The world of industrial machinery thrives on the seamless operation of its diverse components, and among these, the bearing dust seal plays a crucial yet often overlooked role. In essence, the functionality of bearing systems is integral to the machine's overall performance, where dust seals ensure that the bearings remain untainted by external particles that could lead to wear and tear. This is where the experience of seasoned operators becomes invaluable, witnessing firsthand the distinction a high-quality dust seal can make.
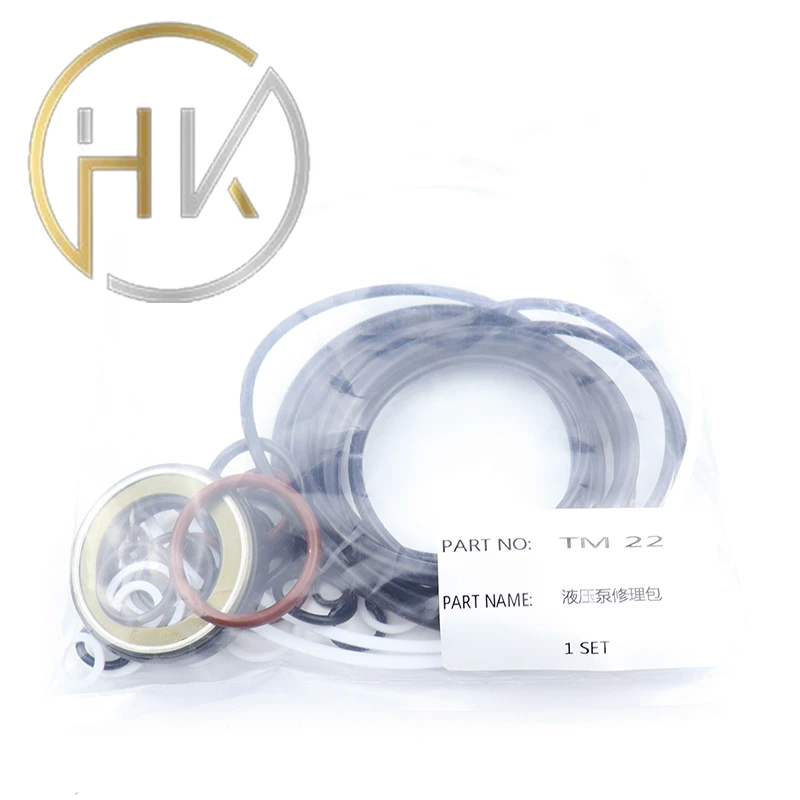
Dust seals are more than just ancillary components; they are the guardians of precision in bearings. When we delve into their design, they are meticulously engineered to fit snugly within the bearing assembly, effectively blocking out contaminants while allowing the free motion of the internal components. An expert in the field would highlight the importance of choosing the right material for these seals. The selection process is not arbitrary but rather contingent on the operational environment—high-temperature applications might necessitate a different material than those subjected to heavy moisture or corrosive elements.
Prolonged exposure to dust and debris can exponentially accelerate the degradation of bearings, leading to machinery downtime and unexpected maintenance costs. Herein lies the authority of manufacturers with deep roots in precision engineering, who understand that the durability and reliability of bearing dust seals are paramount. They invest in research and development to innovate materials such as advanced composites and specialized rubbers that offer superior resilience and performance longevity.
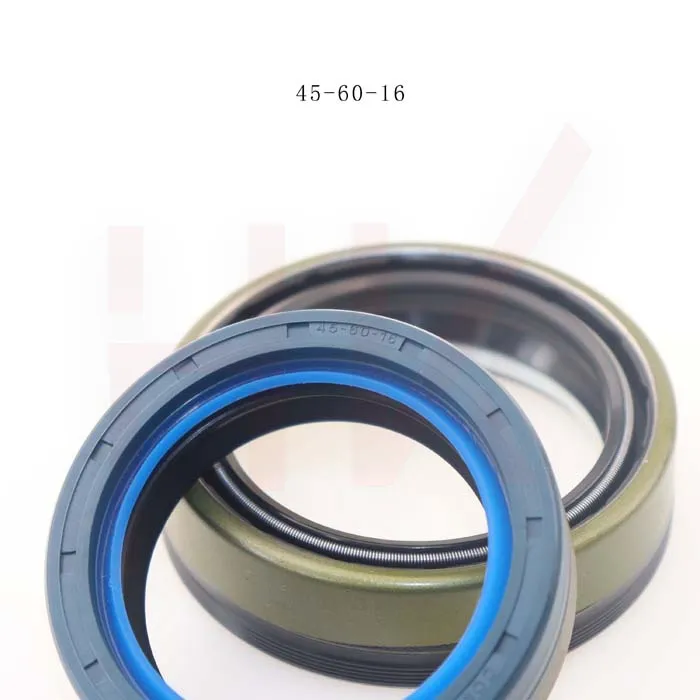
From the trustworthiness standpoint, companies that produce these dust seals continually enhance their manufacturing techniques, adhering to stringent quality controls. Industry certifications and adherence to international standards serve as a testament to their commitment to reliability, providing customers with assurance in their investments.
bearing dust seal
For maintenance professionals and engineers, the emphasis on the right dust seal is more than procedural; it is a practice grounded in expertise. They comprehend that regular inspections and replacements, as per manufacturer recommendations, can extend the life expectancy of the bearings significantly. Training modules and expert seminars also contribute to this knowledge pool, fortifying the expertise of personnel involved in the upkeep of these essential components.
The discussion on bearing dust seals cannot be complete without addressing innovation. As industries push towards automation and higher efficiency, the needs evolve. Smart dust seals embedded with sensors for real-time monitoring have started to make their debut. These innovations harness data analytics to predict wear patterns, ensuring timely interventions and reducing unexpected downtimes—a leap towards predictive maintenance.
While it's true that the bearing dust seal may seem like a small cog in the grand machinery setup, its impact is disproportionately large. In sectors such as automotive, aerospace, and heavy machinery, where precision and reliability are non-negotiable, investing in high-grade dust seals translates into unrestricted machine performance and unprecedented longevity.
In conclusion, the narrative surrounding bearing dust seals must shift towards recognizing them as pivotal to operational efficiency. They are the unsung heroes,
promoted by those with years in the field who understand their pivotal role. By marrying experience with material science and technological innovation, the industry continues to edge closer to maintenance-free bearing systems, setting new benchmarks in machinery reliability and performance. This confluence of expertise, authority, and trust not only safeguards the integrity of equipment but also catapults operational efficiency to new heights, setting the stage for an evolved industrial landscape.