In the ever-evolving world of industrial machinery and automotive components,
maintaining the integrity and performance of systems is paramount. One critical component often overlooked but essential for optimal functionality is the metal wiper seal. These seals operate under harsh conditions, offering protection and efficiency in various applications, from hydraulic systems to automotive machinery. As we delve into the intricacies of metal wiper seals, we uncover their indispensable role in ensuring longevity and performance in mechanical systems.
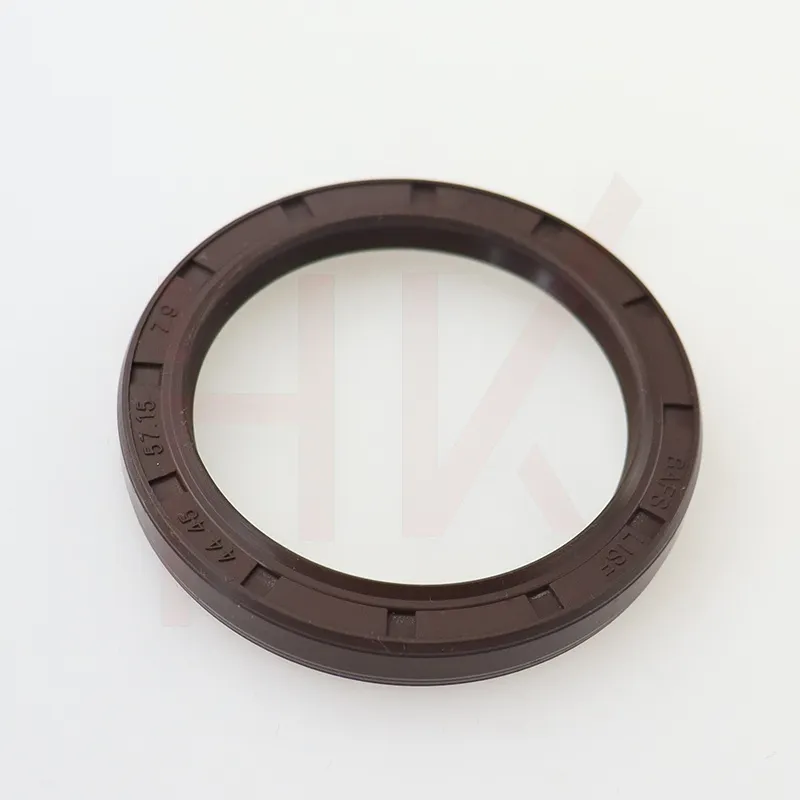
Metal wiper seals, also known as scraper seals, are designed to prevent external contaminants like dirt, dust, and moisture from entering and damaging the hydraulic cylinder or actuator components. The seal achieves this by wiping the rod or shaft as it moves in and out. Made from robust materials like stainless steel, these seals are engineered to withstand extreme temperatures, pressure, and abrasive substances, making them an excellent choice for heavy-duty applications.
A key feature of metal wiper seals is their durability. Unlike their polyurethane or rubber counterparts, metal seals provide exceptional wear resistance and mechanical strength, which are critical in high-load and high-speed environments. Industries such as construction, agriculture, and mining often operate in settings where equipment is exposed to abrasive particles and harsh weather conditions. In these environments, metal wiper seals prove superior due to their resistance to wear and tear, extending the lifespan of machinery and reducing maintenance costs.
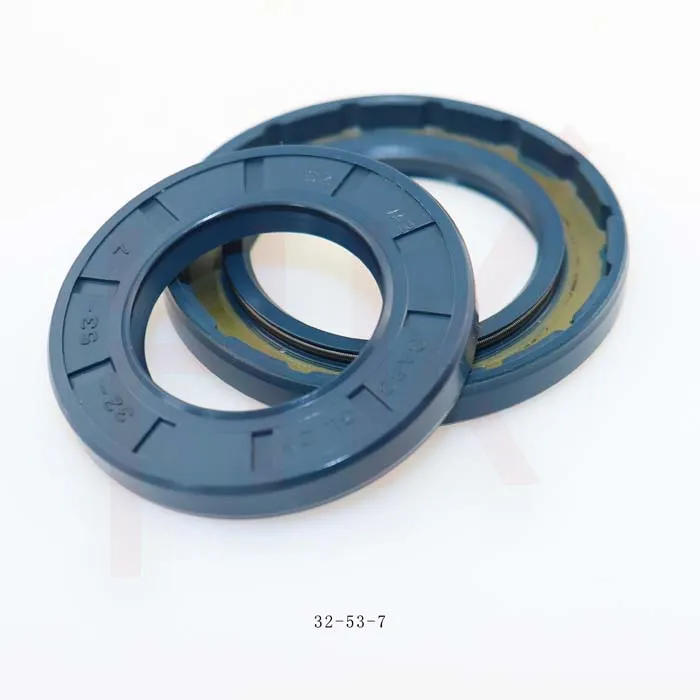
Real-world applications of metal wiper seals demonstrate their indispensability. In the aerospace industry, these seals are employed in landing gear and flight controls, where reliability is not just advantageous but lifesaving. The precision with which metal wiper seals are crafted ensures that they can function effectively in high-altitude, low-temperature conditions where other materials might fail. This expertise in manufacturing, coupled with rigorous testing, establishes metal wiper seals as an authoritative choice for such critical applications.
metal wiper seal
Furthermore, metal wiper seals contribute significantly to system efficiency. By preventing the ingress of contaminants, these seals reduce the likelihood of mechanical failure and downtime. The implications of such efficiency are vast—machinery that runs smoothly not only conserves energy but also operates with reduced friction, enhancing overall productivity. In manufacturing units and industrial plants, this efficiency translates to cost savings and increased output, a testament to the authoritative nature of metal wiper seals in industrial optimization.
Trustworthiness in metal wiper seals is established through stringent quality control processes. Manufacturers adhere to international standards, ensuring that each seal meets requisite specifications for performance and safety. This adherence not only instills confidence in industries that choose metal wiper seals but also underscores their reliability in critical applications. Moreover, innovations in manufacturing processes and materials continue to enhance the functionality and performance of these seals, setting a benchmark for quality and dependability.
In conclusion, the role of metal wiper seals in maintaining the efficiency and longevity of mechanical systems cannot be overstated. Their durability, robust design, and ability to operate under extreme conditions make them a superior choice across various industries. From aerospace to heavy machinery, metal wiper seals provide the necessary protection against contaminants, ensuring that equipment functions optimally with minimal maintenance. As industries continue to evolve and face new challenges, the experience and expertise underpinning the design and application of metal wiper seals will remain central to advancements in mechanical engineering and system efficiency. As such, they hold a position of authority and trust in an ever-demanding industrial landscape, making them an essential component in the pursuit of operational excellence.