Selecting the right oil seal for a pump is crucial for ensuring the efficient performance and longevity of the equipment. Oil seals play an integral role in preventing leakage, maintaining proper lubrication, and protecting the pump from external contaminants. Understanding these components requires both industry insight and real-world application experience.
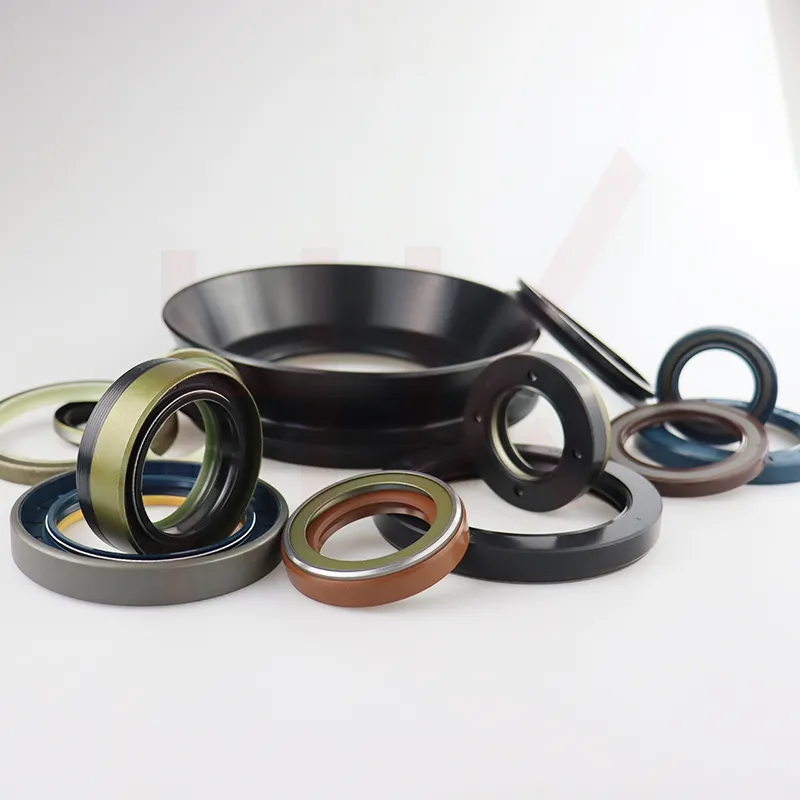
Oil seals for pumps aren't just a simple component in machinery but rather a sophisticated solution designed to handle high-stakes operational demands. Their importance lies in their ability to provide a barrier against the ingress of dirt and moisture, which can severely impact a pump's performance. By retaining lubricants within the pump system, oil seals help maintain the internal environment and reduce friction, ultimately leading to reduced wear and tear on the moving parts.
The expertise in choosing an appropriate oil seal involves detailed knowledge of the operational environment of the pump. For instance, an oil seal used in a pump operating under extreme temperatures needs to be made from materials that can withstand thermal expansion and contraction without losing integrity. Similarly, understanding the pressure conditions is vital since seals must resist pressure differentials that could cause seal failure and subsequent fluid leaks.

A vetted expert will preach the importance of the materials comprising the oil seal. Common materials include Nitrile Rubber (NBR), Viton, and Silicone, each with distinct properties. NBR is prized for its wear resistance and performance with moderate temperatures and pressures. In contrast, Viton is exceptional in high-temperature applications and offers superior chemical resistance. Silicone, however, is used in environments with extreme temperature variations but limited to moderate chemical exposure due to its reactivity.
The design of the oil seal also merits careful consideration. Lip seals, for instance, are engineered to accommodate both forward and reverse fluid pressure, making them versatile for various pump applications. The double lip design provides an additional layer of protection against contaminants, making it ideal for pumps operating in dusty conditions or in applications with significant external particulate matter.
oil seal for pump
Authoritativeness in the oil seal domain translates to understanding these pieces not just as isolated components but as integral to the entire pump system. Adept knowledge about how oil seals integrate with other system components can prevent operational setbacks. For example, incorrectly installed or mismatched seals can lead to energy inefficiencies, resulting in increased operational costs and equipment downtime.
Building trust in the realm of oil seals for pumps also involves real-world validation from those who have employed such components in their operations. Case studies reflect successful instances of oil seals extending pump life, minimizing downtime, and saving costs. For instance, an industrial application might showcase a switch to a higher-grade seal that led to twice the lifespan of its predecessor due to enhanced resistance to harsh chemicals.
Furthermore, maintaining a database of how seals perform across various industries—from automotive to petrochemical—enhances trust. Experience from cross-industry applications creates a comprehensive understanding of typical challenges and successful adaptations, promoting confidence in the expertise of professionals recommending these products.
To conclude, the effectiveness of an oil seal is not in its singular form or function. Rather, it is its tailor-fitted application to specific operational demands, the nuances of materials science, and meticulous selection based on environment-specific criteria that underscore its impact. By merging technical knowledge with practical insights, providers of oil seals for pumps can offer solutions that deliver reliability and superior performance, ensuring the seamless operation of pumps under varied industrial conditions. Through experience, expertise, authority, and trustworthiness, oil seals remain pivotal in safeguarding the efficiency and durability of essential pumping equipment.