Metric shaft seals play a crucial role in maintaining the efficiency and safety of machinery across various industries. These seals prevent the ingress of contaminants and the egress of lubricants, thereby extending the life of bearings and reducing maintenance costs. They are particularly essential in sectors such as automotive, aerospace, marine, and manufacturing, where the precision and reliability of machines are paramount.
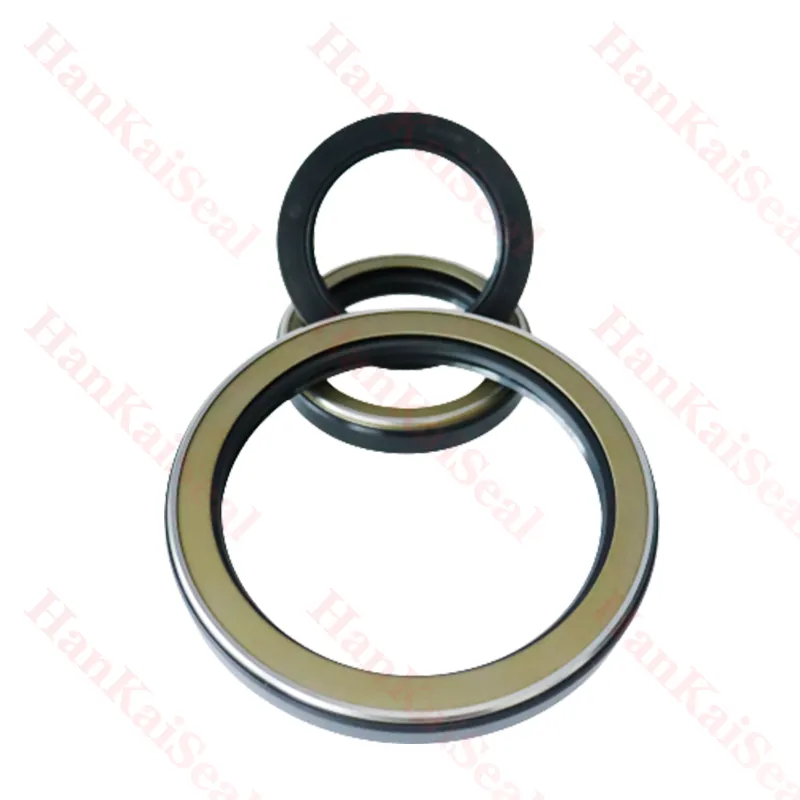
The design of metric shaft seals is tailored to meet international standards, ensuring compatibility and interchangeability with equipment produced globally. This is essential for companies operating in multiple countries, as it simplifies logistics and maintenance procedures. High-quality seals are usually manufactured from durable materials such as nitrile rubber, fluorocarbon, and polytetrafluoroethylene (PTFE), each offering unique advantages depending on the specific operating conditions. Nitrile rubber, for example, is highly resistant to oil and fuels, making it ideal for automotive applications, whereas fluorocarbon is suitable for high temperature and chemically aggressive environments.
In terms of installation, it is vital to ensure that the shaft and housing are clean and free from burrs or rough edges that could damage the seal. Proper alignment during installation cannot be overstated, as misalignment can lead to premature failure of the seal. Additionally, consideration must be given to the operating speed and pressure conditions, as these factors directly affect the seal’s performance and lifespan.
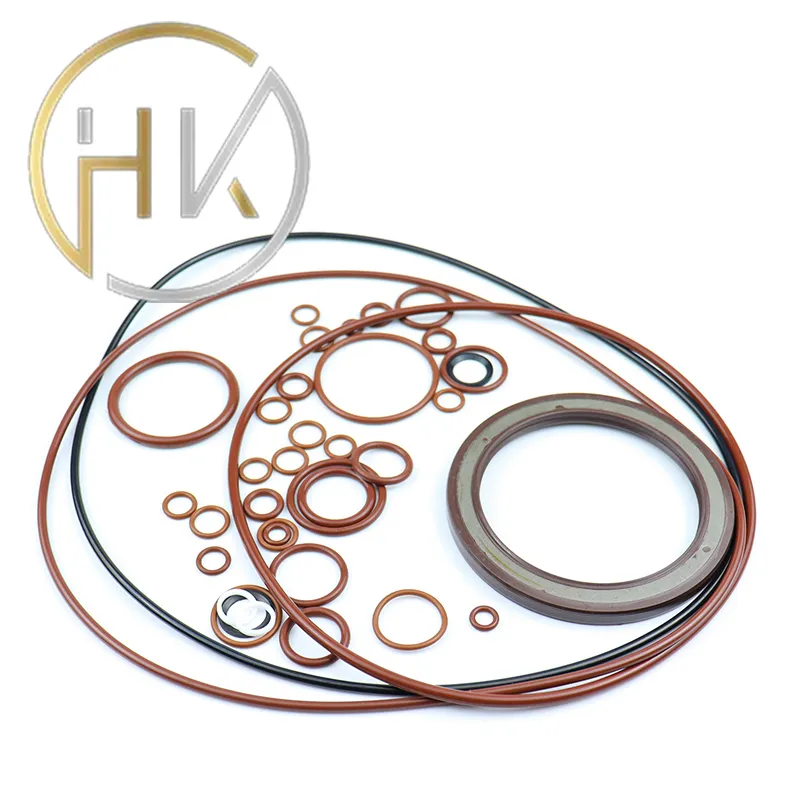
The expertise required to select the appropriate metric shaft seal is significant, and engineers often rely on detailed performance data and manufacturer recommendations. This is why partnerships with reputable seal manufacturers and suppliers can be invaluable. Companies like SKF, Freudenberg Sealing Technologies, and Trelleborg Sealing Solutions are renowned for their rigorous testing and quality control processes, ensuring that their products meet the highest standards of performance and reliability.
metric shaft seals
One real-world example of successful metric shaft seal application is in the energy sector, specifically in wind turbines. These turbines operate in harsh environments, where seals are critical for protecting the gearbox and generator from dust, moisture, and salt. By implementing robust sealing systems, operators have significantly reduced downtime and maintenance costs while increasing the turbines’ operational efficiency.
Furthermore,
innovation in seal technology continues to evolve. Advanced designs now incorporate features like hydrodynamic aids, which improve sealing performance by redirecting fluid films, thereby extending the seal's operational life. Emerging materials and coatings are also being developed to enhance temperature resistance and friction characteristics, reflecting the industry’s commitment to continuous improvement.
To ensure the effectiveness of metric shaft seals, ongoing monitoring and maintenance are essential. Periodic inspections, including checking for leaks and wear, help in preemptively addressing potential issues. Trust in the performance of these seals is built on the foundation of strong technical knowledge, quality materials, and collaboration with trusted manufacturers. Thus, investing in high-quality metric shaft seals is not just a necessity for operational success but also a strategic decision that can influence a company's competitiveness and market positioning.