Cassette oil seals, often regarded as a cornerstone in modern machinery design, have transformed the way industries approach sealing solutions. Their unique construction and functionality make them indispensable in environments demanding reliability and durability. This article delves into the intricacies of cassette oil seals, providing insights drawn from extensive industry expertise and real-world applications.
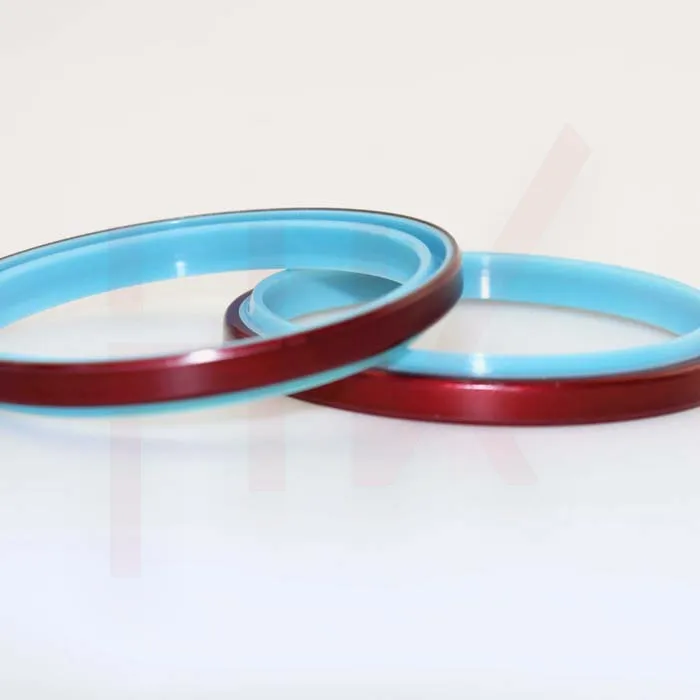
Experience in machine maintenance and repair frequently highlights the critical role cassette oil seals play in safeguarding mechanical components. These seals, distinguished by their compact and integrated design, encapsulate a multi-part seal within a single unit, effectively streamlining the installation and replacement process. This consolidation of parts not only simplifies assembly but also significantly reduces the risk of installation errors—common concerns in high-stakes industrial settings.
In environments where machinery is exposed to dirt, debris, and fluctuating pressures, the reliability of sealing solutions becomes paramount. Cassette oil seals excel in these conditions due to their unique design, which typically includes a metallic outer shell, ensuring robustness and enhanced protection against environmental contaminants. This design innovation is a testament to the expertise involved in their engineering, ensuring that the seal can withstand not just mechanical stress but also the harshest of operational environments.
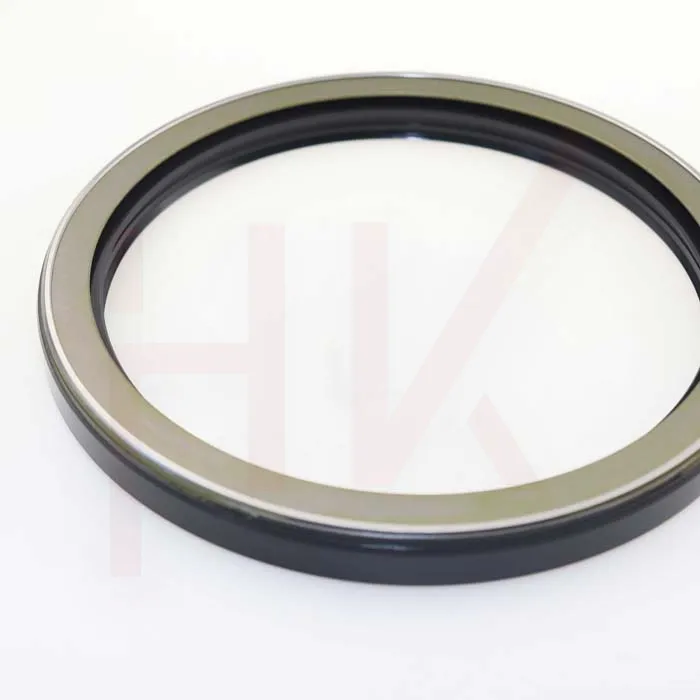
From an expert perspective, the versatility of cassette oil seals offers numerous advantages over traditional oil seals. Their integrated construction typically consists of a primary lip, secondary lips, and an outer case which together provide superior sealing capabilities against both grease and contaminants. This multi-lip configuration is expertly crafted to maintain an optimal contact pressure against the shaft, compensating for any shaft misalignments and reducing wear over prolonged use—an essential consideration in extending the service life of machinery.
cassette oil seal
The authority of cassette oil seals in industrial applications is further reinforced by their widespread adoption across various sectors, including automotive, agricultural, and heavy machinery industries. Manufacturers of these seals are frequently at the forefront of technological advancements, utilizing cutting-edge materials and manufacturing processes to enhance seal performance. For instance, the integration of advanced elastomers and proprietary coatings contributes to improved temperature resilience and reduced friction, marking a leap forward from traditional sealing solutions.
In assessing the trustworthiness of cassette oil seals, it is crucial to consider the rigorous testing and quality assurance protocols they undergo. Leading manufacturers employ extensive laboratory and real-world testing to ensure that their seals meet stringent regulatory standards and perform reliably under various conditions. This commitment to quality is reflected in the comprehensive warranties often provided, giving end-users confidence in their investment.
Moreover, the economic implications of implementing high-quality cassette oil seals are significant. By reducing maintenance cycles and minimizing downtime due to seal failure, companies can achieve considerable cost savings. Furthermore, the simplified design and installation process mean that less specialized training is required, thus allowing for a wider range of personnel to perform maintenance tasks efficiently.
In summary, cassette oil seals offer a robust, reliable, and efficient solution for demanding industrial applications. Their expertly engineered design addresses both performance and operational challenges, cementing their status as an authoritative choice in the realm of sealing technology. Through continuous innovation and adherence to high-quality standards, cassette oil seals not only safeguard machinery but also enhance operational efficiency, delivering substantial economic and functional benefits across various industries.