Oil seals, often referred to as rotary shaft seals or lip seals, serve as small but mighty components that hold significant importance in a wide array of machinery across industries. Their primary function revolves around sealing the spaces between stationary and moving components within mechanical equipment, keeping lubricants in and contaminants out. This seemingly simple task is foundational to the efficiency and longevity of numerous mechanical systems, establishing oil seals as essential for both precision and performance-driven applications.
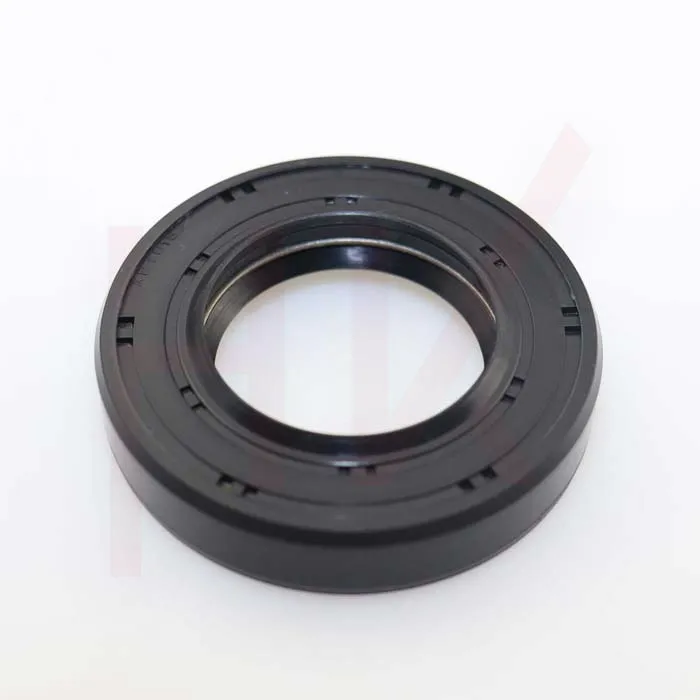
Experience in the field of mechanical engineering and maintenance has shown that the use of oil seals directly impacts the operational capabilities of the equipment. For example, in a real-world scenario involving industrial machinery, any compromise in oil seal integrity often leads to equipment downtime due to the intrusion of foreign particles or leakage of crucial lubricants. This emphasizes the need for regular inspection and maintenance to ensure seal integrity, extending equipment lifespan and maintaining optimal performance.
From an expertise standpoint,
understanding the construction and material composition of oil seals is key. These components are typically composed of elastomers or polymers combined with metals, allowing for flexibility and durability under demanding conditions. Specific materials, such as nitrile rubber or silicone, might be selected based on the operating environment — whether it faces extreme temperatures, exposure to chemicals, or requires a high degree of elasticity. Therefore, choosing the right material is imperative, underlining the technical know-how required for effective application.
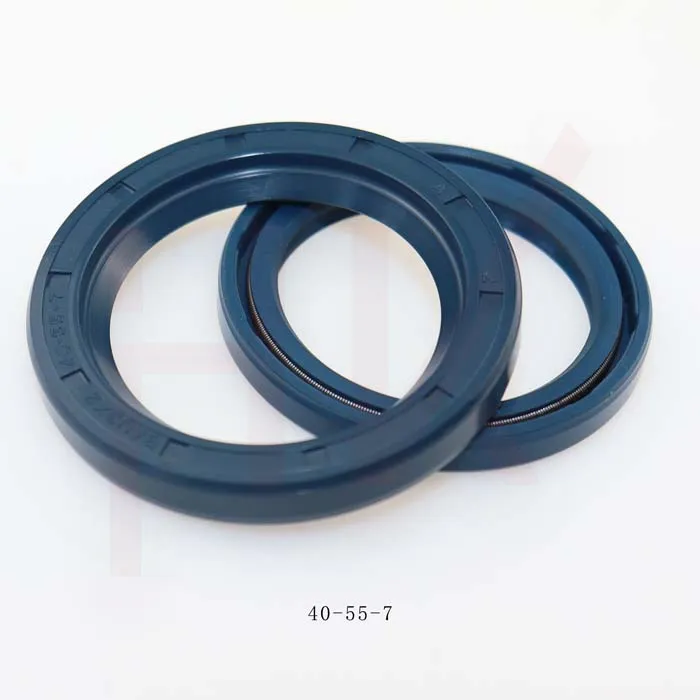
The authoritativeness of oil seals can be highlighted through their profound impact on mechanical systems' reliability. The manufacturers of these seals often undergo rigorous testing and adhere to precise manufacturing standards to ensure that their products can withstand the high stress and varied environments of their applications. Futuristic approaches incorporate the latest technological advancements in material science to develop seals that are more robust and versatile than ever before, enhancing their role in critical sectors like automotive, aerospace, and heavy machinery.
what is the purpose of oil seal
Trustworthiness in oil seals comes from both a brand and a performance perspective. Leading manufacturers who prioritize quality assurance, supported by certifications and customer testimonials, significantly impact the perceived reliability of their products. Additionally, proper installation and adherence to maintenance schedules are crucial to ensuring that oil seals function as intended. Incorrect installation can lead to premature failure, causing more than just simple leaks but also potential damage to the machinery.
In exploring the future of oil seals, the focus is not only on achieving function but also on enhancing their environmental compatibility. Innovations in the use of eco-friendly materials and processes reduce the environmental footprint of oil seals, aligning with global sustainability goals and addressing consumer and regulatory demands for greener technology.
In summary, oil seals are indispensable components in the realm of mechanical systems, serving the critical role of safeguarding operations by maintaining the integrity of fluids within machinery. Their design, material composition, and functional performance underscore a strong level of expertise and technical flexibility. As technology and industry needs evolve, oil seals continue to adapt, standing as a testament to innovation, accountably supporting the machinery that drives industries forward. Thus, understanding and optimizing the application of oil seals is not merely a technical necessity but a strategic consideration pivotal to industrial success and sustainability.