Oil seals, often overlooked, play a crucial role in machinery and automotive applications, enhancing operational efficiency and longevity. Engineered from advanced elastomeric materials, oil seals serve as a barrier, preventing the leakage of lubricants and the infiltration of contaminants. Their importance cannot be understated in maintaining the integrity of engines and mechanical systems.
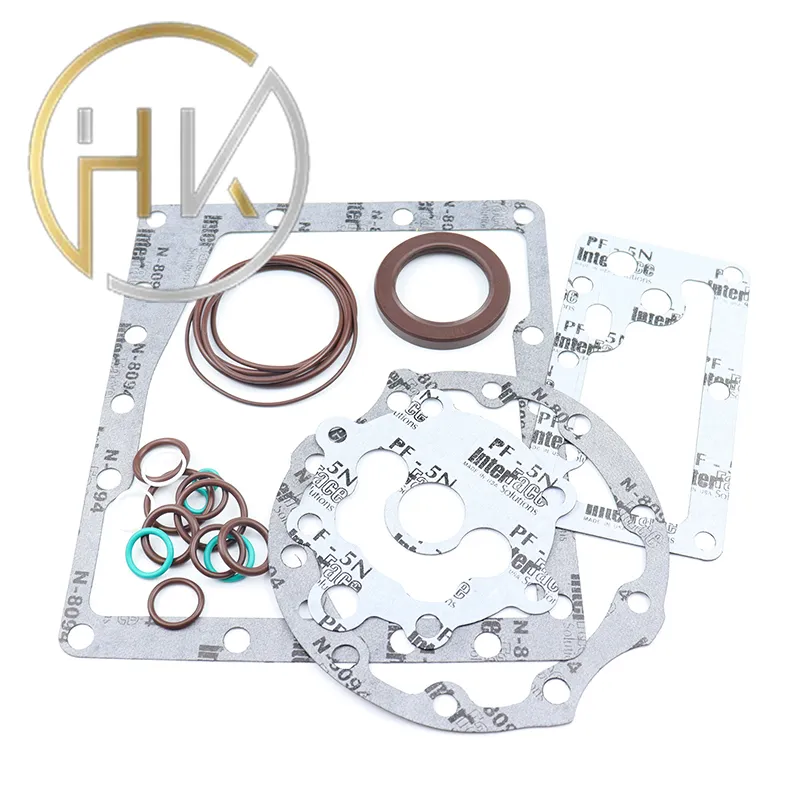
In real-world applications, oil seals are indispensable for the smooth operation of vehicles and industrial equipment. I recall an experience with an automotive client who faced recurrent engine failures. Upon inspection, the culprit was identified as a series of failed oil seals which allowed engine oil to seep out, compromising engine parts. With the installation of high-quality oil seals, the issue was resolved, showcasing the critical role these components play in operational reliability.
Specialists in the domain consistently emphasize the expertise required in selecting the appropriate oil seal for specific applications. The selection process considers factors such as temperature range, pressure levels, shaft speed, and chemical compatibility. A misstep in this process can lead to suboptimal performance or seal failure, underlining the necessity for professional expertise in the specification and installation of these seals.
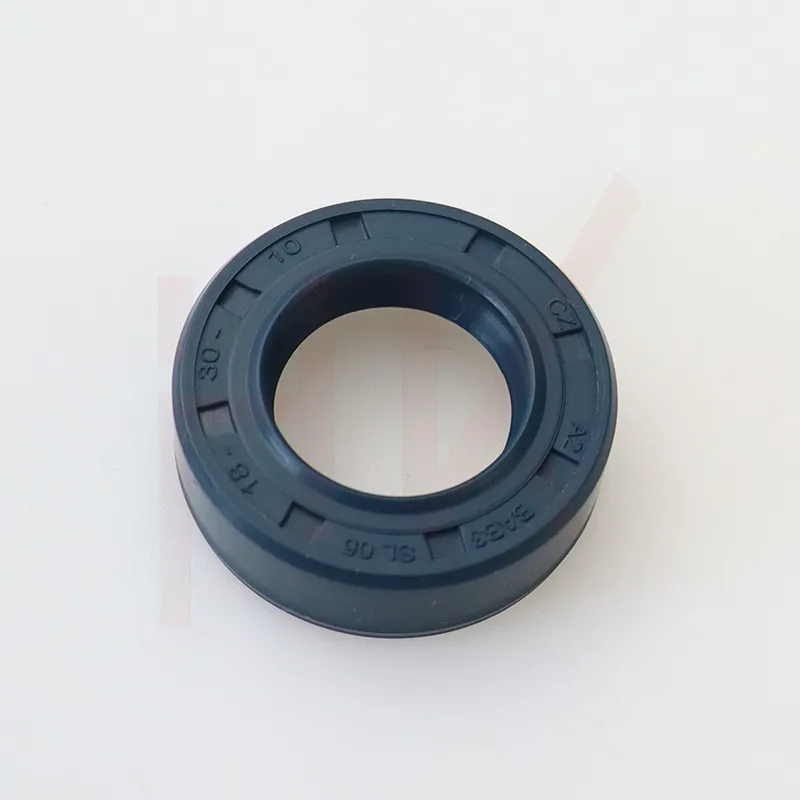
Authoritative sources within the industry, such as the Society of Automotive Engineers (SAE), have established guidelines and testing standards to ensure oil seal performance. These standards serve as a benchmark in manufacturing, guiding producers to develop seals that meet rigorous operational demands. Furthermore, advancements in material science have led to seals capable of withstanding extreme conditions, expanding their application in industries ranging from aerospace to heavy manufacturing.
oil seals
Trust in oil seal performance is reinforced by rigorous testing and adherence to manufacturing standards. Customers are rightfully assured that products conforming to industry standards will perform as expected. Additionally, many manufacturers provide extensive warranties and customer support, reinforcing the reliability of their products. Such commitments from industry leaders contribute significantly to the credibility of oil seals in the marketplace.
The evolution of oil seals continues as technology advances. Innovations such as self-lubricating seals and seals with integrated sensors for real-time monitoring are being explored. These technologies promise even greater efficiency and durability, allowing for proactive maintenance and reduced machinery downtime. As these innovations come to market, they will undoubtedly redefine standards and expectations regarding oil seal applications.
In conclusion, the significance of oil seals is evident in their diverse applications and the impacts they have on maintaining system integrity. The prowess of their design, backed by expertise and authoritative standards, ensures reliability and performance. As industry needs evolve, so too will the development of oil seals, promising continued dependability and enhanced operational outcomes across various sectors.