In the industrial world, the oil pump seal might not captivate attention like other components, yet its importance is undeniable. An expertly designed and well-maintained oil pump seal ensures the smooth operation of machinery, preventing costly downtimes and enhancing the longevity of expensive equipment. Let’s delve into why these seals are a cornerstone of industrial efficiency and how they have evolved to meet modern demands with optimum performance.
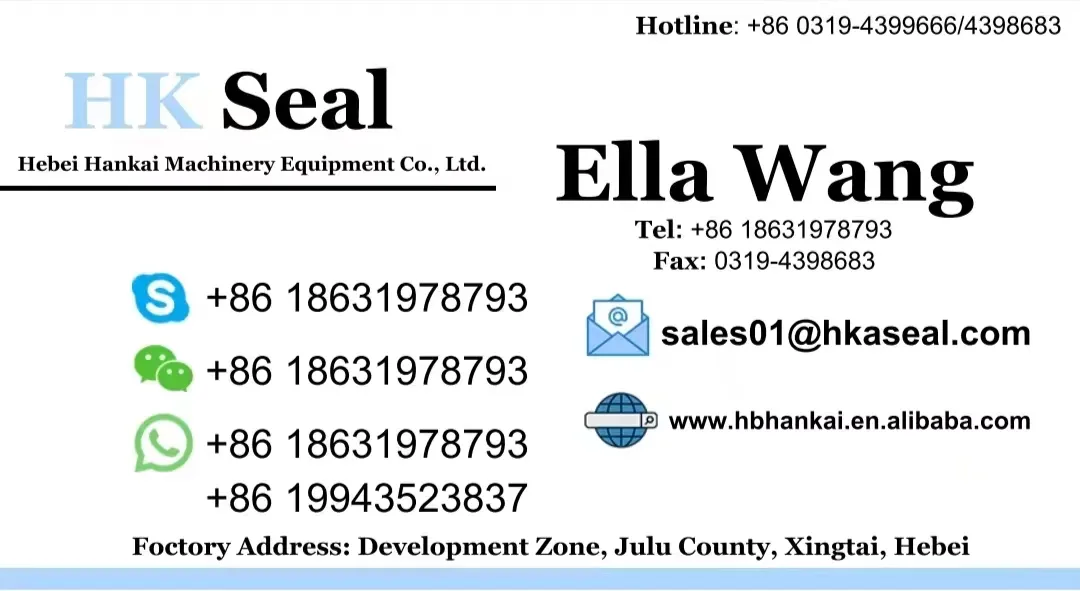
First and foremost, the primary function of an oil pump seal is straightforward to prevent the leakage of oil. However, doing so effectively requires an understanding of not only the machinery it serves but also the environmental conditions it operates within. The expertise in designing these seals involves careful consideration of factors like temperature ranges, pressure variability, and chemical exposures, all of which can drastically affect seal integrity.
When it comes to the material composition, choosing the right compound is crucial for any viable oil pump seal. High-quality seals are crafted from durable, resilient materials such as Nitrile, Viton, or PTFE, each offering unique benefits that cater to specific industrial needs. For instance, Viton seals are prized for their high-temperature resistance and chemical stability, making them invaluable in high-performance applications.
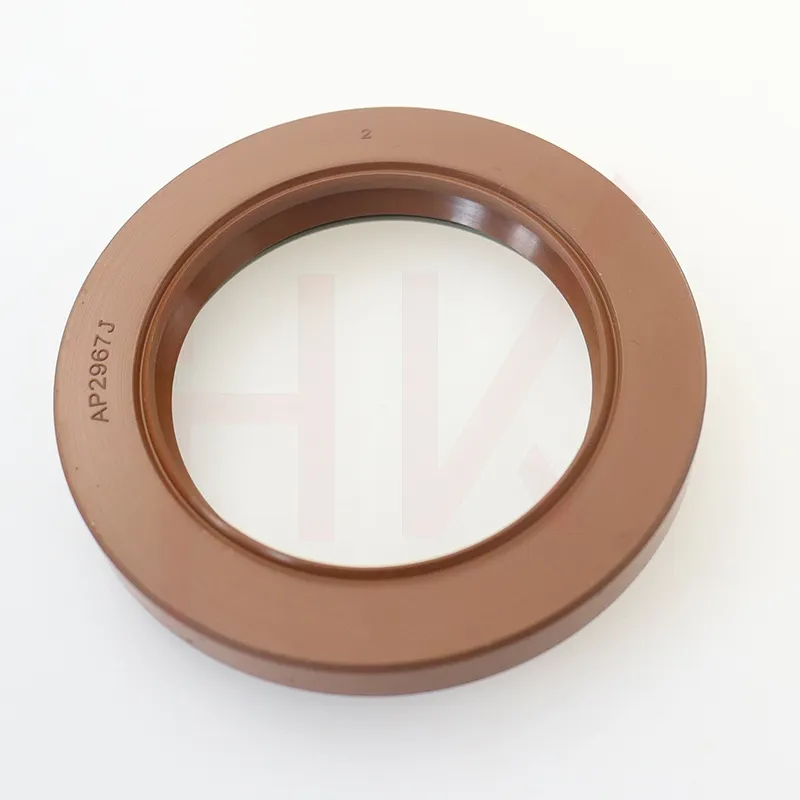
Beyond materials, the design sophistication of oil pump seals plays a critical role in their effectiveness. Over the years, designs have advanced from simple lip seals to more complex arrangements like mechanical seals, which provide better resistance to wear and tear. Such advancements underscore the expertise involved in seal engineering, combining principles from fluid dynamics and material science to create something that can withstand intense operational stress.
Expertise doesn't just end at creation. Installation and maintenance are equally vital in ensuring an oil pump seal performs at peak capacity. Incorrect installation can lead to a variety of problems including premature failure, leakage, or excessive wear. Trustworthy seal suppliers provide detailed guides and support services to assist engineers in the proper assembly and maintenance of these components, reflecting the authoritative nature of established manufacturers in the field.
oil pump seal
The authoritativeness of a seal manufacturer can often be gauged by their adherence to international standards such as ISO 9001. This certification underlines an assurance of quality and consistency, encouraging trust in their products. A reliable oil pump seal is not only about preventing leakage but also about maintaining trust between the manufacturer and end-user, ensuring that every piece delivered is of the highest standard.
From a real-world experience standpoint, industries ranging from automotive to aerospace have documented significant improvements in operational efficiency and equipment lifespan through the use of superior oil pump seals. These success stories are not just marketing anecdotes; they are testimony to skilled engineering and the robust nature of these small yet mighty components.
Integrating the latest sealing technology with insights from data analytics and field experiences enriches the development and application of oil pump seals. Companies leveraging such technologies can predict potential failures and proactively address them, significantly reducing the risk of unforeseen breakdowns.
Therefore, when considering the acquisition of oil pump seals, it’s imperative to prioritize not merely cost but to assess the long-term benefits and expertise of the supplier. With a focus on expertise, authoritativeness, and trustworthiness, a high-quality oil pump seal serves as a linchpin in maintaining machinery efficiency, guaranteeing peace of mind and operational success across industries worldwide.