High pressure lip seals are vital components in a wide array of industrial applications, serving as a barrier that prevents the leakage of fluids between mating surfaces under high pressure conditions. These ingenious devices are engineered to endure extreme environmental situations, making them indispensable in sectors such as automotive, aerospace, and heavy machinery.
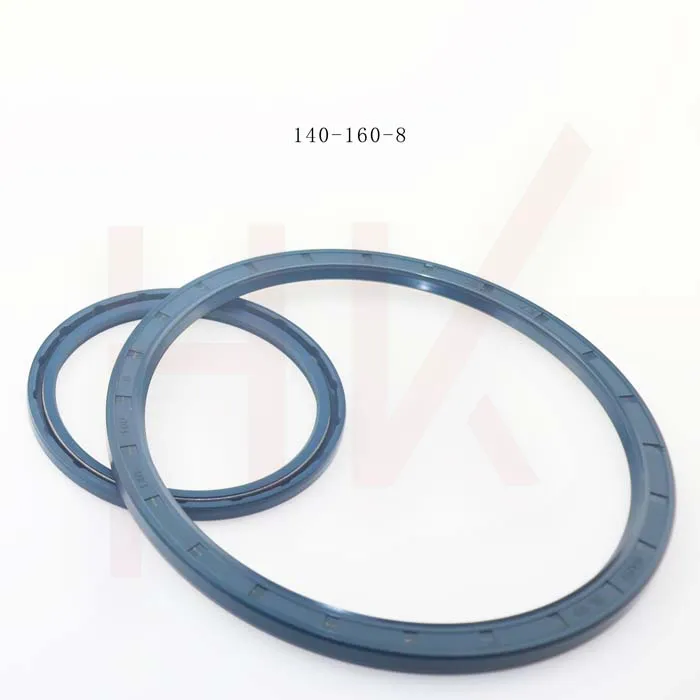
Understanding the essential role of high pressure lip seals requires delving into their construction and the materials utilized in their manufacture. These seals are typically made from durable materials such as polytetrafluoroethylene (PTFE), nitrile rubber, and fluorocarbon rubber, each offering specific properties suitable for different pressures and temperatures. PTFE, for example, provides excellent chemical resistance and can function at temperatures exceeding 200°C, making it an ideal choice for extreme conditions.
One critical aspect of these seals is their ability to withstand high rotational speeds. The design of the lip—which makes contact with the rotating shaft—is crucial.
A perfectly contoured lip reduces friction, thus minimizing wear and extending the seal's life. Engineers often employ advanced computational simulations to refine lip designs, ensuring optimal performance under various operational parameters.
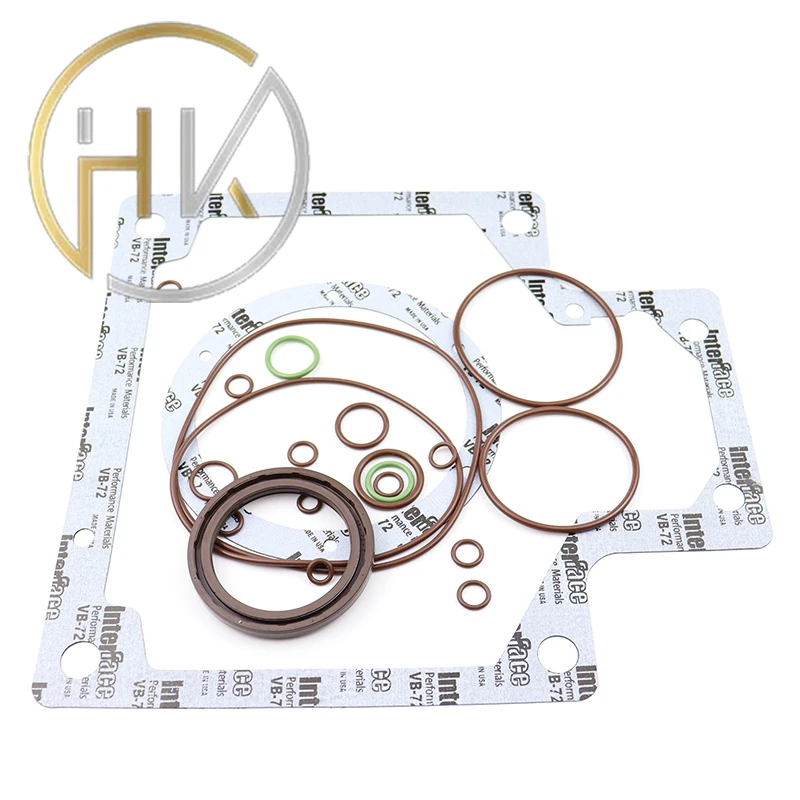
The expertise of manufacturers in producing high pressure lip seals cannot be overstated. Manufacturing these seals involves precision engineering to meet specific industry standards and application requirements. Manufacturers utilize advanced technologies such as computer numerical control (CNC) machining and laser sintering to ensure every seal meets the precise specifications necessary for high-pressure applications.
Expertise is further demonstrated through rigorous testing, which high pressure lip seals must undergo to ensure reliability and performance. This testing includes high-speed rotation trials, extreme temperature exposure, and chemical resistance assessments. Such comprehensive testing ensures that when these seals are deployed in real-world conditions, they perform flawlessly, maintaining their integrity and functionality.
high pressure lip seal
The authoritative nature of manufacturers specializing in high pressure lip seals is often reflected in their extensive experience and research and development capabilities. These companies invest heavily in innovation, exploring new materials and design enhancements that push the boundaries of what these seals can achieve. This authoritative position is backed by global certifications that guarantee compliance with international standards, bolstering trust among their clients.
Trustworthiness, a key component in selecting a high pressure lip seal supplier, is built on a foundation of proven performance and a long-standing reputation for quality. Reputable manufacturers often provide detailed documentation and traceability of their products, ensuring clients have all the necessary information regarding material composition, testing results, and operational guidelines. This transparency fosters confidence and offers clients assurance that they are investing in a product that will deliver as promised.
In product applications stretched across various sectors, the effectiveness of high pressure lip seals is a testament to the innovation and expertise that drives their development. In the automotive industry, for instance, these seals are critical in engines and transmissions, where they prevent oil leakage and contamination. In aerospace, they help ensure the integrity of hydraulic systems, critical to the operation of control surfaces and landing gear.
Moreover, high pressure lip seals contribute significantly to the efficiency and safety of heavy machinery used in mining and construction. By preventing the ingress of dirt and debris, these seals extend the lifespan of bearings and other critical components, reducing maintenance costs and downtime.
The combination of experience, expertise, authoritativeness, and trustworthiness embodied in the field of high pressure lip seals ensures that these components continue to meet the stringent demands of modern industry. The ongoing commitment to research and development promises even more advanced solutions in the future, enhancing performance and reliability. As industries evolve, the integral role of high pressure lip seals in ensuring efficient, safe, and leak-free operation remains a constant, underlining their essential place in the world of engineering.