In the world of industrial machinery, precision and efficiency are paramount. One key component that often goes unnoticed, yet plays an essential role in ensuring machinery performs optimally, is the skeleton oil seal. Renowned for its ability to enhance operational efficiency by preventing leaks, the skeleton oil seal is a silent guardian of machine longevity and reliability.
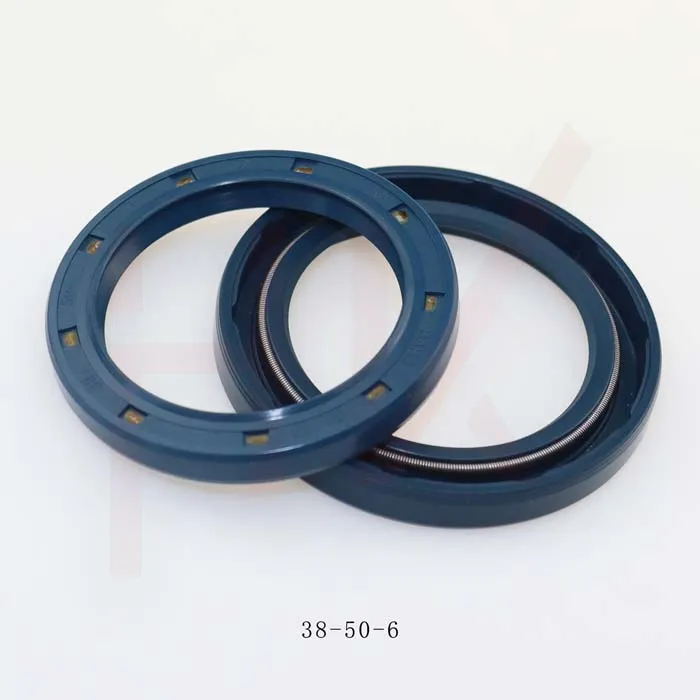
The skeleton oil seal, often referred to as a 'rotary shaft seal,' is an indispensable part of various mechanical systems. It serves the critical function of enclosing lubricants within systems and keeping external contaminants like dirt and moisture out. Its capability to avert leakages not only saves energy but also minimizes the risk of malfunction, thereby extending the life of the machinery.
The expertise in designing a skeleton oil seal involves a deep understanding of material science and engineering mechanics. The construction of an effective oil seal requires precision; it is typically crafted from high-quality materials like nitrile rubber, polyacrylate, and silicone, which possess excellent resistance to heat, wear, and chemicals.
This ensures that the seal can withstand the rigors of harsh working environments.

Professionals in the field of mechanical engineering underscore the importance of choosing the right type of oil seal for specific applications. For instance, nitrile rubber is often preferred for general-purpose applications due to its resilience and affordability. In contrast, for high-temperature applications, polyacrylate and silicone seals are recommended due to their superior thermal resistance. This nuanced understanding of materials and their properties attests to the expertise required in the selection and application of skeleton oil seals.
The reliability of a skeleton oil seal is also significantly influenced by its design. Dynamic seals, designed for rotating applications, feature precision-engineered lips that make consistent contact with the shaft. The resulting tight seal prevents lubricant from escaping while averting the entry of contaminants. Engineers meticulously design these seals using advanced computer modeling techniques to simulate conditions and optimize performance.
skeleton oil seal
Trust in the effectiveness of skeleton oil seals stems from rigorous testing and quality assurance standards. Manufacturers typically conduct extensive laboratory and field tests to ensure seals meet stringent criteria for durability, performance, and safety. This testing regime builds confidence in the seal's capability to perform under real-world conditions, fostering a sense of trust among users.
Industry leaders often rely on skeleton oil seals for critical applications in automotive, manufacturing, and heavy equipment sectors. The automotive industry, for instance, uses these seals extensively in engines and gearboxes where the prevention of oil leaks is crucial for engine efficiency and longevity. In manufacturing, skeleton oil seals help maintain the cleanliness and efficiency of machinery in production lines, contributing to consistent product quality.
To further establish authority in the use of skeleton oil seals, many manufacturers provide detailed technical support and resources to their clients. This includes installation guides, maintenance tips, and troubleshooting advice, ensuring that operators can fully benefit from the advanced features and longevity of their seals. Such comprehensive support underscores a commitment to customer satisfaction and establishes a robust relationship between manufacturers and users.
In conclusion, the skeleton oil seal is a testament to the intersection of engineering expertise and innovative design, playing a pivotal role in enhancing the operational efficiency of machinery across diverse industries. Through careful material selection, precision crafting, and robust testing, these seals ensure that equipment runs smoothly, ultimately delivering value and peace of mind to manufacturers and end-users alike.