Navigating the world of oil pump seals can be complex, yet understanding their functionality and significance is paramount for any professional in the hydraulic or automotive industry. At the core, oil pump seals play a crucial role in maintaining the efficiency and longevity of machinery by preventing leakages and ensuring smooth operation.
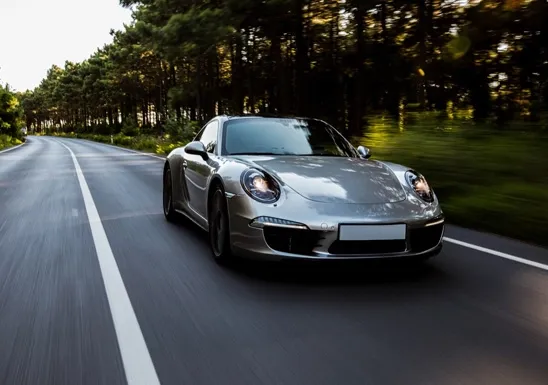
To truly grasp the importance of oil pump seals, it's essential first to understand their purpose. These seals are designed to keep oil contained within a system, avoiding any leakage that could lead to inefficiencies or costly failures. They act as a barrier, preventing contaminants from entering the pump, which could cause abrasive wear or corrosion, ultimately compromising the performance and lifespan of the equipment.
Various types of oil pump seals exist, each designed to suit different applications. For example, dynamic seals are used in situations where there is movement between the parts that the seal interfaces with. Static seals, on the other hand, are used where no relative motion between the surfaces exists. Factors like temperature range, pressure levels, and the type of fluid being pumped influence the selection of the seal material—ranging from rubber and silicone to more advanced materials like PTFE (Teflon) and Viton.
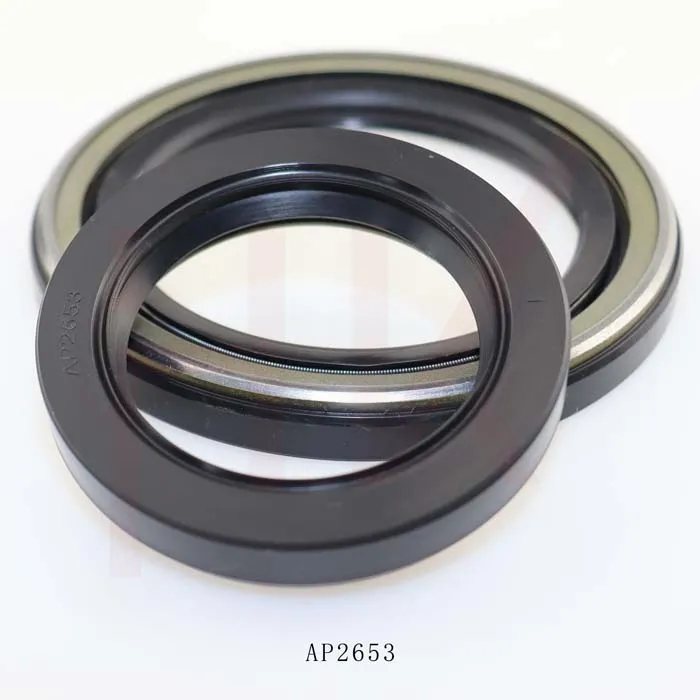
One key aspect of selecting the right oil pump seal is understanding the specific environmental factors the seal will be exposed to. High temperatures, intense pressure, and exposure to aggressive chemicals can all affect the seal's performance.
Choosing a seal material that withstands these conditions is critical. For instance, Viton seals are known for their exceptional heat resistance and chemical stability, making them ideal for automotive and industrial applications where these factors are prevalent.
oil pump seal
In terms of installation and maintenance, ensuring the longevity of oil pump seals necessitates careful attention to detail. During installation, it's vital to avoid any damage or stretching beyond what the seal can handle, which could lead to an improper fit. Regular maintenance checks are equally crucial, as they can identify early signs of wear and tear, such as hardening or cracking, which might cause the seal to fail prematurely. Replacing seals at scheduled maintenance intervals, instead of waiting until failure, can safeguard machinery operation and prevent unscheduled downtimes.
In a professional setting, the expertise in choosing and handling oil pump seals can elevate both the efficiency and reliability of operations. An understanding of different seal characteristics and an ability to troubleshoot seal failures are skills that enhance one’s authority within the field. Moreover, staying abreast of advancements in seal technology, such as developments in high-performance materials or innovative design improvements, contributes heavily to maintaining a competitive edge.
Trustworthiness in the realm of oil pump seals comes from both proven product performance and the reliability of information sources. When selecting seals for specific applications, utilizing suppliers known for integrity and quality guarantees that the products meet functional expectations and industry standards. Additionally, establishing partnerships with reputable seal manufacturers can provide valuable insights and support, ensuring the best sealing solutions for any given application.
In essence, oil pump seals, though seemingly small components, have a massive impact on the operational success of mechanical systems. For those in the field, possessing both a comprehensive understanding of the seal options available and the ability to apply this knowledge effectively is invaluable. The continuous pursuit of excellence in this area not only fortifies machinery performance but also reaffirms one's authority and reliability in today's competitive marketplace.