In the world of industrial machinery, where precision and durability are paramount, the often-overlooked component, the shaft dust seal, plays a critical role. This tiny but mighty part serves as a lifeline for many machines, ensuring optimal performance and longevity. Let's explore why shaft dust seals are indispensable, their various applications, and the considerations for selecting the right one, emphasizing a blend of experience, expertise, authority, and trust.
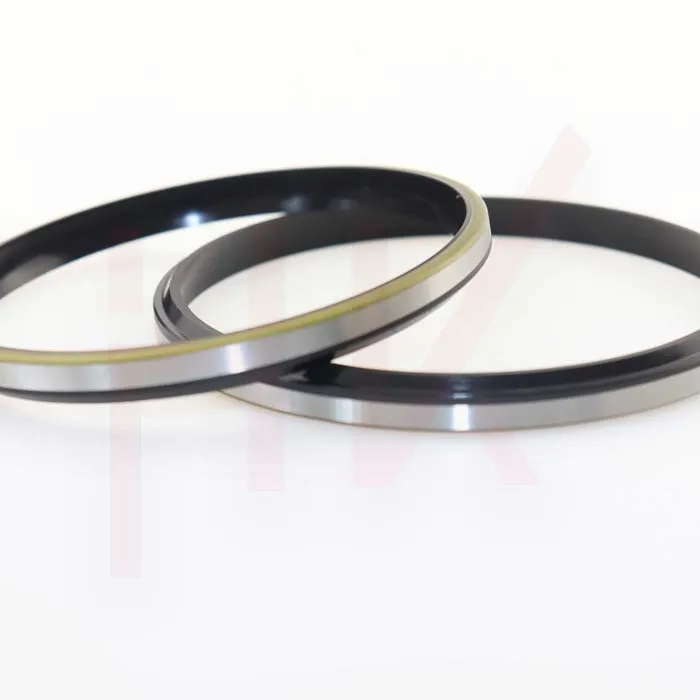
Shaft dust seals might be small, but they are essential components safeguarding the internal workings of mechanical systems. They are designed to prevent dust, dirt, and other contaminants from infiltrating an engine or machine's internal parts. Without these seals, foreign materials could cause extensive wear, resulting in inefficiencies and costly maintenance. This protective function ensures that equipment stays in peak condition, minimizing downtime and extending lifespan.
Specialized knowledge in manufacturing high-performance dust seals has led to innovations that address the nuanced needs of different industries. Materials such as rubber, metal, or polymer composites are used based on the environment and the machinery's requirements. Each material offers distinct advantages rubber provides excellent flexibility and sealing capabilities, metals offer robustness and resistance to harsh environments, and polymers deliver precision with minimal friction. Selecting the appropriate material is crucial for achieving the best performance and durability in specific applications.
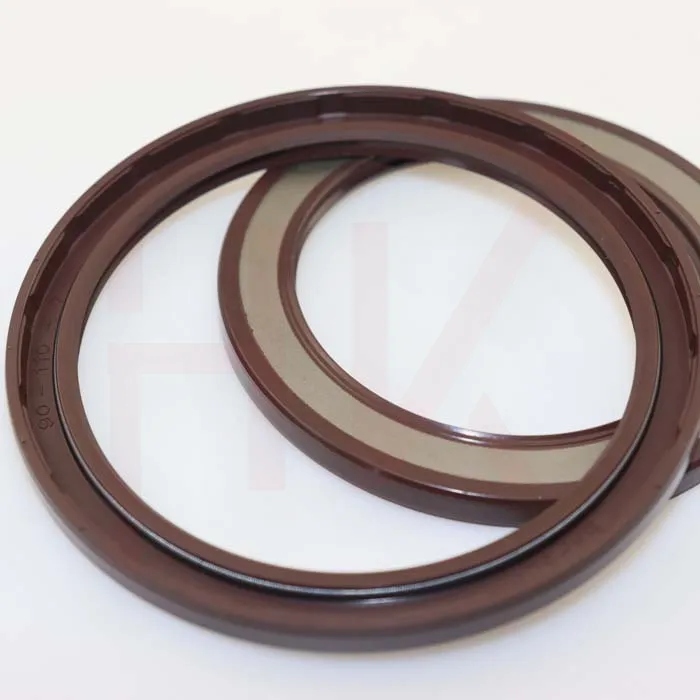
Shaft dust seals find their utility across various sectors, including automotive, aerospace, food processing, and heavy machinery. In the automotive industry, they are crucial for protecting the transmission and engine components. The aerospace sector relies on them for ensuring the integrity of critical systems subjected to extreme conditions. Meanwhile, food processing plants utilize seals that adhere to stringent health standards to prevent contamination and ensure product safety. Each application underscores the significance of using high-quality, reliable seals tailored to industry needs.
shaft dust seal
Choosing the right shaft dust seal requires an understanding of not just the machinery and environment, but also the operating conditions such as temperature, pressure, and rotational speed.
Experts recommend a comprehensive analysis of these factors before selecting a seal. The wrong choice can lead to premature failure, jeopardizing equipment performance and safety. It's not merely about fitting a seal into a groove; it's about integrating a component that will seamlessly complement a machine’s operations under varied conditions.
Trust in the expertise of established manufacturers is vital in the procurement of shaft dust seals. Leading firms often possess certifications and adhere to international standards, offering peace of mind regarding product quality and reliability. They provide technical support and bespoke solutions, ensuring that each seal meets specific needs and conditions. Their commitment to quality and innovation is supported by years of research and development, backed by real-world testing—key indicators of their authority in the field.
Establishing a trustworthy relationship with suppliers ensures continuous improvements in equipment performance and a reduction in overall operational risks. Engaging with providers who offer detailed documentation, clear communication, and consistent quality audits builds confidence, making them reliable partners in maintenance and operations.
By understanding the nuanced demands and applications of shaft dust seals through the lens of experience, expertise, authority, and trustworthiness, industries can make informed decisions. This not only enhances the equipment's operational efficiency but also bolsters the company's bottom line by minimizing unnecessary maintenance and replacement costs. In conclusion, while shaft dust seals may appear insignificant at first glance, their role is integral, and the importance of choosing the right one cannot be overstressed. Prioritizing quality and performance in these components fosters an environment of reliability and prolonged success in any industrial endeavor.