In the realm of industrial machinery, construction vehicles, and even general automotive maintenance, seals play a fundamental role in ensuring optimal performance and longevity of equipment. Specifically, dust seals and oil seals are two critical components that, despite their underlying similarities, serve distinctly different functions. Understanding these differences not only helps in making informed purchasing decisions but also in enhancing the efficiency and lifespan of your machinery.
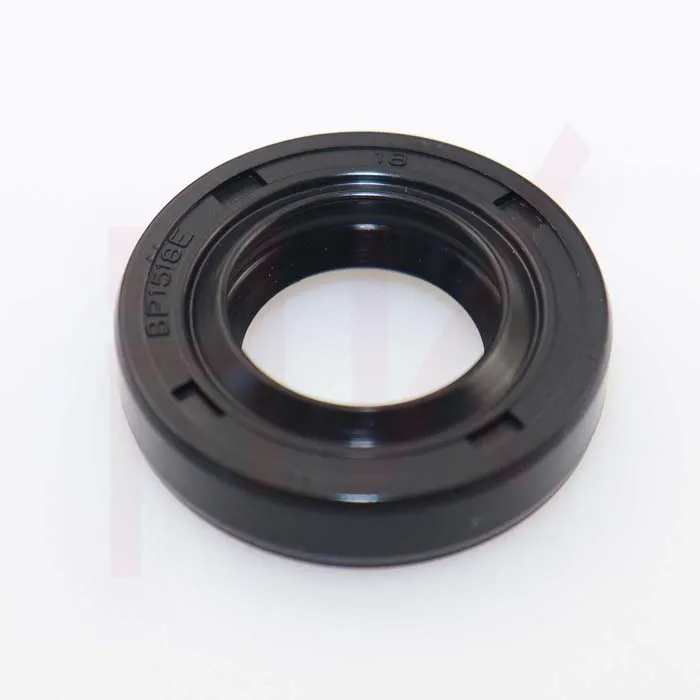
Dust seals are primarily designed to keep particulate contaminants, such as dust, dirt, and sand, away from sensitive components. They are integral in environments where cleanliness is paramount but there isn't frequent exposure to liquid lubricants. Think of applications in dry, particulate-heavy contexts like construction sites or areas prone to windblown dust. Their composition often includes materials like rubber or plastics that are resistant to abrasion while allowing for a snug fit against the moving parts.
The design of a dust seal emphasizes flexibility and durability. In scenarios like off-road machinery operation, where dust clouds are commonplace, these seals prevent contaminants from infiltrating critical joints and bearings. This minimizes wear and tear and maintains the smooth operation, crucial for reducing maintenance costs and downtime. Users frequently report improvements in equipment longevity and operational efficiency after installing high-quality dust seals, underscoring their effectiveness.
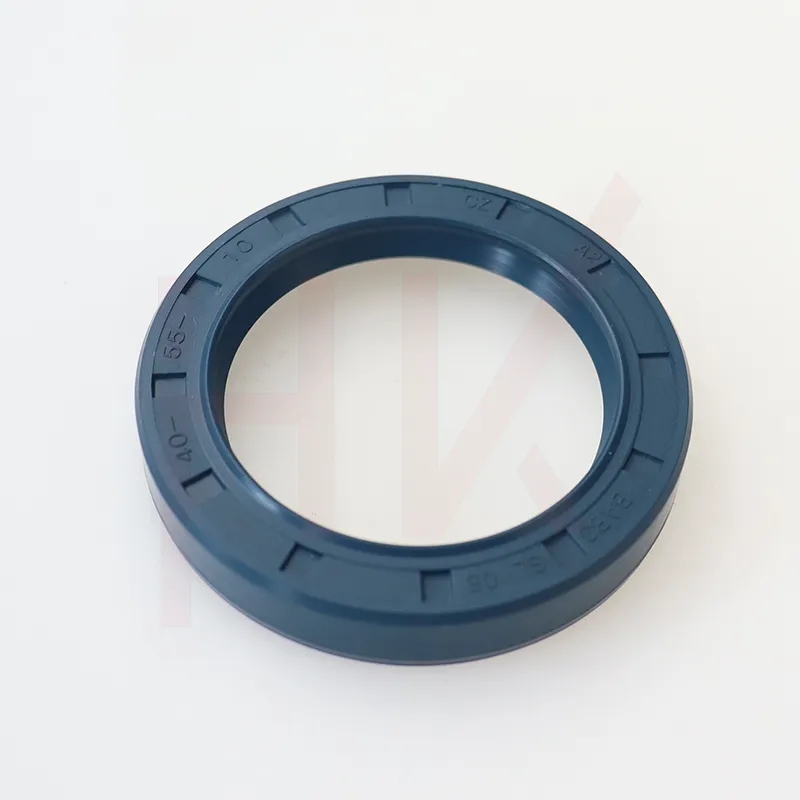
In contrast, oil seals, also known by industry veterans as rotary shaft seals, serve a dual purpose. Primarily, they retain lubricants critical for the smooth operation of mechanical systems. Simultaneously, they prevent contamination of these lubricants by external contaminants. The oil seal is quintessential in applications involving rotary motion where lubricants are vital for minimizing friction and wear. Their structure typically includes a flexible lip, a garter spring to maintain pressure, and a metallic or plastic casing that inserts snugly into housings.
This precise engineering allows oil seals to cope with the complexities of preventing lubricant leakage while keeping harmful substances at bay. A common example is the crankshaft in automotive engines where oil seals prevent the leakage of engine oil, ensuring optimal functioning and efficiency. Experts in mechanical maintenance point out that the proper selection and installation of oil seals can dramatically improve machinery reliability, with users often observing improved energy efficiency and longer service intervals.
dust seal vs oil seal
Integrating the insights from seasoned technicians and engineers, several considerations emerge when choosing between dust seals and oil seals for industrial applications. Longevity and material compatibility rank high on the checklist. For environments dominated by abrasive particles, dust seals made from highly durable elastomers or thermoplastics are ideal. In contrast, machinery with rotating shafts that require consistent lubrication will benefit more from oil seals made of advanced nitrile rubber or fluoroelastomer compositions, known for their resilience to high temperatures and aggressive chemicals.
A significant point often highlighted by industry professionals involves the seal's environment. While dust seals are championed for their simplicity and effectiveness in dry, dusty environments, oil seals are preferred for applications involving exposure to oils, grease, or other lubricants. This division of function is foundational, and selecting the wrong seal type can lead to premature seal failure or reduced equipment performance. Thus, consulting with a sealing specialist or engineer can offer invaluable personalized advice on application compatibility.
The expertise gained from real-world applications consistently emphasizes that routine checks and proper seal maintenance should not be overlooked. This proactive approach is supported by extensive anecdotal evidence from the field proving that well-maintained lubrication and dust exclusion systems translate to smoother operation and prolonged equipment life. DIY enthusiasts and professionals alike are advised to adhere to the manufacturer's installation instructions and industry best practices to optimize seal performance.
Ultimately, the choice between dust seals and oil seals hinges on the operational demands and environmental conditions specific to each application. Both types are indispensable in their rights, with their effectiveness largely determined by the proper matching to task-specific requirements. From safeguarding mechanical integrity on a dusty outdoor construction site to reliable lubricant retention in high-speed rotating machinery, these seals are vital to achieving uninterrupted operation and reducing unexpected failures — a priority for any serious operator seeking to uphold excellence in machinery performance.