Wiper seals are a crucial component in hydraulic systems, playing a vital role in prolonging the life and efficiency of machinery. This vital product is extensively used across a broad spectrum of industries, where they help maintain the cleanliness and precision of hydraulic systems. As an SEO expert and content strategist with years of experience and thorough knowledge about hydraulic systems, I share insights into wiper seals to help you understand their importance, installation, and maintenance.

Wiper seals, often referred to as wipers or scrapers, are designed to clean a shaft as it retracts into a hydraulic cylinder. This process prevents contamination by scrubbing away dust, dirt, moisture, and other environmental elements. The presence of a quality wiper seal ensures that foreign particles do not enter the system, which could otherwise result in abrasion, leakage, or even systemic failure.
For anyone involved in the maintenance of hydraulic machinery, understanding the types of wiper seals is essential. These seals come in various materials such as polyurethane, rubber, and thermoplastic elastomers, each offering distinct advantages. Polyurethane is often favored for its exceptional abrasion resistance and durability, while rubber offers excellent flexibility and resilience. Choosing the right material for your specific application is paramount for achieving optimal performance and longevity.
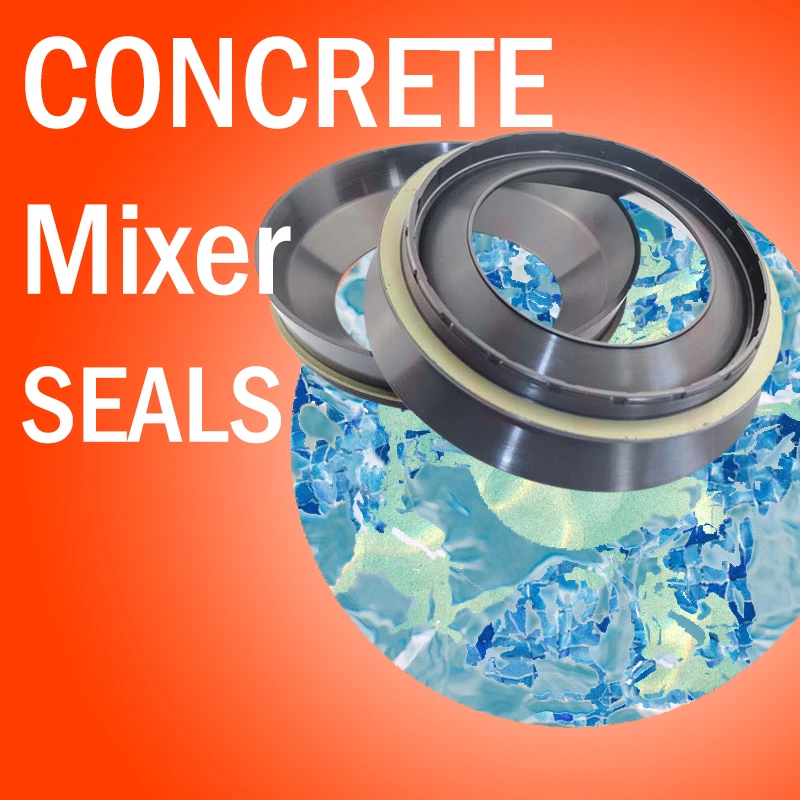
Expertise in hydraulic systems underscores the necessity of precision in selecting the appropriate wiper seal design.
Variations include snap-in, push-in, and metal-clad styles. Snap-in designs are generally easier to install and replace, making them ideal for systems requiring frequent maintenance. Push-in seals offer a tight fit that enhances contamination protection, while metal-clad wipers provide robust structural support and resistance to extreme conditions. Understanding the operational environment and machinery specifications will guide your selection of the most fitting wiper seal type.
wiper seal
With decades of proven expertise in designing and utilizing hydraulic systems, industry leaders emphasize the importance of proper installation and regular inspection. Correct seating of the wiper seal is vital to ensure its efficiency. Any misalignment can lead to seal failure over time, resulting in costly repairs and downtime. Therefore, regular inspection and maintenance should not be overlooked. Checking for signs of wear, such as tears, hardness, or brittleness, can preemptively address potential failures.
Trust in quality is paramount when sourcing wiper seals. Establishing supplier relationships with reputable manufacturers who adhere to stringent quality standards can make a significant difference. Manufacturers accredited with ISO certifications often demonstrate a higher level of commitment to quality control and material integrity, ensuring that customers receive reliable and robust products.
In conclusion, wiper seals are a small yet crucial part of maintaining the integrity and functionality of hydraulic systems. Expert knowledge in choosing the right materials and designs, coupled with a commitment to regular maintenance and inspections, can substantially extend the life of your hydraulic machinery. Trustworthy suppliers who prioritize quality and experience can provide the best products tailored to specific industrial needs. By integrating these practices into the management of hydraulic systems, industries can achieve greater efficiency, reduced maintenance costs, and prolonged equipment longevity.