Motor seals are a crucial component in ensuring the longevity and efficiency of motor systems across various applications. Understanding their role, types, and selection criteria can greatly enhance performance and reliability, making them indispensable in multiple industrial sectors.
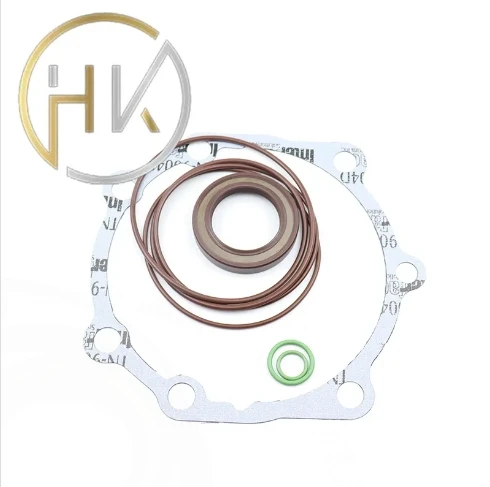
Motor seals serve primarily to prevent leakage of fluids between different components of a motor. Such leakage, if unchecked, can lead to diminished performance, increased wear and tear, and even failure of the motor. In environments where contamination from dirt or moisture is a concern, seals act as protective barriers, safeguarding internal components.
There are several types of motor seals, each designed for specific applications. Common types include rotary seals,
labyrinth seals, mechanical seals, and lip seals. Rotary seals are often used in applications where the motor's moving parts rotate, providing a tight barrier in dynamic environments. Labyrinth seals, on the other hand, are non-contacting seals that offer excellent high-speed performance by using a narrow, tortuous path to block leakage.
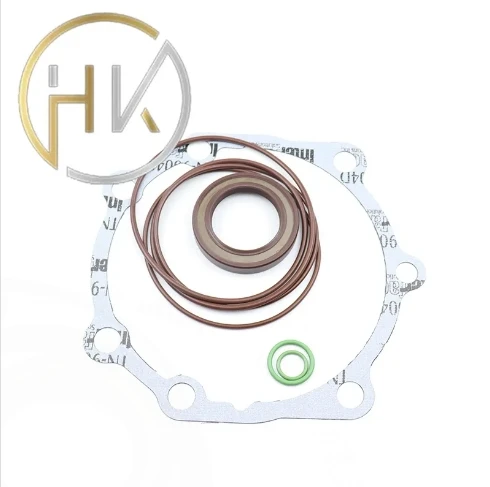
Choosing the right motor seal is crucial for optimal performance. The selection process should consider factors such as operational environment, temperature, pressure, and the nature of the fluids to be sealed. For instance, in high-temperature applications, seals made of materials like PTFE or other high-performance elastomers are preferable due to their heat resistance. Pressure differentials are another critical factor; seals should be able to withstand the pressure without deforming or breaking down.
Material selection is not purely about tolerances and compatibility. It also influences the sustainability and lifecycle costs associated with maintenance and replacement. For example, seals made from advanced composite materials can significantly extend service intervals and reduce maintenance costs, though their initial cost might be higher than standard options.
motor seal
Installation and maintenance play a vital role in the lifespan of motor seals. Even the best-designed seals can fail if improperly installed or maintained. Proper alignment, cleanliness of the mating surfaces, and correct lubrication are essential to prevent premature wear or damage. Additionally, regular inspections can catch signs of deteriorating seals, such as visible wear, leaks, or unusual noises, allowing for proactive maintenance before more severe issues arise.
There is a growing trend towards integrating smart technology with traditional motor systems. Smart seals equipped with sensors can relay real-time data on parameters such as temperature, pressure, and seal integrity to centralized systems. This pioneering approach not only enhances the reliability of the motor systems but also aligns with modern predictive maintenance practices, potentially reducing downtime significantly.
When considering motor seals, it's important to rely on authoritative sources and industry experts for guidance. Engaging with established manufacturers or consulting with engineers who specialize in sealing technologies can provide valuable insights into the most effective solutions for specific applications. They can offer customized seal designs that cater to unique operational requirements, improving both efficiency and durability.
In summary, motor seals are fundamental to the reliable operation of motor systems. Their correct selection, installation, and maintenance are paramount to ensuring efficiency and extending the life of the motor. By focusing on quality materials, incorporating smart technology, and leveraging expert advice, businesses can ensure that their motor systems are not only effective but also future-proof.