Understanding the Integral Role of Oil Seals for Rotating Shafts
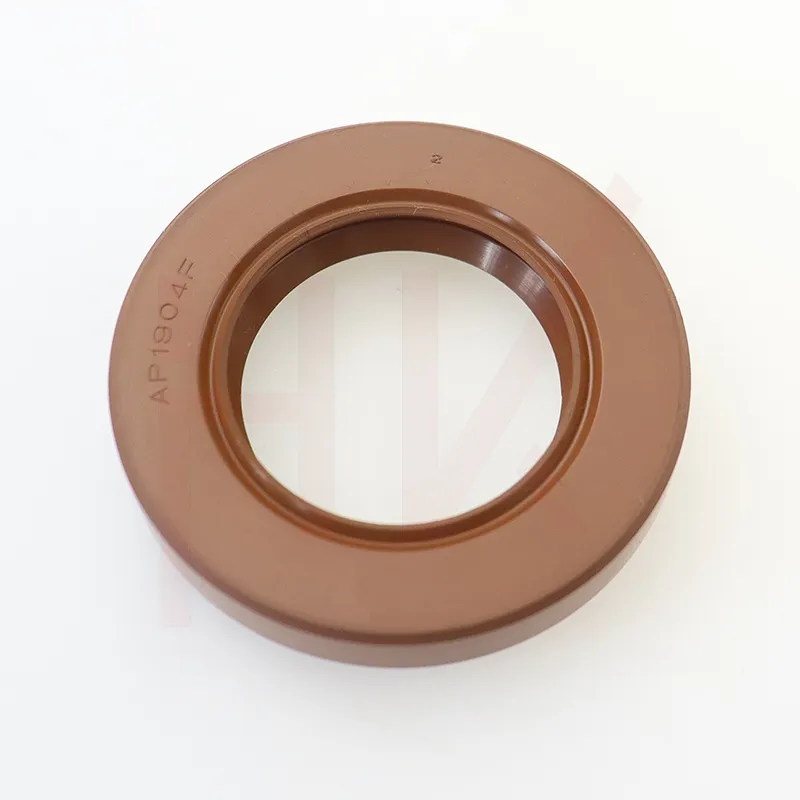
Navigating the world of rotating machinery demands precision, efficiency, and reliability. At the heart of such machinery often lies a component that might seem inconspicuous, yet is crucial the oil seal. These seals are fundamental in ensuring optimal performance and longevity of various mechanical equipment.
The primary function of an oil seal is to retain lubricants within a chamber while preventing the intrusion of contaminants.
This is essential for maintaining the integrity of the lubricating oil in systems involving rotating shafts. Without an effective oil seal, the potential for leakage increases, leading to reduced performance and possible damage due to contamination and excessive friction. Therefore, understanding the specifics about oil seals and their appropriate application is indispensable.
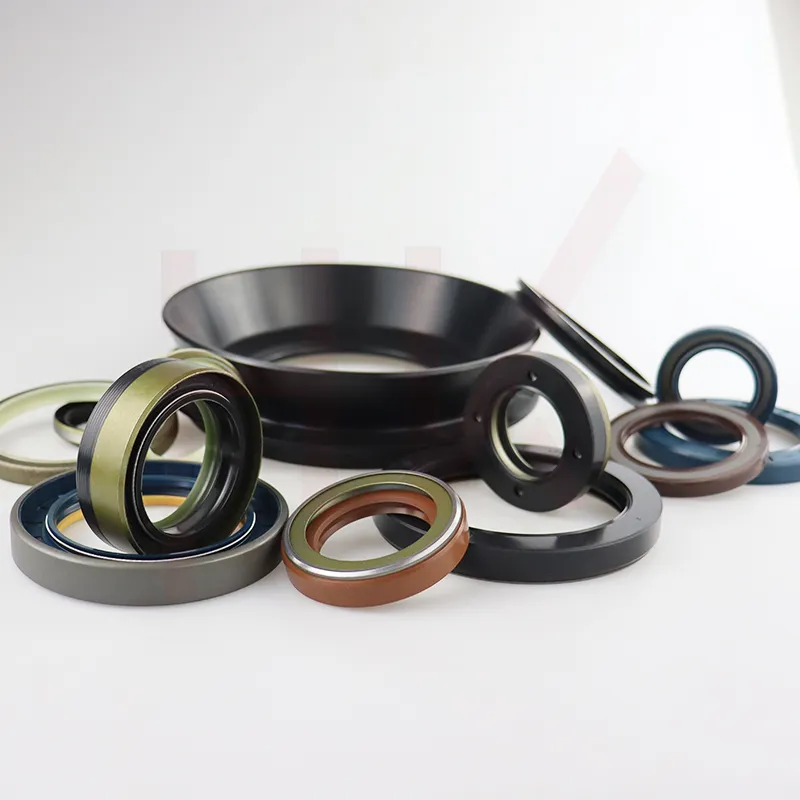
While there are many different types of oil seals available, each serving unique purposes, they all share the common goal of enhancing an equipment’s performance. For example, in automotive engines or industrial gearboxes, oil seals are tailored to withstand high temperatures and pressures. The materials used in these seals often include synthetic rubbers such as nitrile or silicone, designed to resist wear and chemical degradation over extended periods. Professionals selecting an oil seal must therefore have a profound understanding of the operating environment to ensure a perfect match in material and design.
Experts in mechanical engineering emphasize the importance of considering factors such as shaft speed, pressure, temperature, and the specific lubricant used, as each of these aspects can significantly impact the efficacy of the oil seal. A mismatch in any of these areas can lead to premature seal failure, which in turn could disrupt operations and lead to costly repairs.
oil seal for rotating shaft
Furthermore, technological advancements have paved the way for innovations in oil seal designs. Modern seals often incorporate advanced geometries and materials to cater to more demanding applications. For instance, dual lip seals provide enhanced protection by offering an additional sealing surface, thereby effectively preventing both fluid leakage and ingress of external contaminants.
Authoritative sources underline the cost-effectiveness of maintaining high-quality oil seals. Regular monitoring and timely replacement of worn seals can avert the substantial costs associated with mechanical downtime. Equipment operators are encouraged to conduct routine inspections and engage qualified professionals for the maintenance and replacement of seals to uphold the machinery’s operational efficiency.
Companies manufacturing oil seals play a critical role in this ecosystem. They not only supply high-quality seals but also offer expert guidance on selection and installation. Choosing a reputable supplier that demonstrates trustworthiness and competence is key to ensuring the reliability of the seals used. Such suppliers often stand behind their products with warranties and technical support, reinforcing the trust placed in them by industry professionals.
The reliability of machinery and equipment heavily depends on the seemingly minor components like oil seals. Those with professional expertise acknowledge the profound impacts these seals have on overall mechanical performance. By selecting the right type of seal, incorporating latest technologies, and adhering to proper maintenance regimes, machinery performance can be optimized, leading to increased safety, reduced operational costs, and extended lifespan of the equipment.
Ultimately, an oil seal’s effectiveness can be attributed to its design, material composition, and the precision with which it is deployed. The insights and considerations shared by experts in the field are vital in achieving the delicate balance between maintaining performance standards and minimizing costs. Thus, oil seals, though small in size, wield great significance in industrial applications involving rotating shafts.