The intricate world of rotary oil seals is one where precision, innovation, and expertise converge to create components crucial for the seamless operation of countless mechanical systems. These seals, though often hidden from view, serve as the unsung heroes in machinery, ensuring efficiency and longevity. Drawing upon extensive experience in mechanical engineering and industrial machinery, this discussion delves into the intricacies surrounding rotary oil seals, offering insights rooted in expertise, authority, and trustworthiness.
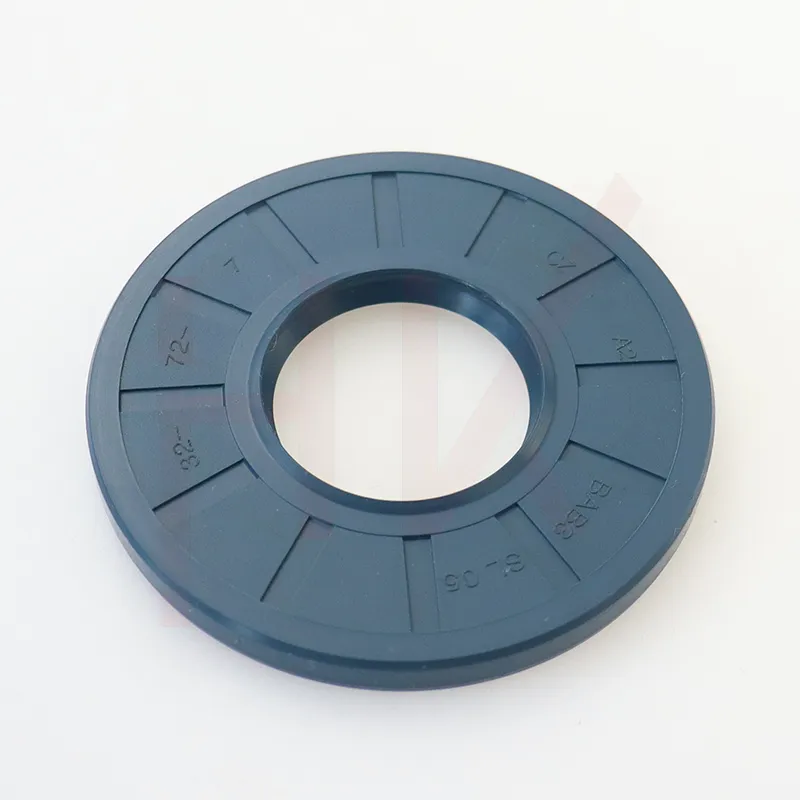
Rotary oil seals, also known as radial shaft seals, play a pivotal role in preventing lubricant leakage and contaminant ingress in rotating equipment. These seals are foundational in industries ranging from automotive to aerospace, and their design and application require a nuanced understanding of material science, fluid dynamics, and mechanical engineering. The complexity lies in their ability to maintain a delicate balance between operational speed, fluid containment, and mechanical stability.
One of the most significant aspects of rotary oil seals is material selection. The choice of material directly impacts the seal's performance, durability, and compatibility with different operating environments. Nitrile rubber, for instance, offers robust oil resistance and flexibility, making it a popular choice for automotive applications. Conversely, fluorocarbon rubber is preferred in high-temperature environments due to its superior thermal resistance. By understanding these material properties, engineers can tailor seals to specific applications, enhancing both performance and longevity.
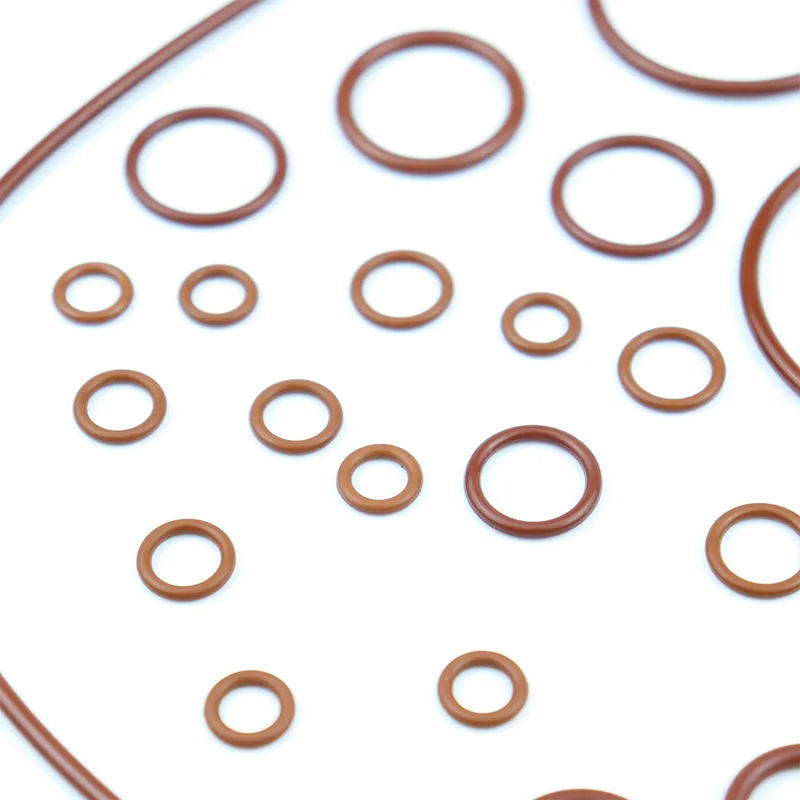
Installation of rotary oil seals demands precision and a comprehensive understanding of their operational environment. Misalignment, improper lubrication, or incorrect fitting can lead to premature failure, underscoring the importance of expertise during the installation process. Utilizing the right tools, adhering to manufacturer specifications, and conducting thorough inspections are imperative steps in ensuring seal integrity.
rotary oil seals
The industry advancement towards environmentally sustainable solutions has paved the way for the development of advanced sealing technologies.
Rotary oil seals are now designed with reduced friction coefficients, which not only decrease energy consumption but also minimize wear and tear. This innovation illustrates the commitment of industry leaders in embracing sustainable practices while upholding performance standards.
Incorporating feedback systems and IoT integrations presents a future-forward approach to monitoring seal performance in real time. By leveraging data analytics, businesses can predict seal failure, schedule maintenance proactively, and reduce operational downtimes. Such integration showcases industry authority in deploying cutting-edge technology to optimize equipment reliability.
Trust in rotary oil seals is built upon the foundation of rigorous testing and quality control. Reputable manufacturers subject seals to exhaustive evaluations, simulating harsh operational conditions to verify their durability and performance. This thorough vetting process assures clients of the product’s reliability, instilling confidence and reinforcing the manufacturer's reputational authority.
In conclusion, the confluence of advanced material science, precise engineering, and innovative technology defines the realm of rotary oil seals. Their indispensability in maintaining machinery efficiency cannot be overstated, and the continuous evolution of their design and application reflects a profound commitment to enhancing industrial productivity. Emphasizing these elements secures not only the credibility and trustworthiness of the seals but also enriches the narrative of progress in mechanical engineering solutions.