are designed to withstand extreme pressure situations, ensuring that machinery operates efficiently without the risk of catastrophic failure. Drawing from years of industry experience and technical expertise, we delve into what makes high pressure seals indispensable in numerous sectors.
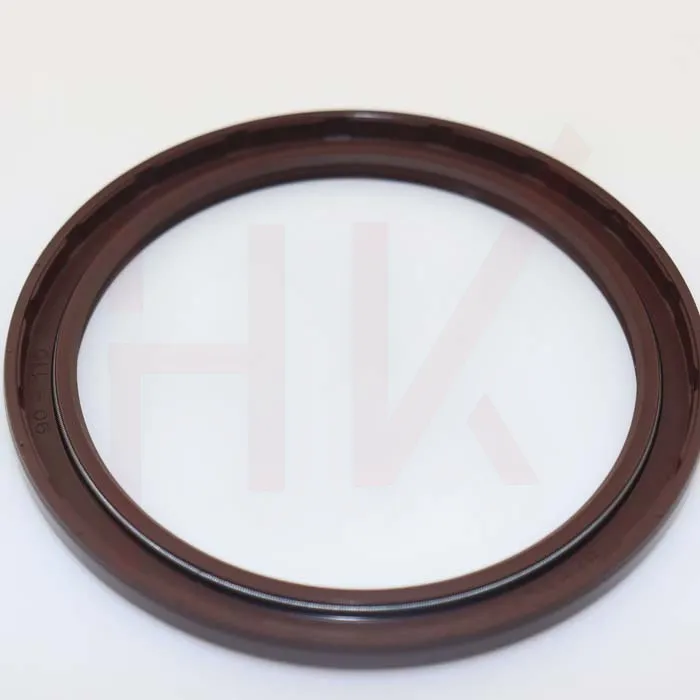
High pressure seals are typically used in environments where fluids or gases are confined under substantial pressure. This includes applications in oil and gas exploration, chemical processing, power generation, and aerospace engineering. Each of these industries demands seals that can not only endure high pressure but also resist extreme temperatures, corrosion, and wear. The ability to deliver on these fronts is what establishes a seal's reputation for reliability and durability.
What distinguishes high pressure seals from regular seals is their design intricacies and the materials from which they are made. Manufacturers employ cutting-edge materials like PTFE, graphite, and advanced elastomers to enhance seal performance. These materials are chosen for their resilience and ability to maintain structural integrity under challenging conditions. The choice of material is often determined by the specific needs of the application, considering factors such as chemical compatibility, temperature range, and pressure levels.
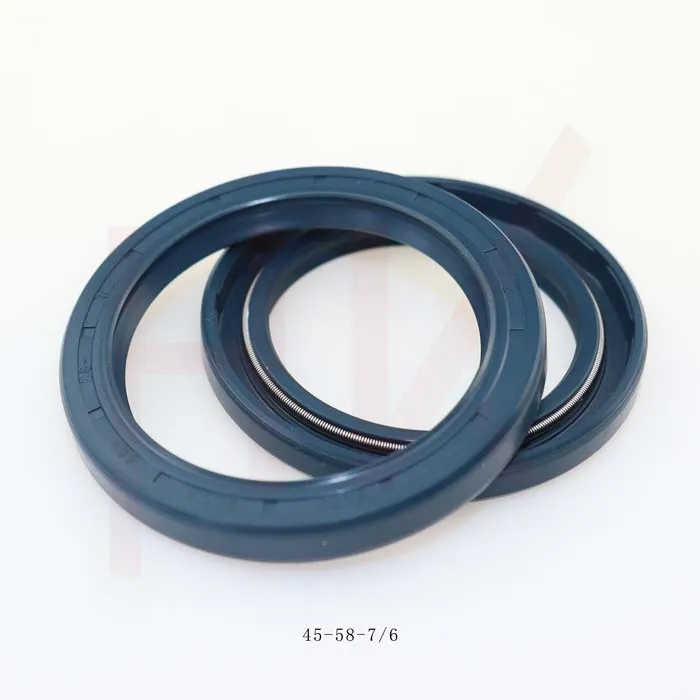
Expertise in seal design is equally important. Engineers employ advanced simulation tools to model seal performance under various operational scenarios. By leveraging Finite Element Analysis (FEA), they can predict how seals will behave under stress, thus optimizing the design before physical prototypes are made. This not only saves costs but also accelerates the development process, ensuring that high pressure seals meet the stringent demands of modern industries.
Authoritativeness in the market is achieved through a proven track record of delivering seals that perform exceptionally well in high-pressure applications. Leading manufacturers often provide technical support and consultation, underscoring their commitment to quality and customer satisfaction. Certifications from recognized bodies further bolster the credibility of these products, assuring users of their adherence to international standards.
high pressure seal
Trustworthiness in high pressure seals is built on years of successful deployments in the field. Case studies showcasing real-world applications serve as testimonials to their effectiveness. For instance, seals used in offshore drilling are exposed to one of the harshest environments possible, withstanding pressures that can exceed thousands of PSI while resisting corrosive seawater and abrasive sediment.
High pressure seals that thrive in such conditions become an invaluable asset to any operation.
Moreover, the evolution of high pressure sealing technology has led to innovations such as non-contacting seals, which reduce friction and heat generation, thereby extending the lifespan of both the seal and the equipment it protects. These advancements contribute not only to increased reliability but also to significant cost savings over time, as equipment downtime is minimized.
Sustainability has also become an integral aspect of high pressure seal development. Manufacturers are increasingly focusing on producing seals that not only offer superior performance but are also environmentally friendly. Utilizing recyclable materials and eco-friendly production processes not only meets regulatory requirements but also caters to the growing demand for sustainable industrial solutions.
In conclusion, a high pressure seal's role in maintaining operational efficiency and safety is unequivocal. With a blend of state-of-the-art materials, innovative design techniques, authoritative market presence, and a commitment to trustworthiness, these seals provide vital solutions across multiple high-stakes industries. Choosing the right high pressure seal necessitates a keen understanding of the application at hand and a reliance on reputable manufacturers who offer proven performance backed by technical expertise and support. As industries continue to push the boundaries of what's possible, the evolution and continuous improvement of high pressure sealing technology remain pivotal to sustaining and enhancing operational success.