In the industrial sector, the application of hydraulic systems demands the utmost precision and reliability. At the heart of these systems, scraper seals play a pivotal role in ensuring efficient and smooth operation. Through years of meticulous study and practical engineering applications, scraper seals have emerged as essential components that safeguard hydraulic machinery from environmental contaminants while enhancing their longevity.
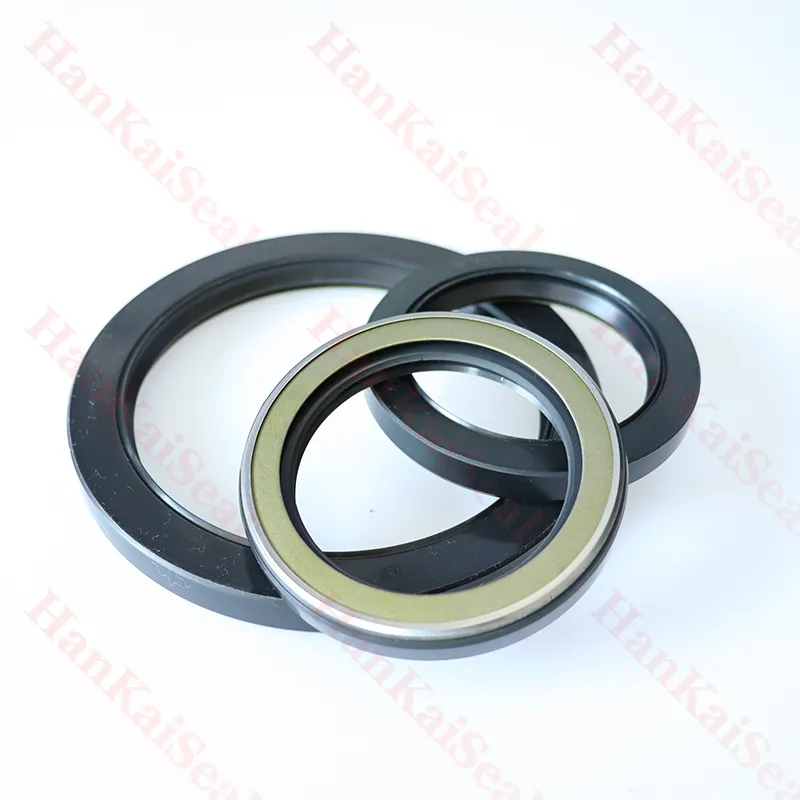
Scraper seals, often called wiper seals, are specifically designed to remove dirt, dust, and moisture from the piston rods of hydraulic cylinders as they retract. This protective function is crucial because contaminants can compromise the hydraulic fluid and internal components, leading to inefficiencies or complete system failures. The sophisticated design of scraper seals ensures that only clean and uncontaminated fluid remains within the system, preserving the integrity of the internal environment.
Expert practitioners within the field recognize that the choice of materials for scraper seals is fundamental to their performance. Common materials include polyurethane, nitrile rubber, or PTFE (polytetrafluoroethylene), each offering unique benefits. Polyurethane, for instance, is celebrated for its exceptional abrasive wear resistance, making it ideal for high-pressure environments. Nitrile rubber is favored for its resilience and cost-effectiveness, particularly in temperatures and fluid compatibility standards. PTFE, with its advanced chemical and thermal properties, provides unmatched performance in extreme conditions. Engineers must weigh these material properties carefully to align the choice of scraper seal with specific operational requirements.
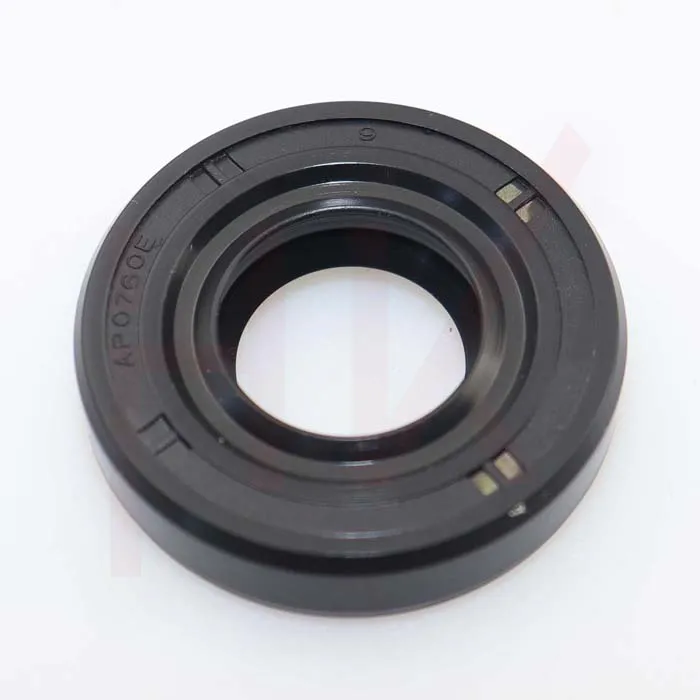
Precision manufacturing techniques are essential to crafting scraper seals that can withstand the demanding conditions of hydraulic systems. Modern advancements have introduced techniques such as computer-aided design (CAD) and precision molding, which ensure that scraper seals maintain tight tolerances and consistent quality. This precision is not only theoretical; it translates into practical benefits by minimizing leaks and prolonging the lifespan of hydraulic systems in real-world operational environments.
Moreover, ongoing innovations have led to the development of hybrid scraper seals. These advanced solutions marry the characteristics of different materials to optimize performance across various parameters such as temperature range, pressure endurance, and friction coefficient. For instance, a hybrid seal might combine the sturdy durability of polyurethane with the low friction of PTFE, offering a versatile solution capable of thriving in diverse hydraulic applications.
scraper seal hydraulic
Trusted suppliers in the market have also prioritized stringent quality control processes. By implementing rigorous testing protocols, they ensure that each seal meets the highest industry standards before reaching consumers. These protocols often include testing for thermal resistance, pressure thresholds, and durability under cyclic loading conditions, establishing a benchmark for reliability that customers can depend on.
As hydraulic systems evolve, scraper seals continue to advance in line with technological innovations. Industry research and development are at the forefront of exploring new materials and engineering methodologies to push the boundaries of what these seals can achieve. Nanotechnology, for example, is being investigated as a means to enhance the surface properties of scraper seals, potentially elevating their resistance to wear and their operational lifespan significantly.
Engagement with academic institutions and professional organizations has also been a cornerstone of developing expertise in scraper seal technology. Collaboration with these bodies fosters an exchange of cutting-edge research findings and industry best practices, ensuring that the knowledge ecosystem surrounding hydraulic scraper seals remains vibrant and forward-looking.
In the realm of customer engagement, companies are adopting a consultative approach. Recognizing the complexities involved in hydraulic systems, manufacturers often provide detailed guidance and technical support to help clients select the right scraper seals for their specific needs. By focusing on customer education and transparent communication, these companies build trust and establish themselves as authoritative figures in the industry.
In summary,
scraper seals are indispensable in hydraulic systems, where accuracy and resilience are paramount. Through robust design, innovative material use, and strict quality standards, these components ensure that hydraulic machinery runs smoothly and efficiently. By remaining at the cutting edge of technology and championing a culture of trust and expertise, the industry continues to deliver scraper seals that meet and exceed the demands of modern engineering applications.