Dust lip seals are an indispensable component in many industries, providing protection and efficiency in machinery and equipment. They serve as a barrier, preventing dust and other contaminants from entering critical components of machinery, thereby safeguarding against wear and deterioration. Implementing the right type of dust lip seal can greatly enhance the longevity and performance of equipment, making their selection and maintenance a focal point for engineers and maintenance professionals.
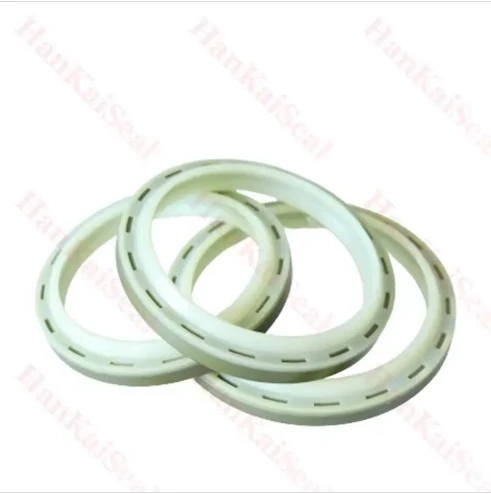
Experience with dust lip seals reveals their essential role in a broad array of applications, including automotive, industrial machinery, and heavy equipment. In the automotive industry, these seals are crucial in axles and steering systems, preventing the ingress of harmful particles that could compromise the vehicle’s performance. Similarly, in industrial settings, they are employed in pumps and compressors where a dust-free operation is crucial for optimal functioning and reliability.
From a professional perspective, selecting the appropriate dust lip seal requires a nuanced understanding of the operating environment and the materials involved. The seals must be resilient against the specific types of debris they are exposed to, as well as the temperatures and pressures of operation. Nitrile rubber, for example, is favored for its excellent resistance to oils and abrasion, making it suitable for automotive applications. On the other hand, silicone seals might be selected for their superior high-temperature performance and flexibility, offering advantages in equipment that operates in extreme conditions.
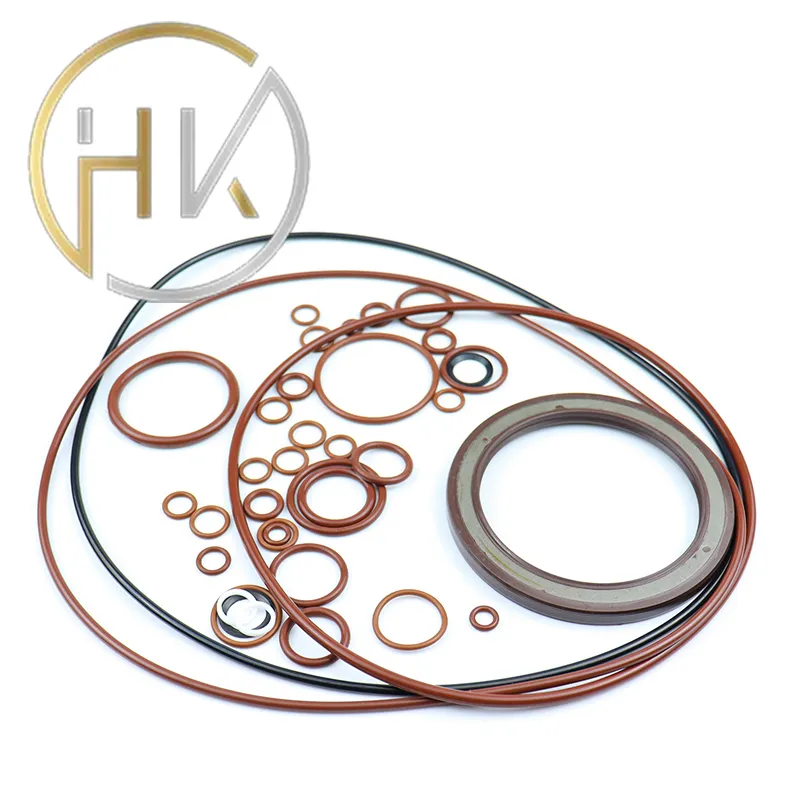
Authoritativeness in the domain of dust lip seals stems from a thorough comprehension of their design and materials. Engineers and designers look towards industry standards such as those from the American Society for Testing and Materials (ASTM) and the International Organization for Standardization (ISO) to ensure quality and compatibility. Following these standards not only assures the reliability of the dust lip seals but also guarantees that they will meet the rigorous demands of the machinery they are intended for. Moreover, manufacturers frequently invest in research and development to enhance the materials and designs of these seals, keeping pace with new technological advancements and emerging market needs.
Building trustworthiness in the use and selection of dust lip seals entails a combination of transparent communication from suppliers, high-quality product offerings, and consistent performance. Manufacturers demonstrate this by providing detailed specifications, test results, and certifications that verify the integrity and performance of their seals. This information empowers engineers to make informed decisions, ensuring that every seal meets the specific needs of their projects, thus minimizing risks and maximizing operational uptime.
dust lip seal
In practice, this means proactively conducting regular inspections and maintenance on machinery employing dust lip seals. Such inspections can identify early signs of wear or failure, allowing for timely interventions that prevent more serious problems. Moreover, training maintenance personnel to recognize different types of seal damage and the conditions that lead to degradation can significantly enhance the durability and effectiveness of these seals.
The utilization of technological tools and methods also plays a crucial role. Advanced simulation tools can predict the performance of seals under various conditions, helping in the selection of the most appropriate seal for any given application. Furthermore, ongoing monitoring technologies can provide real-time data on the operational conditions of the equipment, facilitating pre-emptive measures before seal failure occurs.
Ultimately, the expertise brought to the selection, installation, and maintenance of dust lip seals culminate in improved machine longevity, efficiency, and reliability. This not only reduces operational costs and downtime but also extends the life of critical machinery. When industries prioritize the optimal selection and management of dust lip seals, they are investing in the heart of their productive capacity, ensuring continued success and competitiveness in their respective fields.
This comprehensive exploration of dust lip seals underscores their significance across various industries, revealing why they must be chosen with care and maintained with diligence. As industrial demands continue to evolve, so too will the role of these essential components, driven by advancements in materials science and engineering excellence, promising even greater performance and protection in the future.