Oil seals for pumps play a critical role in ensuring the smooth operation of various industrial and household pump systems. As an essential component, they provide both durability and efficiency by keeping lubricants sealed in while preventing contaminants from entering the pump mechanism. But finding the right oil seal involves understanding their types, materials, mechanisms, and choosing the one that accurately fits the pump’s operational environment.

The significance of oil seals for pumps cannot be overstated. These seals mainly function to prevent leakage of the lubricating oil, which is crucial in avoiding wear and tear on bearings and other rotating components. More specifically, they serve as a barrier that not only keeps the lubricant intact but also impedes dirt, dust, and moisture from coming into contact with sensitive internal components.
Several factors influence the performance and longevity of oil seals, which is why expertise in material science and mechanical design becomes integral. For instance, the choice of material for an oil seal can considerably affect its performance under different environmental conditions. Common materials include nitrile rubber, fluorocarbon, silicone, and polyacrylate, each offering varying levels of resistance to heat, oil, and abrasion. Nitrile rubber is valued for its affordability and moderate resistance to oil, making it a popular choice in general applications. On the other hand, fluorocarbon seals provide exceptional thermal and chemical resistance, suitable for more demanding conditions.
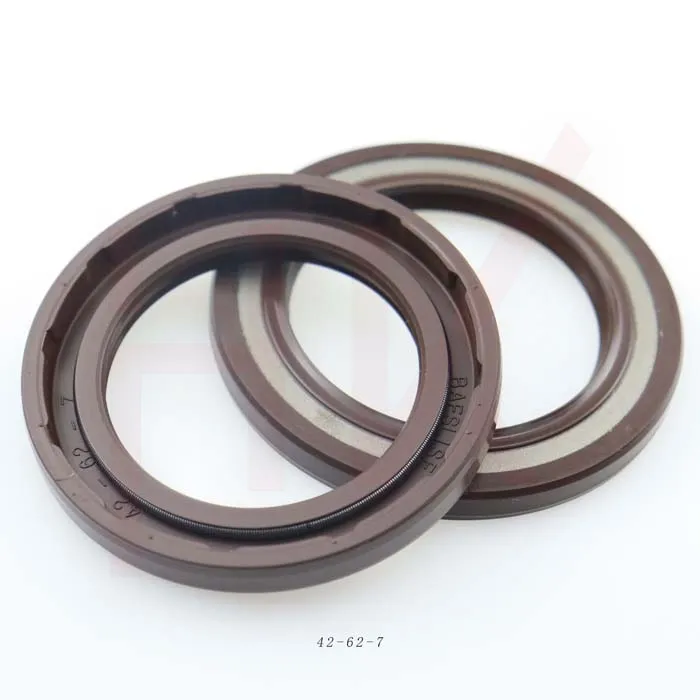
The design of oil seals is also pivotal to their function. Seals can be classified based on their structure as single lip or double lip types. Single lip seals are efficient for basic tasks, where contamination risks are minimal. Conversely, double lip seals offer an additional lip which serves as a secondary barrier against external contaminants, ideal for more stringent applications.
Having authoritative knowledge about oil clutch seal alternatives offers a competitive edge in selecting the right type for precise applications. It's equally important to consult with professionals to ensure seals are aligned with the operational parameters such as shaft speed, temperature range, and environmental conditions. Misjudgment in these aspects can result in seal failure leading to mechanical downtime and expensive repairs.
oil seal for pump
Proper installation is another area demanding attention and professional expertise. The installation process should be carried out meticulously to ensure that the seal is seated correctly around the shaft. This involves cleaning the shaft, checking for any sharp edges that could harm the seal during installation, and cautiously introducing the seal into its housing. Lubricating the seal with a suitable oil or grease aids in smooth installation and reduces initial startup friction.
Furthermore, for trustworthy operation, regular inspection and maintenance routines are recommended. Oil seals should be examined for signs of wear or damage such as cracking, hardening, or swelling. Early detection of these signs enables the proactive maintenance or replacement of seals before significant wear results in substantial damage.
The authority of information regarding oil seals can often be attributed to collaborative efforts between experienced engineers and skilled industrial professionals. Research and development teams consistently explore advancements in material technology and sealing mechanisms, ensuring the evolution of oil seal products alongside industry advancements.
In conclusion, oil seals are indispensable to pump systems, significantly contributing to the efficiency and longevity of machinery by performing vital protective functions. Expertise in selecting appropriate materials and designs, paired with authoritative installation and maintenance practices, ensures trustworthy and sustainable operation of pumps across varied applications. Leveraging accumulated industry knowledge not only optimizes performance but also extends the lifecycle of essential mechanical systems, underscoring the oil seal’s pivotal role in modern engineering.