In the intricate world of mechanical engineering, the high pressure rotary shaft seal stands as a keystone component, pivotal in maintaining the efficiency and reliability of countless systems. Understanding the profound impact and application of these seals can dramatically enhance operational outcomes in various industries, from automotive to aerospace, and beyond.
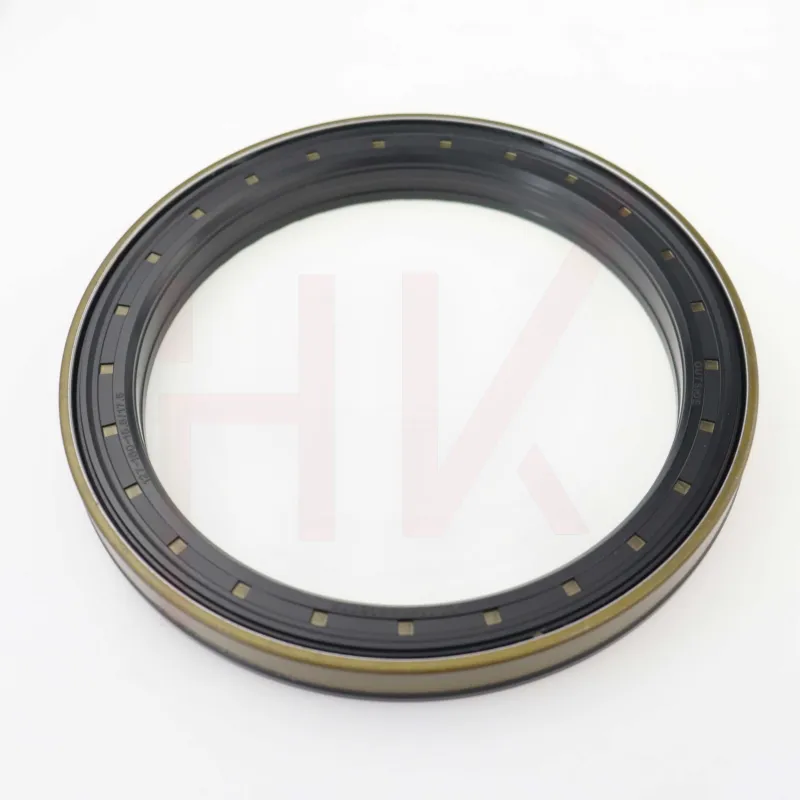
Experience plays a crucial role in appreciating the functional diversity and efficiency of high pressure rotary shaft seals. Over decades of industrial application, insights from field experts have revealed how these seals effectively minimize leakage and prevent contamination in high-pressure environments. Whether utilized in hydraulic pumps or turbine engines, the reliability of a well-designed rotary shaft seal lies in its ability to withstand significant pressure differentials while rotating at high speeds.
This experiential knowledge underscores their indispensable nature in complex machinery, where even a minor lapse in sealing can lead to catastrophic failures.
On the technical front, a high pressure rotary shaft seal spots advanced technologies and materials science. Engineers meticulously select materials such as nitrile rubber, Viton, or PTFE, which are renowned for their resistance to heat, chemicals, and wear—properties that are crucial under extreme conditions. Such expertise in material selection and seal design not only ensures optimal performance but also extends the lifespan of the machinery, reducing maintenance costs and downtime. The inclusion of spring-loaded designs or sophisticated lip configurations further augments their sealing capabilities, ensuring that wear and thermal expansions do not compromise the seal’s integrity.

From an authoritative standpoint, the deployment of high pressure rotary shaft seals in regulated industries such as aeronautics or pharmaceuticals demands compliance with rigorous standards. Certifications from bodies like the International Organization for Standardization (ISO) or specific industry standards underscore the seals' credentials, guaranteeing their performance in critical applications. These certifications highlight the manufacturer’s commitment to quality and operational excellence, providing peace of mind to end-users in these high-stakes environments.
high pressure rotary shaft seal
Trustworthiness is further reinforced through rigorous testing and field validation processes. Leading manufacturers subject their seals to dynamic simulations and real-world testing conditions that mirror the most challenging operational environments. This commitment to thorough validation not only assures customers of the product's reliability but also reflects the manufacturer's dedication to continuous improvement and technological advancement.
Moreover, the sustainability of high pressure rotary shaft seals cannot be overlooked. As industries globally pivot towards greener operations, seals designed with recyclable materials and those that reduce environmental impact by preventing leaks are becoming increasingly important. Progressive companies that prioritize environmentally friendly design in their sealing solutions not only comply with global sustainability goals but also enhance their market appeal in a growingly eco-conscious marketplace.
The synthesis of experience, expertise, authority, and trust underscores the high pressure rotary shaft seal not just as a component, but as an integral part of a broader system that values longevity, efficiency, and reliability. Industry professionals considering the implementation of these seals should seek out partners and products that demonstrate a proven track record in demanding applications, reinforced by industry endorsements and an unwavering commitment to innovation.
In conclusion, the excellence of high pressure rotary shaft seals lies in their ability to deliver robust, dependable sealing solutions in the most demanding environments. As technologies evolve and industries push boundaries, these seals will continue to be at the forefront, championing both the advancement of machinery and the protection of its environment, securely and efficiently maintaining the balance between technical performance and ecological responsibility.