In the realm of industrial applications where machinery operates under high-pressure conditions, the significance of a robust oil seal cannot be overstated.
An oil seal designed for high pressure not only extends the operational life of mechanical components but also ensures safety and efficiency. Engineers and maintenance professionals are continuously seeking reliable oil seals that can withstand the demands of high-pressure environments. This article delves into the intricacies of high-pressure oil seals, offering insights from experienced professionals and highlighting the importance of expertise in selecting the right product.

High-pressure oil seals are specifically engineered to prevent the leakage of lubricants and other fluids while keeping foreign particles out of critical machinery components. These seals are indispensable in applications involving hydraulic systems, compressors, and industrial pumps where maintaining a pressure-tight seal is crucial to operational integrity. The performance of these seals directly impacts the equipment’s efficiency, reducing downtime and maintenance costs.
From an expertise standpoint, the materials used in the construction of high-pressure oil seals are paramount. Typically, these seals are crafted from materials like nitrile rubber, fluorocarbon, and PTFE composites. Each material offers distinct properties that cater to various temperature and pressure requirements. Fluorocarbon, for instance, is renowned for its excellent heat resistance and compatibility with a wide range of fluids, making it a preferred choice in rigorous conditions. Selecting the appropriate material ensures the seal can endure the specific operational environment, thus preventing premature failures.
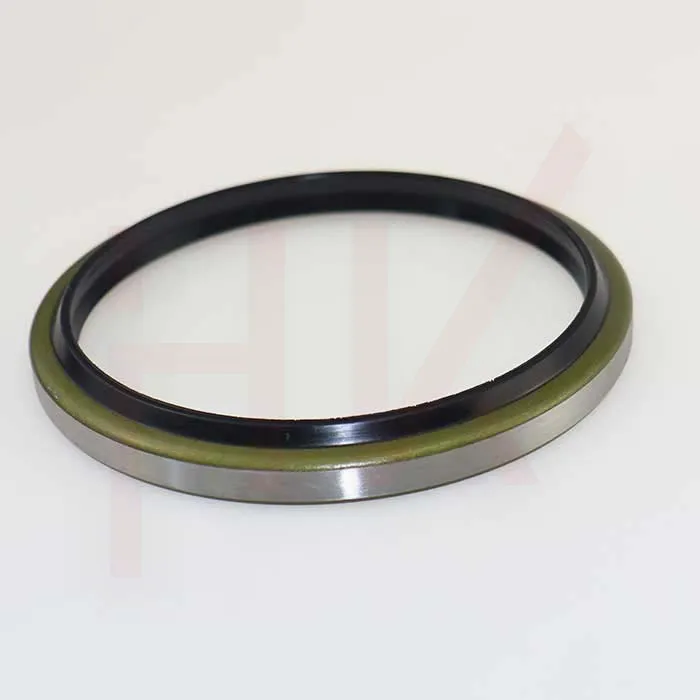
Authoritative insights from industry veterans emphasize the importance of understanding the operational parameters of the machinery where these seals are employed. Factors such as temperature fluctuations, pressure variations, and the type of fluids involved play a crucial role in determining the seal’s longevity and performance. It is recommended that businesses consult with experienced engineers and manufacturers to ensure the oil seal's specifications align with the application's demands. This approach not only enhances the reliability of the equipment but also builds a foundation of trust for the company supplying and using the seals.
oil seal high pressure
Trustworthiness in high-pressure oil seal products hinges on proven performance and adherence to industry standards. Leading manufacturers subject their seals to rigorous testing, simulating the harshest operating conditions to verify their efficacy. Certifications from recognized bodies further attest to the quality and capabilities of these seals. Customers are advised to seek seals that not only meet but exceed these standards, ensuring peace of mind and functional reliability.
Real-world experiences from engineers and maintenance teams further underline the critical nature of choosing the right oil seal. Case studies reveal scenarios where suboptimal seal selection led to costly repairs, safety hazards, and extended downtime. Conversely, a carefully chosen, high-quality seal often becomes the unsung hero, consistently outperforming expectations and reinforcing the dependability of the machinery.
In conclusion, while the upfront cost of a high-pressure oil seal may be a consideration, it is imperative to view it as an investment in maintaining the equipment’s efficacy and safety. Expertise in selecting the correct oil seal based on material, application, and manufacturer credibility is vital. Valuing expertise, authoritativeness, and trustworthiness in supplier partnerships and product selection will ultimately drive operational success and long-term savings in industrial applications.