In the realm of industrial machinery and hydraulic systems, the role of a hydraulic cylinder dust seal is often overlooked until its absence or failure disrupts a smooth operation. A component that might seem simple at first glance, the dust seal, actually stands at the forefront of ensuring peak performance and longevity of hydraulic systems. This article delves into the intricacies and paramount importance of dust seals, drawing on real-world experiences and the expertise of seasoned professionals in the field.
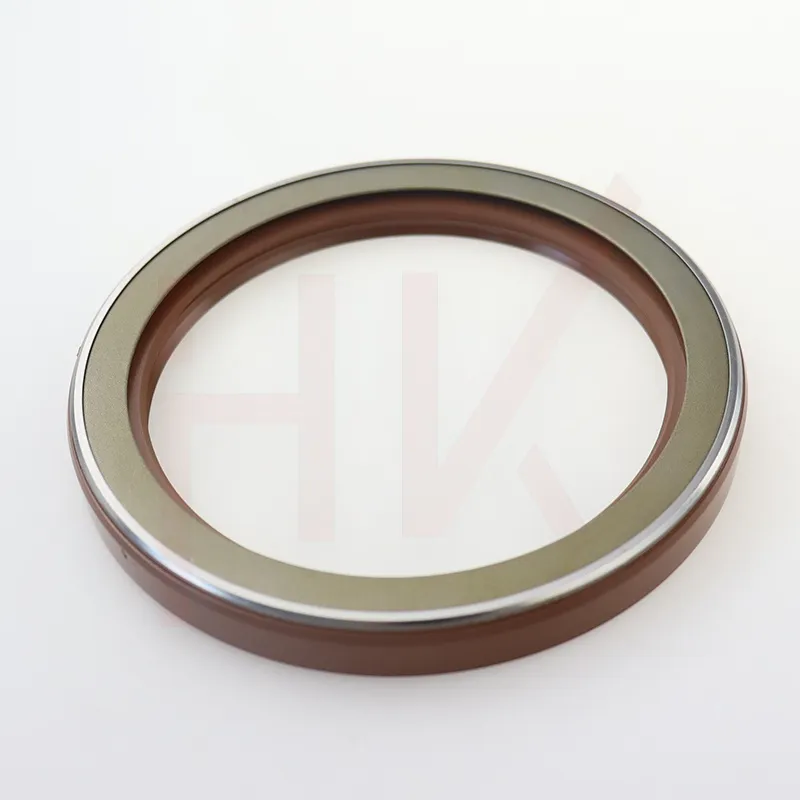
Dust seals, primarily crafted from high-quality synthetic rubber or polyurethane, act as sentinels that prevent contaminants such as dust, dirt, and grit from infiltrating the hydraulic cylinder. In environments laden with particulate matter, these seals safeguard the precision components within the cylinder, promoting a much-needed operational dependability. Imagine operating heavy machinery in a mining operation; without an effective dust seal, abrasive particles could easily breach the cylinder’s interior, leading to wear and tear, and, eventually, costly repairs and downtime.
For professionals in the industry, trusting the wrong seal can spell disaster. Expertise lies in understanding that not all dust seals are created equal; their design and material composition must align with the operational stressors of the specific application. For example, in environments exposed to extreme temperatures, selecting a seal material like Viton, which withstands such conditions, ensures reliability and peak performance.

Industry experts often emphasize the need for regular inspection and maintenance of dust seals. A proactive maintenance schedule, guided by expert advice, helps in early identification of wear or potential failure points, allowing for timely replacement. Trust in this process is built from the repeated successes observed in field operations, where a well-maintained seal system correlates directly with machine longevity and reduced operational costs.
The authority of dust seal manufacturers plays a critical role in the overall effectiveness of hydraulic systems. Leading manufacturers invest in R&D, constantly innovating to enhance seal design and material science. Their findings are documented and reviewed in industrial journals, contributing to the breadth of knowledge available on effective seal applications. This intellectual capital positions them as authoritative voices in the industry, offering peace of mind to clients who rely on their products to protect valuable machinery.
hydraulic cylinder dust seal
Customer testimonials add an additional layer of trustworthiness. Consider a construction company that integrated premium dust seals into their equipment and documented the aftermath—less unscheduled downtime, improved efficiency, and reduced repair costs. Such real-world experiences underscore the seal’s value proposition, rendering an abstract component into something tangible and indispensable.
While it may be tempting to cut corners, procuring sub-standard seals presents risks that far outweigh any upfront cost savings. Inferior seals sacrifice material integrity, leading to swift degradation under operational strain. For companies aiming to maintain a competitive edge, investing in quality dust seals is a prudent strategy that delivers measurable long-term benefits.
When selecting a supplier, engage with those boasting a proven track record, certifications, and robust quality assurance processes. Their commitment not only ensures superior product delivery but also offers expert consultancy, tailoring seal selection to the unique demands of your machinery. This strategic partnership maximizes the utility of hydraulic systems, ensuring they function with precision and longevity.
In summary, the critical role of hydraulic cylinder dust seals cannot be overstated. They are key protectors within the hydraulic system framework, offering frontline defense against operational adversities. By leveraging the expertise, experience, and industry authority of top-tier manufacturers, and trusting in their proven methodologies, companies can unlock the potential of their machinery, achieving exceptional operational reliability and success.