Navigating the intricacies of high pressure rotary seals requires an understanding of their critical role in various industrial applications. High pressure rotary seals are vital components used to maintain an effective seal in rotating machinery operating under high pressure conditions. This article delves into the significance of these seals, their application in diverse industries, and the advancements that resonate with experts' insights while bolstering authority and trust in their reliable performance.
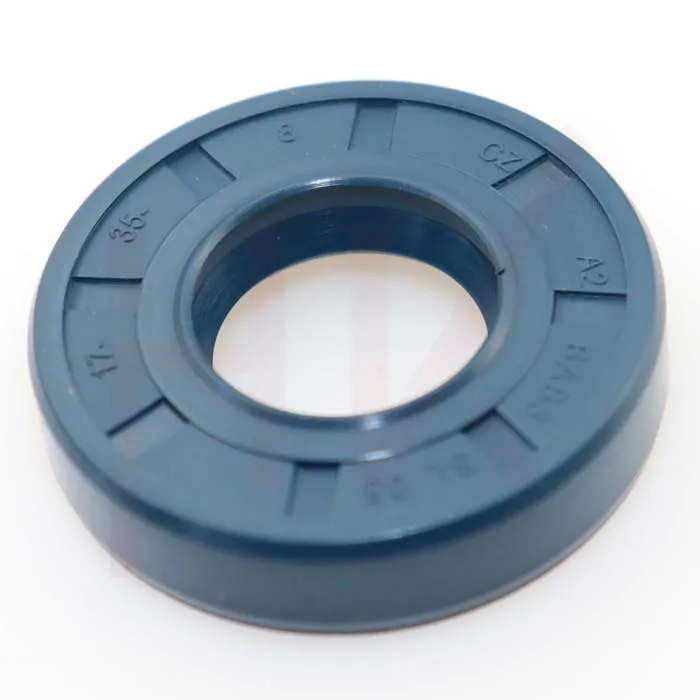
High pressure rotary seals are engineered to function under elevated pressures, ensuring that fluids do not escape and contaminants do not enter the system. Their precision design and composition are crucial for the success of equipment ranging from industrial pumps and compressors to hydraulic motors and drilling machinery. With industries increasingly demanding efficiency and reliability, high pressure rotary seals serve as the linchpin ensuring optimal performance and longevity of such equipment.
The unique design elements of high pressure rotary seals include the use of specialized materials and structures capable of withstanding high stress environments. Materials such as high-grade elastomers, PTFE, or metal are often employed for their ability to resist pressure, temperature fluctuations, and chemical exposure. The design may incorporate advanced features like multiple lip configurations, which enhance sealing capability while reducing wear, thus optimizing the service life of the seal.
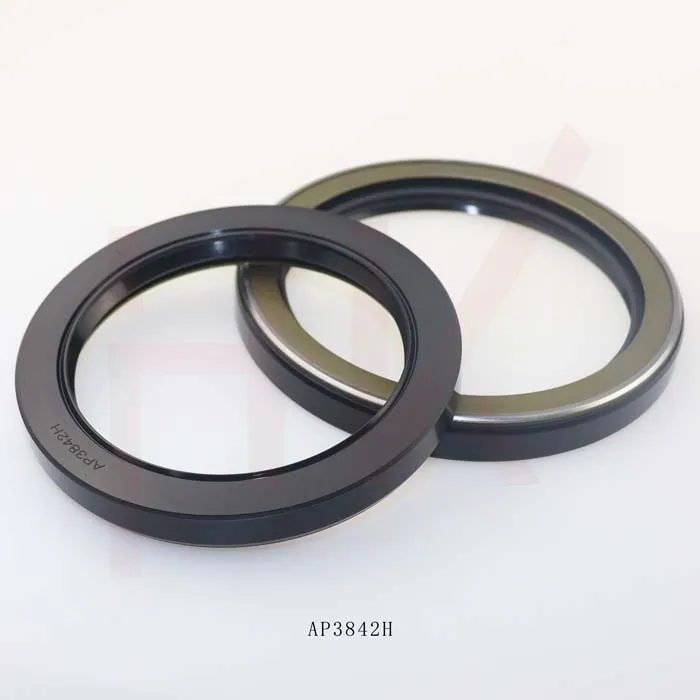
Incorporating feedback from industry veterans, many manufacturers have advanced the science behind these seals. Innovations such as computer-aided design (CAD) tools enable designers to simulate conditions that the seal will encounter, allowing precise tailoring of seals to specific applications. This focus on tailored solutions aligns with expert opinions on the necessity of personalized engineering to meet unique operational challenges. Such customization not only enhances performance but also minimizes the risk of equipment failure, improving the overall trustworthiness of the machinery.
The credibility and authority of high pressure rotary seals are further evidenced by their rigorous testing and certification. Standardized testing protocols, such as ISO standards, are applied to ensure that these seals can handle the pressures they are designed for. Endorsements from third-party testing bodies and adherence to industry standards bolster the seals' reputation, reinforcing their place as an authoritative solution in high-stakes environments.
high pressure rotary seal
Beyond theory, real-world applications provide compelling insights into the indispensable nature of high pressure rotary seals. In the oil and gas industry, for instance, these seals are subjected to harsh operational conditions, including exposure to corrosive substances and extreme temperatures. The seals' robustness in such scenarios confirms their role in preventing catastrophic leaks, safeguarding the environment, and ensuring energy security. Such performance underscores the expertise embodied in their design and manufacturing processes.
Another sector benefiting immensely from high pressure rotary seals is the chemical processing industry. The ability of these seals to prevent cross-contamination between reactive substances is crucial.
Seals designed for these environments must not only withstand pressure but also provide chemical inertness. The development of seals with these properties is pivotal, as endorsed by chemical engineers who emphasize safety and reliability as paramount.
As technology evolves, so does the field of high pressure rotary seals. The integration of smart technologies, such as sensors that monitor seal integrity in real-time, is a growing trend. These advancements offer predictive maintenance opportunities, allowing users to address potential issues before they result in failure. This proactive approach enhances trust in the machinery's operational efficacy and demonstrates an expert understanding of emerging technological instruments aiding seal performance.
In sum, the realm of high pressure rotary seals extends beyond simple mechanical components. They epitomize a blend of engineering prowess, material science innovation, and authoritative standards that collectively reassure industries of their performance capabilities. As industrial demands intensify, the continued evolution of these seals guided by expert insights and real-world experiences remains crucial. This commitment to excellence ensures that high pressure rotary seals will continue to be a cornerstone technology, maintaining their esteemed status in modern industry and securing their place as a trusted resource for engineers and decision-makers worldwide.