The evolution of machinery and advanced engineering has brought sophisticated components like rotary shaft oil seals to the forefront, demanding attention for their crucial role in maintaining the integrity and efficiency of mechanical systems. With decades of experience in the industry, one realizes that selecting the right oil seal is fundamental, yet often underestimated. But why has this tiny component gained such importance?
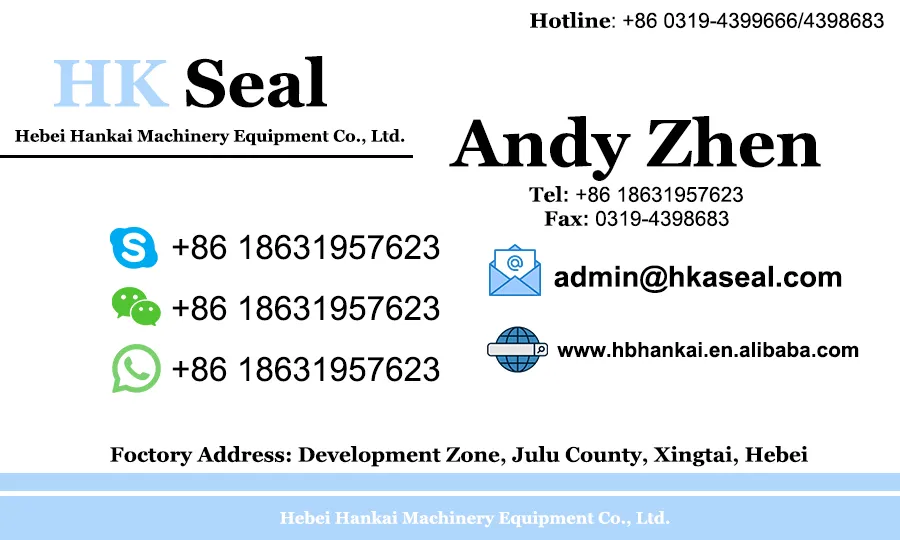
Experience has shown that rotary shaft oil seals serve as guardians of lubrication, preventing leakage and contamination in various mechanical assemblies. These seals are indispensable in a plethora of applications, ranging from automotive engines to industrial machinery. Their ability to retain lubricants and exclude contaminants ensures prolonged equipment life and enhances performance. In real-world scenarios, the absence of an effective seal can lead to catastrophic failures, incurring significant downtime and repair costs.
Expertise in the design and application of rotary shaft oil seals allows for customization to meet specific operational needs. Factors like shaft speed, temperature range, pressure conditions, and chemical compatibility are meticulously considered when selecting an oil seal. Advanced materials such as nitrile, fluoroelastomer, and PTFE are often chosen for their specific advantages in resistance to heat, chemicals, or wear, underpinning the seal’s performance in challenging environments.

Authoritativeness in this domain comes from a deep understanding of both the mechanical systems and the critical role these seals play.
Leading manufacturers continue to invest in research and development to innovate better sealing solutions. Patented technologies and proprietary materials emerge as a testament to their commitment to pushing the boundaries of what rotary shaft oil seals can achieve. Engineers and product designers are encouraged to collaborate closely with experts and leverage cutting-edge sealing technologies to optimize their machinery designs.
Trustworthiness in rotary shaft oil seals is validated through rigorous testing and quality assurance practices. Reputable companies conduct extensive laboratory tests, including endurance testing, leakage assessments, and compatibility analysis to ensure the reliability of their seals under varying conditions. Certifications from recognized bodies further bolster the assurance that these components are engineered to meet stringent standards, emphasizing their dependability.
rotary shaft oil seals
Moreover, sustainability has become a focal point in the production of rotary shaft oil seals. Environmentally responsible manufacturing processes, coupled with materials that reduce waste and improve energy efficiency, are now becoming industry staples. This shift not only aligns with global ecological goals but also resonates with customers who are increasingly mindful of their environmental footprint.
Real-world application success stories echo the importance of choosing the right rotary shaft oil seals. For instance, in the automotive sector, selecting an optimal seal can result in significant improvements in fuel efficiency and emissions control, while in heavy machinery, a well-designed seal can drastically reduce maintenance needs and extend operational uptime.
For businesses, understanding these nuances and prioritizing high-quality rotary shaft oil seals is an investment in operational efficiency and longevity. Collaboration with trusted suppliers who provide comprehensive support, from product selection to installation guidance, can significantly impact overall performance.
In conclusion, rotary shaft oil seals, while small, embody a critical intersection of engineering prowess and material science. They serve as a linchpin in mechanical systems, ensuring reliability, efficiency, and longevity. As industries evolve, so too does the need for advanced sealing solutions, reinforcing the importance of experience, expertise, authoritativeness, and trustworthiness in the selection and application of these essential components.