The shaft oil seal, also known as a rotary seal or lip seal, is a crucial component in mechanical systems that call for the containment of lubricants within rotating equipment. Its design and functionality have undergone significant innovations, making the shaft oil seal an indispensable tool in ensuring the longevity and efficiency of various industrial applications.
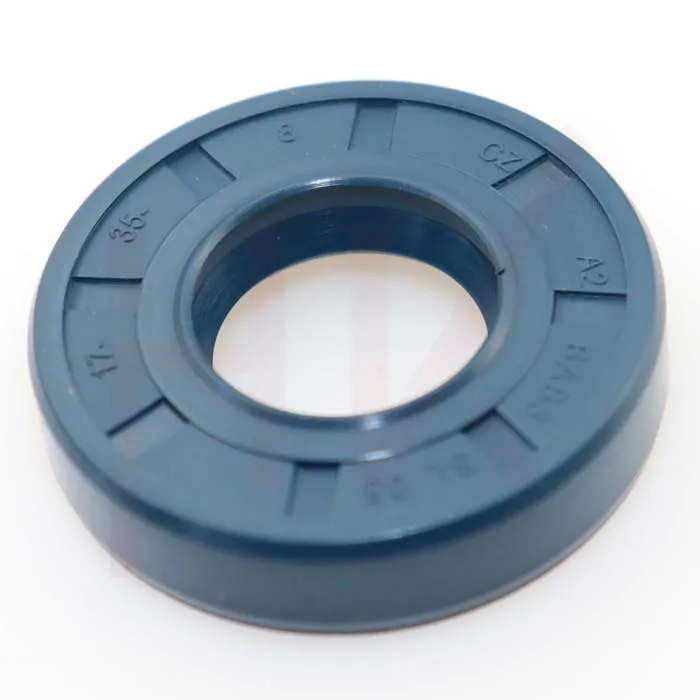
Drawing from years of expertise in mechanical engineering and lubrication technology, it's clear that the effectiveness of a shaft oil seal is underpinned by its ability to prevent leakage while minimizing friction. The critical function of these seals extends beyond simple containment; they are tasked with maintaining the precise alignment of components and the efficient operation of machinery. This complexity underscores the importance of selecting the right seal for specific applications, whether it be automotive, aerospace, or heavy machinery industries.
The material composition of the shaft oil seal often dictates its performance and durability. High-quality seals typically feature advanced materials such as fluorocarbon, silicone, or PTFE, each chosen for their unique properties in resisting chemical degradation and temperature extremes. For instance, PTFE seals are favored in high-temperature environments due to their excellent thermal stability, while silicone seals offer superior flexibility across a broader range of temperatures.
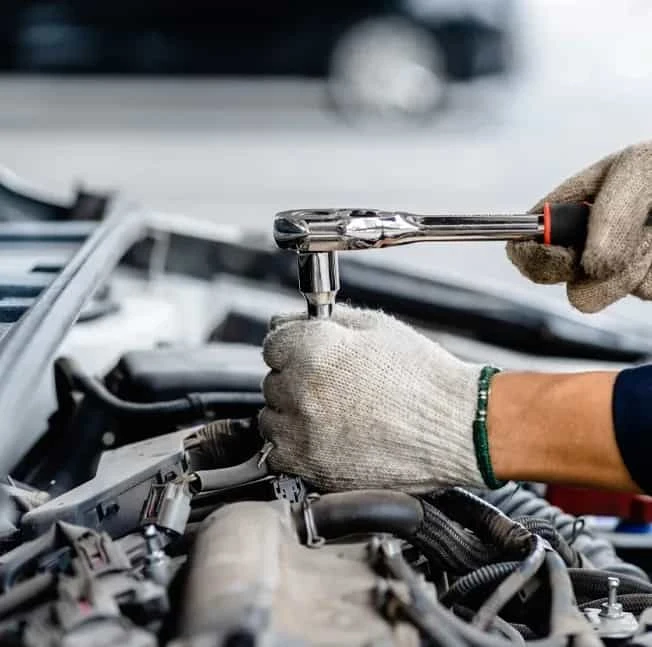
Installation of the shaft oil seal is a skill that combines precision and expertise. Incorrect installation can lead to premature wear and failure,
negating the seal's benefits. It is essential that installation is executed with meticulous attention to cleanliness and alignment, minimizing the risk of introducing contaminants into the system that can abrade the sealing lip and compromise its integrity.
Innovation in shaft oil seals frequently involves the development of enhanced lip designs. A dual lip configuration can offer improved protection against environmental ingress and retention of lubricants, while multi-spring designs ensure consistent pressure against the shaft, enhancing the seal's efficacy even in fluctuating conditions.
shaft oil seal
Maintaining trustworthiness and authoritative performance, leading manufacturers conduct rigorous testing of shaft oil seals to meet industry standards. Performance trials often simulate extreme operating conditions to verify the seal's capability to withstand pressure differentials, rotary speed variances, and temperature fluctuations. Such rigorous testing protocols ensure that the shaft oil seals on the market today will meet the durability and reliability needs of their intended applications.
Sustainability is increasingly influencing the production and selection of shaft oil seals. Manufacturers are now focusing on reducing the environmental impact of seal materials and production processes. Environmentally conscious initiatives, including recycling programs for used seals and the development of bio-based materials, are becoming more prevalent, responding to the growing demand for sustainable industrial practices.
Expertise in the domain of shaft oil seals plays a vital role in optimizing machinery performance. By choosing a seal with a design tailored to specific operational environments, businesses can extend the lifespan of their equipment while reducing the maintenance frequency and associated costs. This decision-making process underscores the need for close collaboration between users and manufacturers, ensuring that the knowledge surrounding seal selection and maintenance is leveraged for optimal performance and efficiency.
The evolution of shaft oil seals continues to be driven by technological advancements and industry demands. As innovations emerge, the imperative to stay informed about the latest developments in seal technology remains a priority for engineers and maintenance professionals. Keeping abreast of these changes can lead to more strategic decisions that enhance equipment longevity and operational efficiency, further solidifying the shaft oil seal's role as a cornerstone component in mechanical engineering.