High pressure oil seals are a critical component in ensuring the seamless operation of machinery across various industries. These seals play a pivotal role in maintaining the integrity of lubrication systems, preventing the ingress of contaminants, and ensuring that oil does not leak. The importance of utilizing high-quality oil seals cannot be underestimated, especially in high-pressure environments where the stakes are remarkably high.
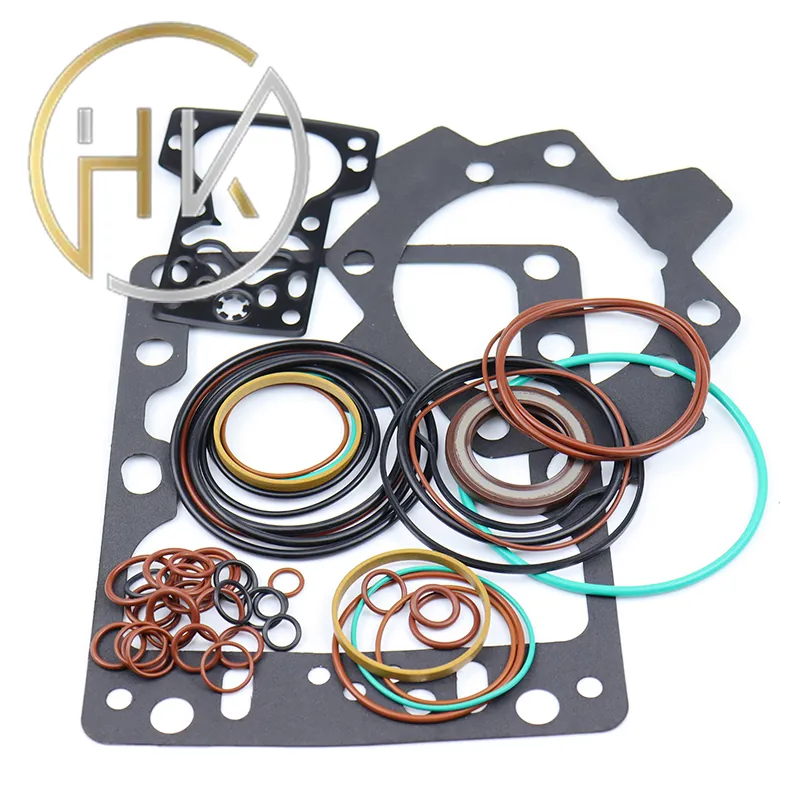
The necessity for high pressure oil seals becomes evident in industries such as automotive manufacturing, heavy machinery, aeronautics, and marine engineering. These seals are specifically designed to withstand extreme conditions, providing a robust barrier between essential components and harmful external elements.
In the automotive industry, for instance, high pressure oil seals ensure that engine components operate smoothly and efficaciously. They prevent leakage of lubricants which could otherwise result in expensive repairs or irreparable damage. The seals are crafted from materials that endure high temperatures and pressures. Their durability affords vehicles longer lifespans and improved reliability.

The expertise in developing high pressure oil seals comes from a blend of rigorous research and advancements in material science. Industry professionals conduct exhaustive material testing to ascertain that these seals can handle both static and dynamic conditions. Materials like fluoroelastomers, silicone, and PTFE are often employed due to their remarkable thermal and chemical resistance. The manufacturing process also incorporates precision engineering, ensuring these seals achieve the exact fit and tolerance necessary for optimal performance.
Furthermore, the credibility of manufacturers rests on their track record of producing oil seals that surpass industry standards. Manufacturer expertise is bolstered through collaborations with leading research institutions, ensuring that the development process incorporates cutting-edge innovation. Trustworthiness in this sector hinges on quality control certifications and compliance with international standards like ISO and SAE. These certifications exemplify a commitment to quality and customer satisfaction, showcasing a manufacturer's authority in the field.
high pressure oil seals
Real-world experience validates the critical metrics required for these seals to perform under high pressure. Engineers and mechanics with years of hands-on experience provide insights into the challenges faced in the field. Their feedback is invaluable in understanding operational challenges and optimizing seal performance. It is through these interactions that continuous improvements and innovations are achieved, reinforcing the pre-eminent position of high pressure oil seals in industrial applications.
To leverage existing technology and address future needs, the ongoing evolution of oil seal technology focuses on sustainability and environmental impact. Utilizing eco-friendly materials and refining the manufacturing processes help in reducing the carbon footprint of these essential components.
Ultimately, the balance between advanced design, material excellence, and empirical feedback creates a benchmark for the production of high pressure oil seals that not only meet but exceed expectations. The commitment to quality, combined with a profound understanding of operational dynamics, ensures that high pressure oil seals remain indispensable in maintaining the efficacy and reliability of machinery in demanding settings.
In conclusion, high pressure oil seals are vital to operational efficiency, offering significant protection and longevity to industrial equipment. Their importance cannot be overstated, as they are essential in safeguarding against operational failures due to leaking or contamination. As technology progresses, these seals will continue to evolve, meeting the increasing demands of modern machines and setting new standards in quality and performance.