Oil seals for rotating shafts are critical components in a diverse array of machinery, providing numerous benefits and ensuring the optimal functioning of mechanical systems. Understanding their role and significance can vastly enhance the maintenance and productivity of equipment, adding tangible value to both industrial and consumer applications.
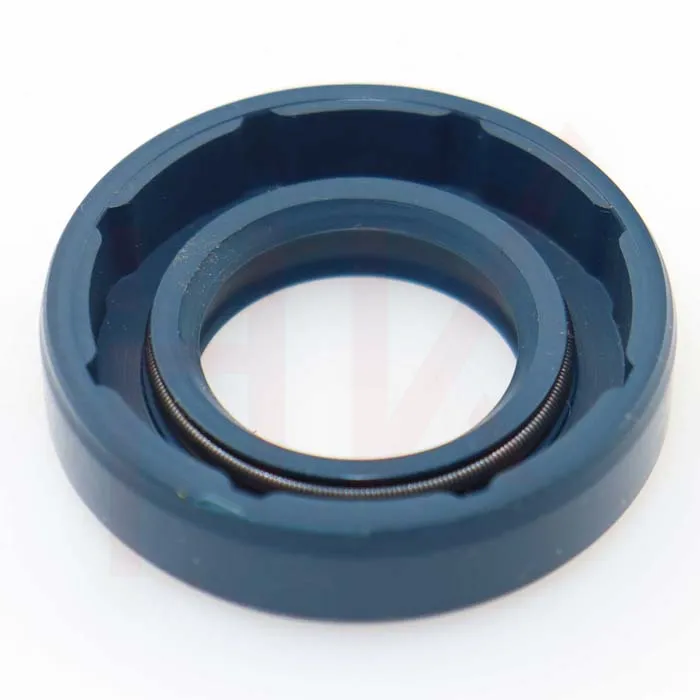
In industrial machinery, oil seals act as barriers, preventing leaks of lubricants and fluids, which are essential for the smooth operation of rotating shafts. Expertise in selecting the right oil seal involves evaluating the specific needs of the machinery, including speed, temperature, pressure, and chemical compatibility. High-quality seals reduce wear and tear on bearings, minimize contamination risks, and lower maintenance costs—a testament to their importance.
From an authority perspective, oil seals are recognized in mechanical engineering as pivotal in enhancing the lifespan of machinery. Their design must be precise; even the slightest imperfection can lead to catastrophic failure, causing downtime and potentially expensive repairs. The selection process often involves consultations with manufacturers or engineers who understand the intricate dynamics of the systems in play. Trusted brands in the market offer seals with certifications that authenticate their quality and reliability, ensuring peace of mind for engineers and operators alike.
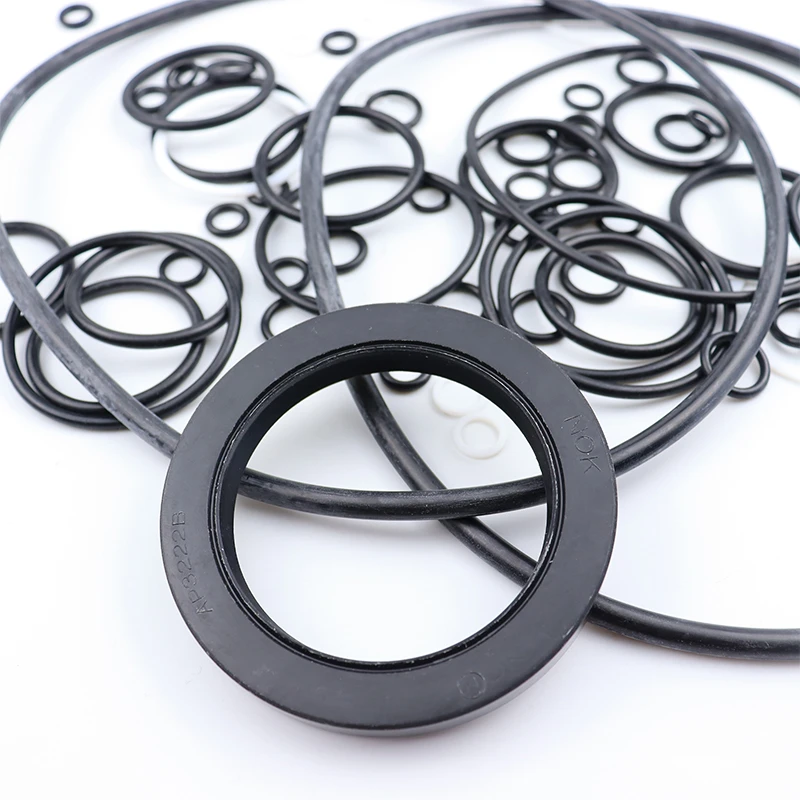
Trustworthiness of oil seals is enhanced by adherence to rigorous industry standards. Certifications such as ISO or API standards prove that a seal can withstand specific environments and stresses. Actual field experience shares valuable insights into how oil seals perform under different conditions. Testimonials and case studies reveal real-world scenarios where seals have effectively prolonged the functional life of machinery. Operators often report not having to replace seals as frequently, which translates to cost savings and increased operational efficiency.
oil seal for rotating shaft
The experience of using quality oil seals draws similarities across various sectors, from automotive to heavy machinery. In automotive applications, for instance, these seals prevent leakage of fluids in engines and axles, directly impacting vehicle performance. A faulty seal here can lead to gradual degradation of engine components, illustrating the necessity of investing in premium quality seals. Similarly, in heavy industries, where machinery operates under extreme conditions, oil seals are often a decisive factor between continuous operation and unexpected halts.
Additionally, innovation in oil seal materials and design continues to refine their effectiveness. Advanced materials like PTFE and FKM are used to combat chemical reactions and extreme temperatures, expanding the range of applications dramatically. Improved manufacturing technologies ensure seals have perfect symbiosis with the shafts they protect, minimizing friction and prolonging service life.
The cumulative knowledge gained from decades of mechanical engineering and practical experience with oil seals reveals a truth that transcends industry boundaries—choosing the right oil seal is as much a science as it is an art. Awareness of the nuanced complexities in seal selection and application empowers decision-makers to achieve greater efficiency and longevity in their machinery.
In conclusion,
oil seals for rotating shafts are fundamental components that serve as the unsung heroes in the world of machinery. Their ability to preserve system integrity, extend machinery lifespan, and improve operational performance cannot be overstated. Keeping up with advancements and industry best practices in seal technology equips stakeholders with the knowledge to make informed decisions, backed by experience, expertise, and trustworthiness. Whether for automotive, industrial, or any specialized machinery, investing in the right seal plays a pivotal role in enhancing overall mechanical resilience.