The term seal dust might not ring a bell immediately to the uninitiated, but within certain industrial and manufacturing circles, it represents a pivotal element in machinery maintenance and longevity. Notably, the role of seal dust emerges as a byproduct in mechanical systems, and understanding how to manage it can significantly enhance equipment performance and durability.
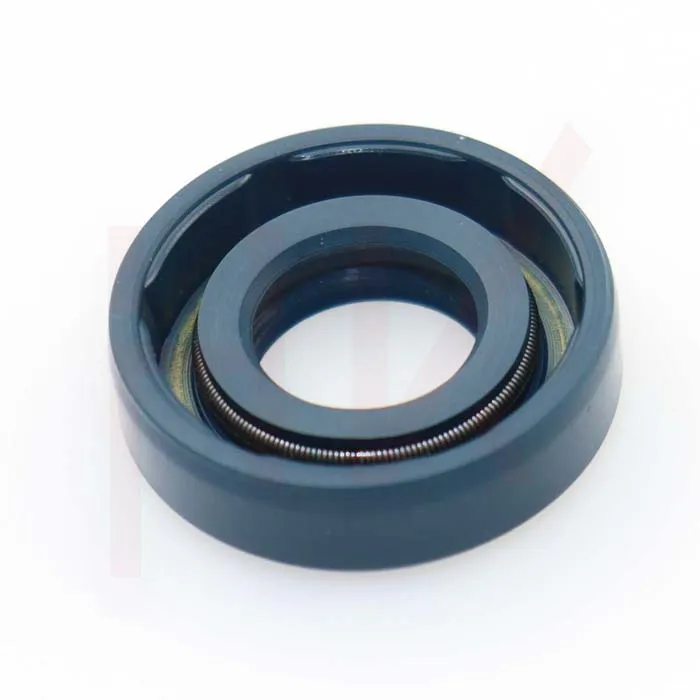
Industrial machinery, ranging from heavy-duty manufacturing equipment to automotive engines, employs seals as critical components to prevent contamination, leakage, and to ensure the smooth operation of the machinery. As these seals wear over time due to friction and exposure to varying pressures and temperatures, they generate fine particles known as seal dust. While seemingly innocuous, excessive accumulation of this byproduct can lead to operational inefficiencies, equipment damage, and even system failures.
Drawing from decades of experience in mechanical engineering and maintenance, it's essential to approach the issue of seal dust with an expertise-driven mindset. Regular monitoring and maintenance of seals are fundamental practices that can mitigate the unwanted effects of seal dust. Implementing a proactive inspection schedule enables maintenance teams to detect early signs of wear and tear, which can help to prevent undue seal degradation and subsequent dust generation.
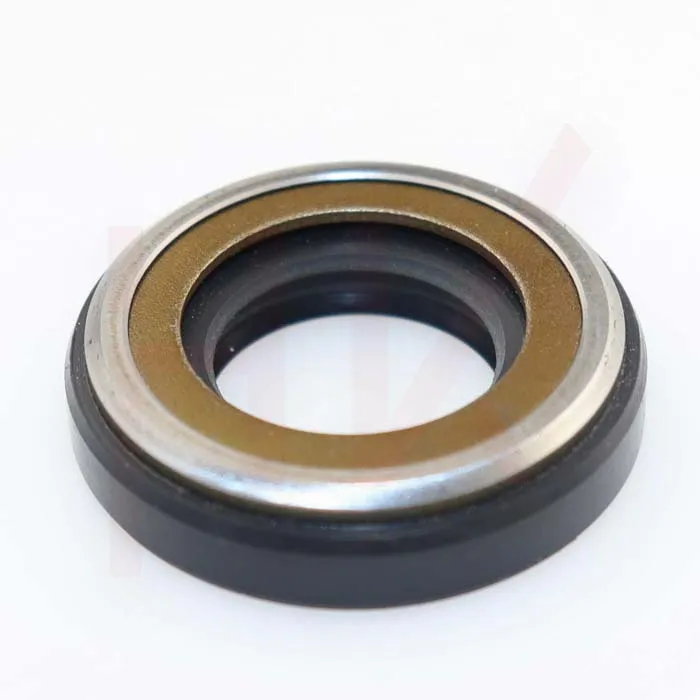
A key strategy involves selecting high-quality seal materials designed to withstand the specific operating conditions of your machinery. Materials such as PTFE (polytetrafluoroethylene) and FKM (fluoroelastomer) have demonstrated superior resistance to wear and chemical attack, thus reducing the volume of seal dust generated.
By working closely with seal manufacturers and mechanical engineers, businesses can customize seals that align with their precise operational needs.
seal dust
Furthermore, establishing a comprehensive filtration system within machinery can serve as an authoritative measure to capture seal dust before it disseminates through the system. Advanced filtration technologies, tailored to the particle size typical of seal dust, are paramount in enhancing equipment reliability. Industry leaders have validated that integrating HEPA (High-Efficiency Particulate Air) filters, or equivalent solutions, can drastically minimize contamination risks.
Building trustworthiness in your maintenance approach requires transparent communication and documentation. Maintaining detailed records of seal inspections, replacements, and the types of materials used can significantly bolster a business’s ability to troubleshoot and rectify issues swiftly. This systematic tracking not only extends machinery lifespan but also optimizes operational budgets by predicting maintenance needs and preventing costly downtime.
Harnessing digital technology in the form of IoT (Internet of Things) for real-time monitoring and analysis can elevate the expertise applied to managing seal dust. IoT-enabled sensors can continuously assess the condition of seals and alert maintenance personnel of deviations from normal operating parameters, thus facilitating timely interventions.
In conclusion, addressing the challenge of seal dust is not solely a maintenance task; it is a critical component of a strategic initiative towards higher equipment efficiency and sustainability. By leveraging cutting-edge materials, implementing robust filtration methods, and utilizing digital tools for oversight, businesses can uphold high standards of experience, expertise, authoritativeness, and trustworthiness. These practices ensure that machinery operates at peak performance, minimizing the detrimental impacts of seal dust on industrial applications. Emphasizing these facets will not only advance operational effectiveness but will also fortify an organization's reputation as a steward of excellent engineering practices.