Rotary lip seals have become indispensable components in the machinery and automotive industries, where maintaining lubricity and preventing leakage are paramount. These versatile seals efficiently protect gears, bearings, and various other mechanical components, ensuring optimal operation and extending the lifespan of a wide array of equipment.
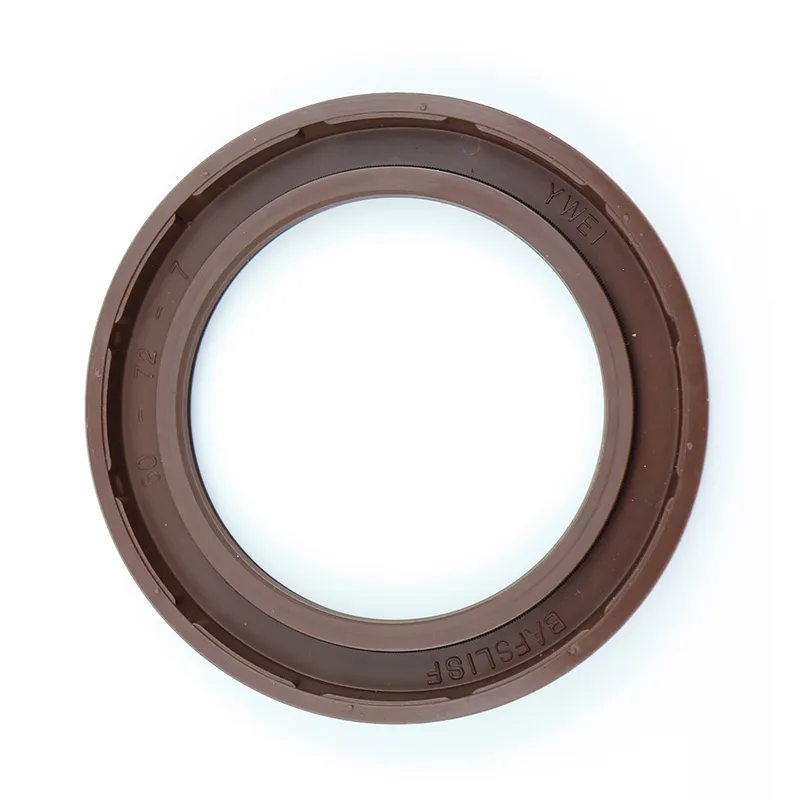
The inherent design of rotary lip seals consists of a flexible lip that remains in continuous contact with a rotating shaft. This seamless interaction prevents fluid leakage while simultaneously offering a protective barrier against environmental contaminants such as dirt, dust, and moisture. These seals are engineered from durable elastomers or rubber compounds, allowing them to withstand high temperatures, pressure variances, and aggressive chemicals, increasing their efficiency and reliability.
The undeniable expertise in the manufacturing of rotary lip seals is evident among leading manufacturers, who rely on precision engineering and extensive testing regimes to ensure their products meet stringent quality standards. These manufacturers have honed their craft over decades, resulting in seals that boast enhanced adhesion, superior wear resistance, and unprecedented thermal stability.
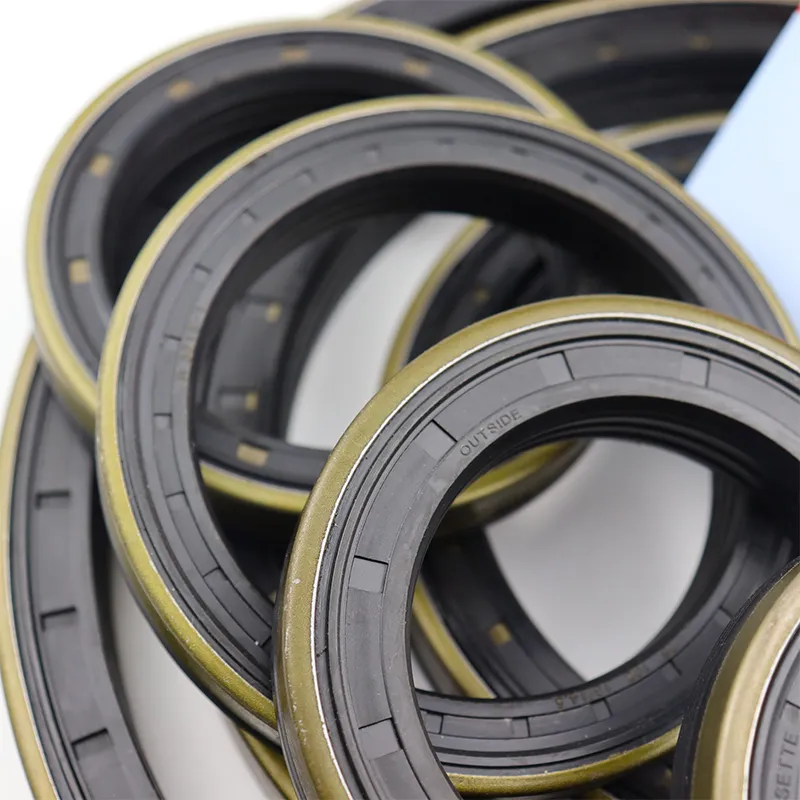
Professionals in the field widely recognize the importance of selecting the right material for rotary lip seals. Fluoroelastomer (FKM) is a preferred choice for applications involving high thermal stress, whereas nitrile rubber (NBR) offers excellent compatibility with petroleum-based oils and gasoline. For environments with extreme chemical exposure, polytetrafluoroethylene (PTFE) remains unmatched due to its exceptional chemical resistance.
Furthermore, installation expertise plays a critical role in the performance of rotary lip seals. Proper alignment and lubrication during installation are vital to minimize wear and tear, thereby ensuring the seal performs optimally throughout its lifespan. Experts caution against common installation errors, such as inadequate shaft surface finish or incorrect lip orientation, which can compromise seal integrity and lead to unexpected failures.
rotary lip seal
The authoritative stance on rotary lip seals is reinforced by their extensive application across numerous sectors. In the automotive industry, these seals are celebrated for their ability to maintain oil integrity in engines and transmissions. Meanwhile, in the industrial sector, they are indispensable in maintaining the efficiency of pumps, compressors, and gearboxes, where any lubrication failure could result in costly downtime and repairs.
Testing and quality assurance processes for rotary lip seals are rigorous, further emphasizing their trustworthiness. Leading manufacturers perform extensive simulations and empirical tests to predict seal behavior under various operational conditions, including pressure, temperature, and exposure to corrosive substances. This dedication to quality assurance instills confidence in these products' ability to perform reliably over extended periods.
When evaluating rotary lip seals for a specific application, discerning individuals consider several critical factors load conditions, shaft speed, environmental challenges, and compatibility with media types. An informed choice necessitates balancing these variables with the seal’s material properties to optimize performance and longevity.
Therefore, consultation with seasoned experts and thorough analysis remain integral to the selection process.
In embracing cutting-edge developments in seal technology, innovative designs such as dual-lip configurations and spring-loaded assembly have emerged, offering superior resilience and adaptability. These advancements underscore rotary lip seals' evolution, tailored for modern mechanical demands and engineered for peak performance.
In conclusion, rotary lip seals epitomize the fusion of experience, expertise, authoritativeness, and trustworthiness. Their widespread application and relentless innovation highlight their critical role in ensuring mechanical efficacy and reliability across diverse industries. With a thorough understanding of their material composition and application nuances, these unassuming components continue to safeguard mechanical systems, driving innovation and excellence in engineering practices worldwide.